Sustainability – An Holistic Approach of Modern Lubrication Management
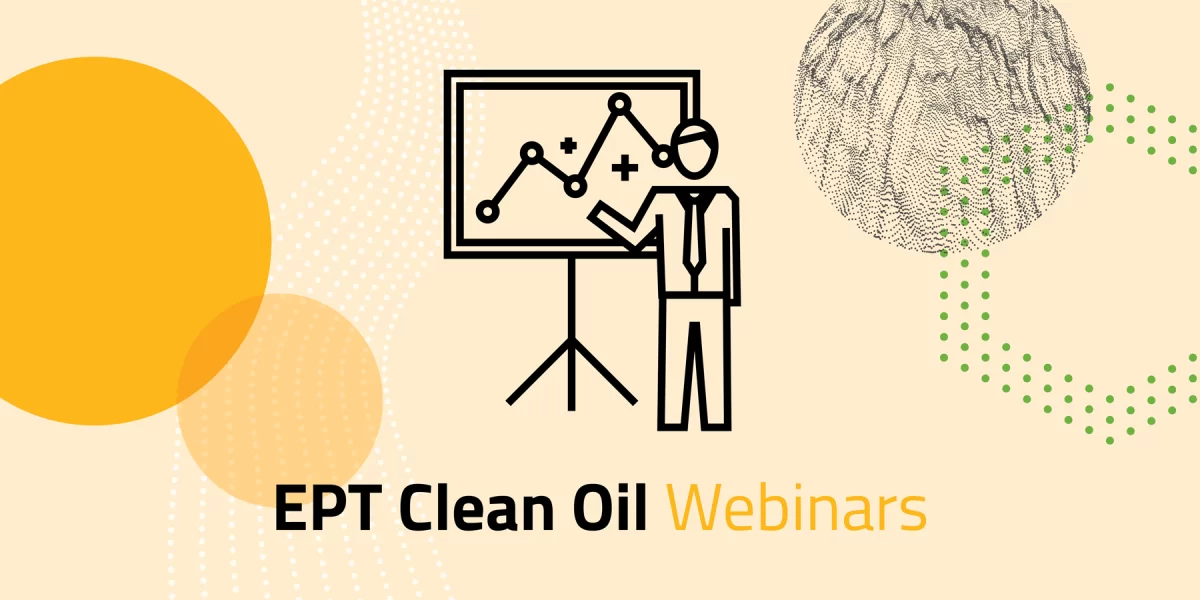
What can we do to effect change in Lubrication Management?
Achieving net-zero by 2050 is arguably the most challenging goal we will undertake in the history of humanity. For hundreds of thousands of years, we have been burning hydrocarbons to heat, cook, protect and ultimately control our destiny. Moving towards net-zero by 2050 will require us to do everything differently, and in a twisted sense of irony, it is necessary again to control our destiny.
We have both the opportunity and responsibility to affect change and adopt more sustainable lubrication management programs in the industries where we work. To start, we need to rethink what we consider an asset and how we manage these assets.
At what volume and at what cost would we consider lubricants to be an asset?
Traditionally lubricants have been viewed as a commodity or consumable item where users operate with it for as long as possible. Then they dispose of it without consideration of maintenance.
What we know to be true – lubricants don’t die suddenly. They die over very long periods, after much abuse and neglect. The challenge is that users have very few problems in the first half of a lubricant’s life, making it easy to turn a blind eye. Somewhere around year 4, the consequences of unmanaged fluid breakdown surface. The result: increased acid number, 30% to 40% additive loss and enough accumulated oxidation material that the lubricant starts depositing on mechanical surfaces.
Lubricant death does not have to be inevitable. There is no reason we cannot double the life of most lubricants or even longer if we start considering what is killing the lubricant and adjusting our maintenance practices to slow down or even manage that process.
It starts with removing unmanaged processes from our programs. While oxidation is unavoidable, the reality is that in many cases, we can reduce its severity and manage outcomes much more efficiently. Oxidation generates dissolved waste material that accumulates in the lubricant, decreasing solubility, accelerating lubricant breakdown, and increasing the rate at which additives are consumed, effectively putting an end of life date on the lubricant.
The wait-and-see approach to oxidation is a big mistake. The result of not managing the consequences of oxidation from day one is lubricant quality deterioration and ultimately equipment failure.
The next step is to remove budgetary constraints. There is a saying that you often get what you pay for. In this case, you don’t get what you don’t pay for: lubricant maintenance and testing. For example, an eighty million dollar failure could have been prevented with forty thousand dollars in maintenance spending. That works out to only eighty cents of new spending to save one million dollars. The business case for increased maintenance is there.
Do you have a lubrication management program that measures the contamination causing equipment and lubricant failure?
Now that you have a budget, the next step is to establish predictability in your oil analysis programs. While this sounds obvious, it is often an aspirational goal because the programs have not been implemented 100%, or gaps are preventing the full benefits of the oil analysis program from being realized.
There are three basic but critical requirements.
- The right test
- At the right time
- To the right standard
There is no point in oil testing if the test method is not followed. Take the MPC varnish test as an example. This test takes almost 100 hours to do when following the international standard. As it turns out, a 100-hour test is not easy for labs to do, so often, a modified test is performed, providing incorrect data that drives poor decision-making.
Establishing predictability within your oil analysis and maintenance program is the best money you can spend. Suppose you can rely on the data and you have the correct analysis at the right time and know-how to interpret that data. In that case, you have compelling predictive information essential for overall lubricant management optimization.
Finally, it is time to evolve past dirt and water removal. Full-time chemistry management within your maintenance programs using ion-exchange technology is a safe and effective approach that offers very predictable outcomes. Ion-exchange filters, the opposite of particulate removal filters, remove dissolved contamination and the accumulation of oxidation material, restoring oil solubility and eliminating varnish formation potential.
The result: acid number and additive consumption rates significantly decrease extending lubricant life. To further extend lubricant life, additive levels can be maintained with 3% to 5% fresh top-up annually using the same brand of lubricant. This eliminates the need for expensive aftermarket chemicals and the complexity of recovering a half-dead lubricant. It is much more cost-effective and sustainable to manage lubricant chemistry from day one.
Lubrication Management Case Study #1
- Baseload gas turbine with 87,000 running hours over twelve years on an R&O Group II base oil.
- Ion-exchange purification technology was utilized from day one, and the customer has been adding 3% to 5% top-up per year.
After twelve years, the acid number has never increased from 0.01, which is better than new, and the MPC value has never been above 1.8, again, better than new oil quality. Using linear sweep voltammetry (LSV), the additive levels reported 87% of the primary antioxidant remains and 64% of the secondary antioxidant remains.
In reviewing the average consumption rate in additive over the twelve years, this works out to 1.1% in the amine and 3% in the phenol per year. This 4500-litre reservoir has already achieved 150% of the typical life and is on track to last another eight to ten years, potentially even for the turbine’s life.
Lubrication Management Case Study #2
- 80 turbo compressors ranging in volume from 4,000 to 12,000 liters
- Fleet has been using ion-exchange technology since 1992 to manage the chemistry on a full-time basis.
An economic analysis published in 2014 showed that 97 million dollars were saved, with savings approaching 1 million per turbo compressor before considering the cost of production losses. Lubricant waste was reduced by 4.2 million liters, and filter waste was reduced by 2.3 million kilograms.
Summary
The combination of robust oil testing and maintenance using ion-exchange technology from day one with small volumes of fresh oil top-up each year has demonstrated the ability to manage oil quality consistently and reduce oxidation rates to levels never previously thought possible.
The road towards a more sustainable future starts with lubrication management and a fundamental decision to be the change you want to see in your lubricant. Break the wasteful, expensive and unsustainable cycle of viewing lubricants as commodities and treat your lubricant like the asset it is.