Oil and Water Shouldn’t Mix: Restoration of Steam Turbine oil Demulsibility
Eliminating Water Contamination from Hydraulic and Lubricating Fluids 101
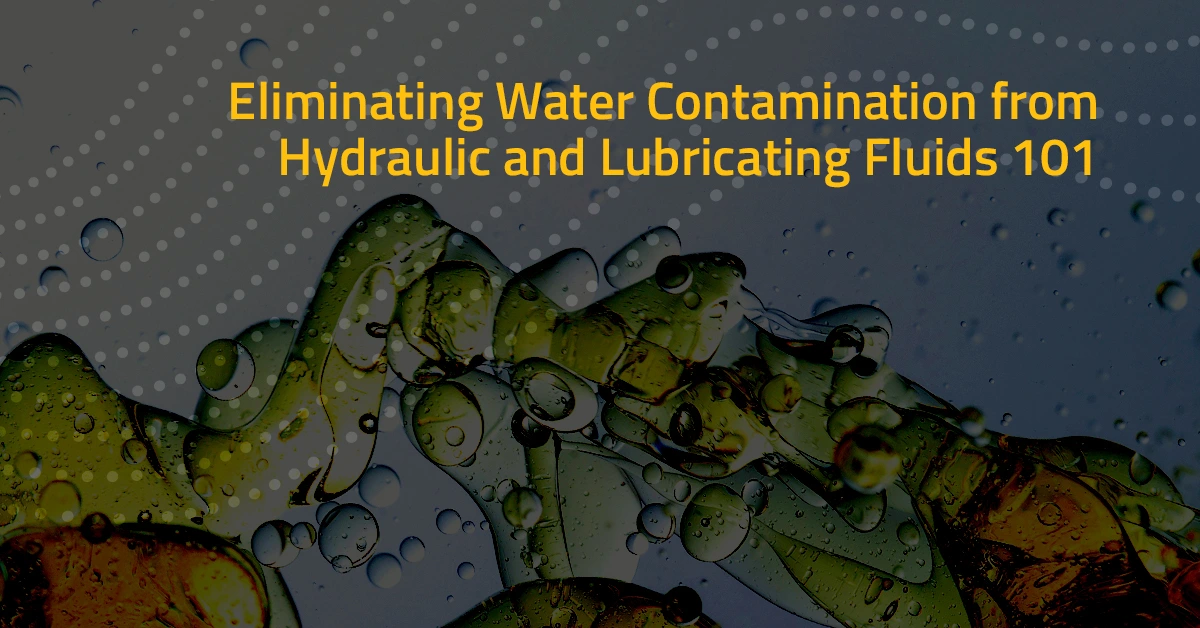
Water is the most damaging contaminant found in hydraulic and lubricating systems. In ester-based lubricants, water reverses the chemical process originally used to manufacture the ester. In mineral oils, water shortens lubricant life by promoting oxidation, acid formation and, in some cases, the removal of additives.
The proactive management of water levels and eliminating water contamination is key to effectively maintaining hydraulic and lubricating systems and managing the drivers of oxidation. Water complications come in three forms: free, emulsified, and dissolved. Free water is the excess water above the fluid’s saturation point and is visible as a separate layer. Dissolved water is below the fluid’s saturation point and is not visible. Emulsified water is the point between free and dissolved, where water first becomes visible as a haze. Conventional maintenance technologies often will remove one form, but not all, frequently resulting in the wrong technology being applied.
It is not understood that in many applications, the primary mode of water ingression is the atmosphere itself. When the atmosphere’s moisture content is higher than the moisture content in the lubricant, the atmosphere provides an unlimited water source.
Our TMR® products are used to remove existing water and, more importantly, to prevent additional water and other atmospheric contamination from entering the system. Reducing water levels in hydraulic and lubricating fluids has been proven to extend equipment life, fluid life and trouble-free operating windows.
Why is water the most damaging and harmful contaminant in hydraulic and lubricating systems?
In ester-based lubricants, water reverses the chemical process originally used to manufacture the ester. In mineral oils, water shortens lubricant life by promoting oxidation, acid formation, and, in some cases, the removal of additives.
What are the industry standard tests for measuring water in lubricating fluids?
ASTM D6304-20: The standard test method for determination of water in petroleum products, lubricating oils and additives, which utilizes the Karl Fischer Titration method and ASTM D7546-15: The standard test method for determination of moisture in new and in-service lubricating oils and additives which utilizes the Relative Humidity Sensor method.
Can breather elements eliminate the ingression of water?
Humid air above the lubricant transfers water through condensation in atmospheric vented systems. While breather elements offer some mitigation, they cannot prevent atmospheric water ingression completely.
What are some key issues plaguing atmospheric breathing lubricant reservoirs?
The lubricant has unlimited access to water when atmospheric moisture levels are greater than lubricant levels, and breather elements cannot reduce existing water levels. They also have limited capacity to reduce condensation and cannot prevent water ingress from the atmosphere via mass transfer. Sea water and industrial environments will also contribute metal ions, increasing the overall lubricant breakdown rate.
How can I extend the life of my mechanical systems and increase reliability?
By adding an effective water removal program to your lubrication maintenance and keeping moisture levels in check, you can significantly reduce water levels and easily double the life of your equipment.
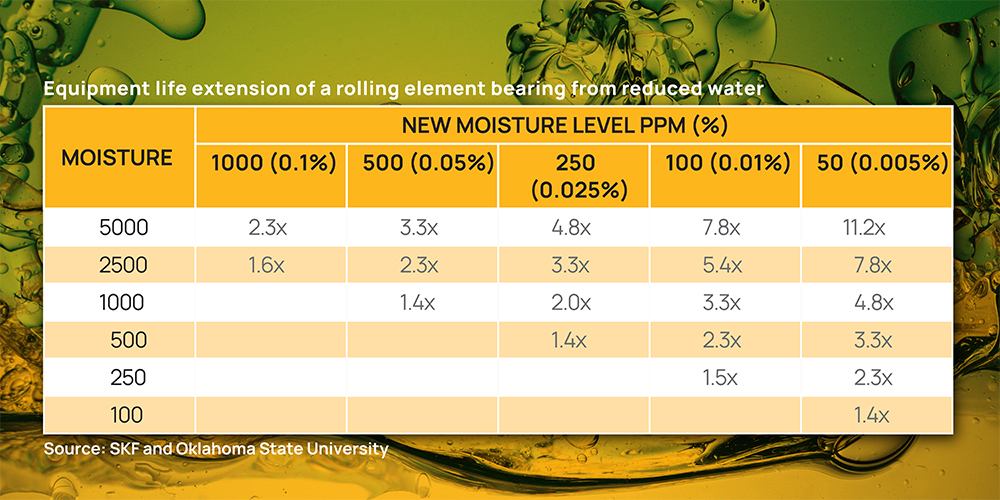
What do I need to consider when choosing a water removal system?
Understanding the source of water contamination is equally essential to understanding water ingression rates. Carefully matching the water removal system’s capabilities with your application is critical. The water removal system must be able to remove the form of water present in your application and remove it according to the amount of water ingress.
What are some of the options for water removal systems?
The major types of water removal systems include: Water Adsorbing Filter, Coalescing Systems, Vacuum Dehydrators, Air Stripping Technology, and Free Flowing Dry Gas Blankets.
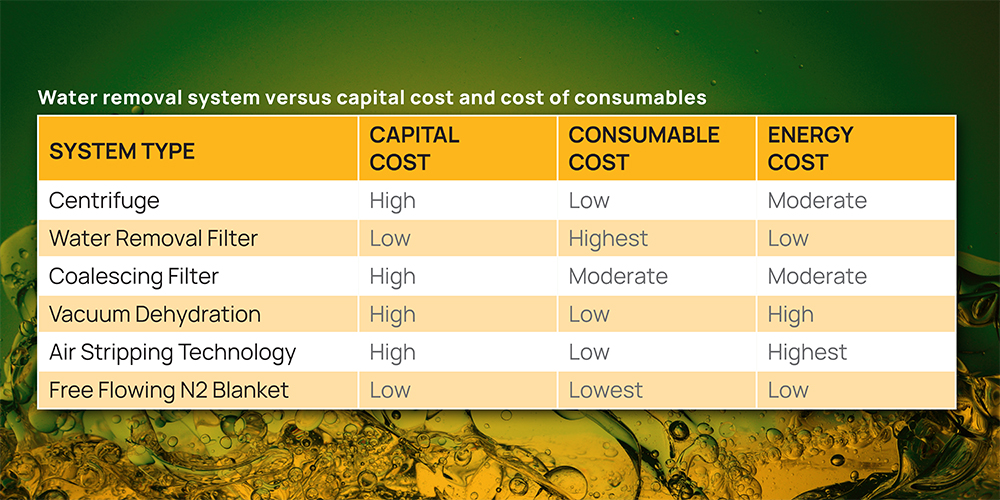
How can I proactively maintain my hydraulic fluid and turbine lube oil to better help manage the drivers of oxidation?
EPT Clean Oil’s TMR™ N2 water removal system provides unlimited capacity to remove water and eliminate atmospheric water ingression via high purity nitrogen introduced into the reservoir headspace above the lubricant surface, forming a nitrogen blanket. As the clean, dry nitrogen gas sweeps across the reservoir, it provides insulation. This eliminates the ingression of atmospheric water and better manages the factors that accelerate oxidation.
What are some of the other benefits of the TMR N2 Water Removal System?
The TMR can help maintain water at very low levels (<50 ppm total or <350 ppm for EHC fluids), reducing the rate of lubricant breakdown. It can also eliminate the lubricants’ contact with oxygen, reducing oxidation and promoting the removal of H2, CO, C2H4 and other harmful breakdown gases, thus, extending fluid life.
Why is it essential to eliminate fluid contact with oxygen, and how does the TMR N2 extend fluid life?
The TMR N2 systems offer the additional benefit of eliminating fluid contact with oxygen, which along with water and metals, comprise the three primary oxidation catalysts. This allows users to move beyond reactionary maintenance and actively manage the factors that accelerate oxidation by continually controlling water and oxygen levels. This eliminates metal ion ingress from the atmosphere, can lower the rate of lubricant breakdown, reduce maintenance requirements, and extend fluid life.