Getting Answers through Lubricant Condition Monitoring
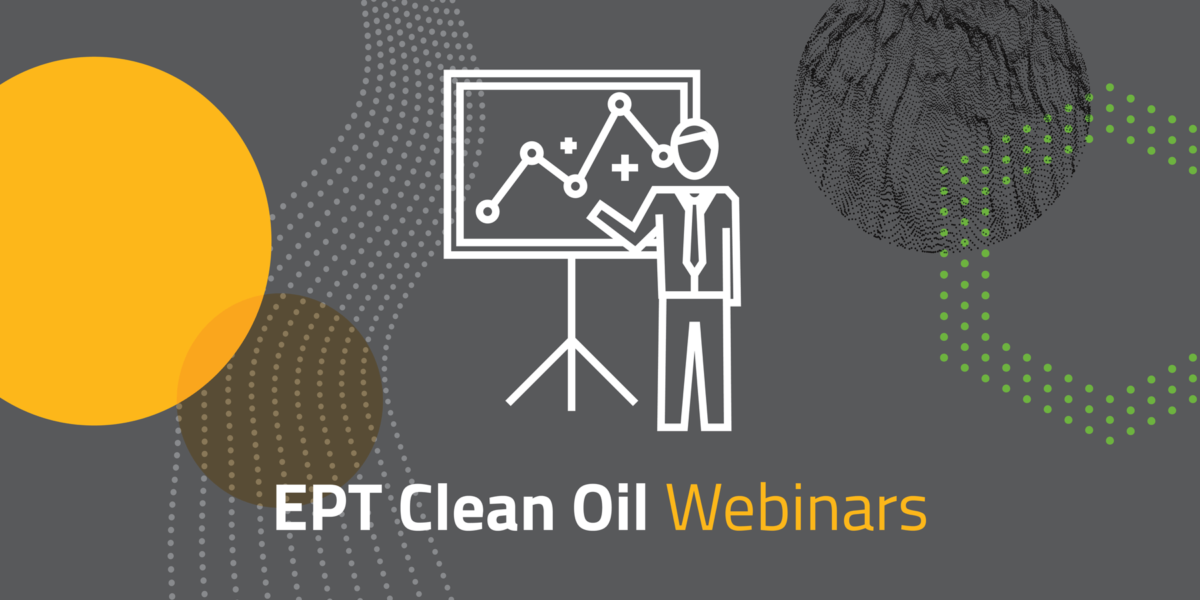
Connect the dots between critical rotating equipment lubricant condition monitoring and truly effective maintenance.
When it comes to critical rotating equipment, lubricant condition monitoring and effective maintenance are essential. Unfortunately, many operators recognize that lubricant condition monitoring is vital to their maintenance program but do not fully understand their oil analysis results. As a result, reports often leave end-users with more questions than answers.
Subject Matter Expert, Dr. Matt Hobbs, shares his secrets for lubricant condition monitoring in the below webinar.
Lubricant condition monitoring starts with the right tests, at the right time and to the right international ASTM standards.
We highly recommend adopting and understanding the following three ASTM standards, written by subject matter experts and approved by various stakeholders, including equipment OEMs, fluid suppliers, filtration vendors, and fluid analysis labs.
- ASTM D4378: Standard Practice for In-Service Monitoring of Mineral Turbine Oils for Steam, Gas, and Combined Cycle Turbines
- ASTM D8323: Standard Guide for Management of In-Service Phosphate Ester-based Fluids for Steam Turbine Electro-Hydraulic Control (EHC) Systems
- ASTM D6224: Standard Practice for In-Service Monitoring of Lubricating Oil for Auxiliary Power Plant Equipment
Armed with the right ASTM standards, the next step in lubricant condition monitoring is understanding what your oil analysis results are telling you by answering four key questions.
1. Will my oil still do its job as it is right now?
It would be best to look at the oil’s physical properties and viscosity to answer that question. If your viscosity is too low, your fluid is too runny, which can lead to inadequate lubrication. And if you have insufficient lubrication in a bearing application, for instance, you’re going to have metal-on-metal contact. If your viscosity is too high, your fluid is thick and viscous, resulting in reduced efficiency and excess friction, which heats everything, and that will lead to oil breakdown down the road.
2. Could an immediate failure occur, or is there an imminent failure in progress?
To answer that question, you need to look at contaminant levels in your fluid, including particles, water and metals.
Particles
Insolubles abrasives that result in equipment wear and ultimately can lead to failure. If you have a system with tight clearances, particles can plug up those clearances and lead to oil starvation, leading to failure. Similarly, oil filters can plug and can starve oil systems downstream. And finally, particles can also catalyze oil breakdown.
So how does oil analysis measure insoluble levels?
An ISO particle count is the most common way of doing so. It is a three-number code. To crack that code and understand your particle count results, you need to understand those three numbers. The first number is the number of particles in your sample greater than 4 microns. The following middle number is the number of particles greater than 6 microns in size. And finally, the last number is the number of particles greater than 14 microns in size.
So particle count gives is not only a valuable tool for quantifying insoluble contamination in your oil, but it also classifies it out according to size.
One thing that is essential to be aware of with ISO particle counts is that each increase of one ISO code indicates a doubling of the number of particles present. So, essentially, this is an exponential scale, and some end users are not aware of that.
What are your particle count limits?
These will vary by OEM, and they will also vary by application. For a steam turbine or gas turbine lube oil, D4378 is your relevant standard, and it outlines an 18/16/13 maximum level. You want to make sure you never cross that line. Lower is better.
D8323 is your relevant standard for EHC fluids and steam turbine oils for hydraulic applications. It would be best to have a tighter particle count due to tight clearances in those systems. So in that application, the line is drawn at 16/14/11 as the maximum allowable particle count. But once again, lower is better.
If your particle count is high and if you have high levels of insoluble, what can you do?
Filtration is your solution. OEM built-in filter systems require filter changes to eliminate exhausted filters. An exhausted filter will no longer be able to perform the job demanded. Another option is to upgrade standard filters as the current filter may be letting fine particles through. If you want to take it a step further, you can go to the kidney loop filter cart or even a larger kidney loop, filtration skid.
Water
Oil and water don’t mix. If you get water into your system, the consequences can be severe. Wear can result, which can lead to failure. Corrosion can result when we have water. And water finally also leads to oil breakdown. When an oil analysis lab measures water, the end-users are sometimes unaware that labs can use various test methods to measure water.
Karl Fischer titration or KF, Relative Humidity Sensors – RH, FTIR spectroscopy, or crackle tests are all commonly employed by commercial labs. It’s essential to be aware that not all tests are created equally. In particular, I would suggest that a crackle test is not helpful in a critical application.
I’m also a little bit dubious when it comes to FTIR. It can be a practical test, but commercial oil analysis labs love this test because it takes them about 1 second to run, it’s straightforward to automate, and it provides about six different results. I’m hesitant to use it for water because there are a lot of interferences in oil samples that can potentially make water measurements unreliable. And repeatability for FTIR is ill-defined.
I would suggest that your lab should probably use Karl Fischer titration, which is nicely amenable to a lab measurement of water.
What are the limits?
These will vary by OEM and application. I can’t speak to every OEM out there, but with regards to application, we’ll look at D4378 for lube oils – they call for 200 ppm of water, max. This is the line in the sand that you do not cross. So above 200 parts per million water in your oil, you’re going to have free water, and that’s going to lead to wear and potential failure.
Concerning ester-based hydraulic oils, D8323 defines a limit as more of a range: 300 to 500 ppm. We’re a little higher here because ester-based oils are hygroscopic. They will pull water out of the atmosphere and take it in. It’s harder to keep them dry, but you want to do your best because ester-based oils will also react with water that they pull in from the atmosphere or any contaminant water for that matter.
That reaction is called hydrolysis, and it breaks down the base oil molecule and cleaves it into its constituent parts, which occur when water levels are above 500 ppm.
What do you do if you do get water into your oil?
Your first action item should identify that water source and correct it if possible. So in a steam turbine application, this could be a seal leak, and you should fix that seal leak. Anything you do down this list on the bullet points lower than that is only managing water levels, but it’s not fixing the root cause of the water ingression. Water will still keep getting in unless you fix your problem. Things like centrifuges and coalescers are valuable tools for separating water from oil, but they rely on the oil having good demulsibility and oil-water separability.
Vacuum dehydration is also very useful if you’ve got to do a bulk clean-up. If you get a lot of water in your oil and need it out fast, vacuum dehydration is the way to go. Water is more volatile than oil, so if you put it under vacuum and you heat it, the water will evaporate out of the oil.
Finally, a nitrogen gas blanket is a valuable tool for keeping oil dry. It’s not quite as fast as vacuum dehydration, but it doesn’t beat up the oil as much. A dry gas blanket prevents the oil from taking water from the atmosphere.
Metals
Metals can come from different places, so it’s essential to know where all these metals can come from. Common sources of metals in your fluid can be things like wear. And in that instance, you want to look out for metals like iron, copper, chromium, nickel, aluminum and titanium, to name a few. Another common source of metals is additives, so calcium, magnesium, zinc. These are common additives in AW Oil packages. (D4378 provides a complete list of the familiar sources of all twenty of these metals.)
What are the consequences if metals get into your system?
Metals can accelerate oil breakdown. They behave as catalysts, catalyzing increased oxidation, hydrolysis, etc., which leads to oil breakdown. They also promote deposit formation because they can lead to gels and sludges. And finally, they contribute to wear.
You can manage metal levels with patented ICB® ion-exchange, but managing doesn’t correct the underlying cause. You’re just filtering off the results of that problem, and you’re covering up the evidence, so it’s essential to identify the root cause.
3. Is there any decent likelihood of a future failure in this system?
To answer that question, you need to look at oil breakdown levels. Breakdown products impair reliability and, in extreme cases, impact fundamental oil properties like viscosity.
So let’s take a look at some of these breakdown products and discuss them in more detail here.
Acids
They are corrosive and can eat away at the metal surfaces in your system. They also promote deposit formation (varnish precursors). Finally, acids are catalysts, accelerating oil breakdown and shortening your oil’s life.
Where do these acids come from?
The most common source of acids is oxidation. Oxygen is in the air all around us, which is not suitable for our turbine oils because oxygen is an incredibly reactive molecule that reacts indiscriminately with base oil molecules. And when it does, it degrades them, forming oxidation products, the most common of which are weak organic acids.
Another potential source of acid formation is hydrolysis if you’re using an ester-based lubricant. It can react with contaminant water, which cleaves the ester into its constituent parts. Now, one of those parts will be acid, and in the case of phosphate esters used in EHC applications, that will be a strong acid. And this is significant because strong acids are more harmful than their weak acid counterparts.
If you have strong acids in your system, your problem is more severe.
How do we measure acid number?
Two standard test methods can be used to measure acid number. ASTM D664 is a potentiometric method, and ASTM D974 is a visual-manual method. So, which of these methods is better? In my opinion, ASTM D664, the potentiometric method, is more reliable because you’re using an electrode to measure acid levels in the fluid. And you can get more information still out of that because you can determine whether the acids that were present were strong or weak. So, D664 allows you to report strong acid numbers. And the acid number is the total acid number. So it’s the sum of the weak acids and strong acids in a system.
What are our recommended limits for acid number?
ASTM D4378 has a complicated way of defining these limits in lube oil applications. So for oils that are under 20,000 hours in-service, the limit is defined as a change in acid number, up or down of 0.1 per year. So if you have your acid number increased by 0.15 in the first year of service, you have a problem according to D4378. Now they relaxed that a little to 0.15 as the oil ages. Older oil is going to break down more.
For phosphate-ester-based fluids, the limit’s a lot easier. It’s a simple line in the sand, 0.20 acid number max, and you don’t cross that line. You are out of specification if you were operating above that acid number.
What can you do if you get acid in your system or if acids have accumulated in your system? Well, acid filters are available to remove those acids. Our patented ICB® ion-exchange filters are a great option. If you’re already using ICB filters and acids are accumulating, that’s probably suggesting that the acid filters have exhausted. Each of these filters has a finite capacity. They can remove only so much acid, and once they’ve removed all that acid, they’re not doing any good. So you need to change the filters if you start to see acid levels increasing.
And finally, more of a preventative maintenance thing is ensuring that your antioxidant levels are sufficient if you’re using a lube oil because acids form as the result of oxidation. Antioxidants mitigate the risk of oxidation. So if you have antioxidants at reasonable levels in your fluid, you shouldn’t see the acid formation. So keep your antioxidant levels high.
Varnish
Varnish is the most common cause of oil-related downtime in gas turbine applications. And it doesn’t just affect gas turbines; it also affects steam turbines, compressors, and hydraulic systems. So it’s something to be broadly aware of. But gas turbines are certainly the most famous examples of varnish-related failures.
What is varnish?
Varnish is essentially a complex mixture of oil breakdown products. And these oil breakdown products are soluble or dissolved within the oil. Still, the problem is they have some propensity to come out, to precipitate from solution, at which point they become solids – they become insoluble. And when they do, that leads to the famously associated problems with varnish.
Most commonly cited is valve sticking in a gas turbine application, leading to unit trips. Now, varnish doesn’t just lead to valve sticking. Varnish can plug filters, and that can lead to oil starvation. If varnish plates out on a bearing, that can lead to high-temperature operation because you’re increasing friction by reducing clearances. If you have a high-temperature operation, you’re going to increase the rate of oil breakdown.
This is a cycle where breakdown begets more breakdown. It would be best to stay on top of breakdown levels to ensure they don’t get out of control. If you reduce clearances by varnish depositing out on surfaces, you can have equipment wear, leading to failure.
If you have a heater or a cooler in your application, varnish can coat out on cooler surfaces. If you’re relying on that cooler to bring your gas turbine oil’s temperature back down, for instance, if you have sludge all over the walls of that cooler, it’s not going to do a good job. We’ve seen cases where end users have to de-rate their turbine because they can’t run it full out. After all, there’s so much varnish on their cooler walls. They can’t cool the oil down effectively if the turbine’s running at its capacity.
How do we measure varnish?
We measure varnish potential using membrane patch colorimetry or MPC testing for short outlined by ASTM D7843-21. Essentially, it’s a filter patch test method. These are 0.45-micron patches, and to isolate varnish and other oil breakdown products from the fluid, we pass them through the patch.
Varnish that is dissolved is going to pass right through a patch. The MPC test mixes your oil sample with a non-polar solvent. And that crashes some of the soluble varnish present out of solution. And once it’s insoluble, you can catch it with a filter, detect it, and see it.
How does the MPC test work?
Essentially, the intensity of the colour of the stain on the patch is our varnish, and the intensity of that colour is quantified by Delta E using a spectrophotometer. High Delta E values mean you have a high varnish potential. So dark patch, high Delta E, high varnish potential.
One word of caution here. Don’t look only at MPC Delta E; look at the patch photo as well.
In addition to reporting that Delta E value, ASTM D7843 also requires that labs report the 72-hour test hold time. This is the crucial sample prep step used in the MPC test and directed by the MPC test method. The ASTM method requires that this be reported. If it isn’t being reported, how sure are you that they’re doing the test the way they’re supposed to be?
This step is used to ensure that varnish becomes somewhat insoluble so that the lab filter patch can capture it and it can be detected.
What are the recommended limits?
Well, D4378 and D8323 are in alignment concerning the relative limits. They set a warning limit at a Delta E greater than 20 and an action limit greater than 30.
Now again, these aren’t target values; these are limits. These are lines that you do not cross. Just because you’re operating at a Delta E of 19 doesn’t mean you’re out of the woods; you’re in spec, per se. Again, MPC testing is varnish potential testing. We’re looking at this in terms of a risk spectrum.
So, in theory, Delta E of 19 is a lower risk than a Delta E of 21. Still, the only way to ensure the performance and reliability of a critical asset is to make sure you’re operating at a near-zero varnish potential. So regardless of the limits, your target for MPC varnish potential should be as close to zero as is possible.
What do you do if you do have varnish in a system?
We offer soluble varnish removal skids – SVR® that utilize our patented ICB® ion-exchange filters specifically engineered to remove varnish from different lubricant types selectively. You can use these to prevent varnish-related failures.
4. How much longer will my oil last?
It would be best to look at the oil’s remaining lifetime to answer that. Lube oils are formulated with antioxidants – sacrificial additives that protect the base oil from oxidation. There is a direct relationship between antioxidant levels and oil lifetime.
So how do you evaluate your fluid’s remaining lifetime?
Well, two standard test methods are used to do this. RPVOT and LSV. LSV stands for linear sweep voltammetry, referred to by ASTM (also known by some as the RULER test, which is the trade name of one of the instruments used to measure this.)
The RPVOT test degrades the oil, measuring how long it takes to oxidize it.
The LSV test looks at the remaining antioxidant levels, specifically amines and phenols. This is reported as the percent amine or the percent phenol in the fluid. You have 100% of your antioxidants left when starting with virgin oil. As that fluid goes into service, those antioxidants get consumed.
What are the limits?
The limits are aligned for both of these tests. 25% virgin oil levels are the limits. So for RPVOT, that means if your virgin oil took a thousand minutes to degrade, your limit is 250 minutes for the in-service oil. Once your RPVOT result is less than 250 minutes, your oil’s remaining lifetime has been exhausted. It would be best to change that fluid.
For LSV similarly, 25% virgin oil levels. So you start it with 100% of your antioxidants. Once that’s depleted down to 25%, you’re getting painfully close or dangerously close to that critical level where oil break down is going to take off like a shot. You’re going to want to take action to address it before it does.
I would suggest with both RPVOT and LSV that you don’t get completely hung up on the exact numbers. The reason for that is that the repeatability of these two test methods is unfortunately poor. They’re practical tests because they give you valuable information, but that information is more useful in terms of trends you see coming out of the data than any one result. Any result can vary by as much as plus or minus five or even 15% for both test methods.
So that means I could take the same oil sample, and I could test it two times using LSV and one time, I might get a result of 80%, and the next time I might get a result of 95%. And that’s the same sample, same test, done the same way, by the same analysts. Before you hit the panic button, I suggest waiting for the next month’s result to come back to accommodate the normal test variation. If the next month you see it going down, and the month after that, you see it going down again, then you have a significant downward trend, and that’s highlighting an issue that you need to take action to correct.
What can you do if your remaining oil life is not so great? Regular top-up can be a handy maintenance tool. At EPT Clean Oil, we advocate for a 5% annual top-up with new virgin oil. So, you’re keeping on top of those additives that deplete naturally during service.
Now, if your oil is more degraded and antioxidants have depleted much more significantly, bleed and feed is another tool at your disposal to bring antioxidant levels up more quickly. In theory, a 25% bleed and feed will increase antioxidant levels by 25%.
Oil replacement is your last resort, but it’s an important one because if your antioxidants have entirely exhausted, and if you have to do a 50% bleed and feed anyways, at a certain point, you may as well replace the oil, and then you get to start fresh. Your oil is protected, and you can keep it protected. And there are ways that you can do that by conserving antioxidants. So if you’re in a situation where you need to replace the oil and you want to make sure that your next fill lasts longer, avoid excessive heat and stress on the fluids.
You can also use SVR®and ICB® because these remove varnish and other oil breakdown products. Like acids, varnish and oil breakdown products are reactive and can react with antioxidants. When they do, they take the antioxidant out of the fluid essentially. They nullify it. And in that respect, the antioxidant never got to do its job – it never got to prevent oxidation as it should. So if you keep low levels of varnish, acids, etc., you can maintain your antioxidants and extend your oil lifetime in that way.
This webinar was hosted, and recorded live on May 27, 2021. If you have questions after viewing this webinar about lubricant condition monitoring, please connect with Matt Hobbs.
Presenter Background: Matthew G. Hobbs is the Senior Chemist at EPT Clean Oil, where he manages research, development and the Fluid Technical Center services. Matthew works with users to provide lubricant contamination solutions in critical industrial applications as a technical expert. Before joining EPT Clean Oil, Matthew obtained his Ph.D. in synthetic chemistry from the University of Calgary and was the General Manager of a National oil analysis laboratory.
Matthew is also an active contributor to ASTM, recognized recently with the Award of Appreciation from ASTM International. This award acknowledges Matthew’s tremendous contributions to the Petroleum Products, Liquid Fuels, and Lubricants Committee. Of note, Matthew was a vital contributor to the updates of the following ASTM Standards: