A Proactive 4 Step Solution to Phosphate Ester Fluid Maintenance Challenges
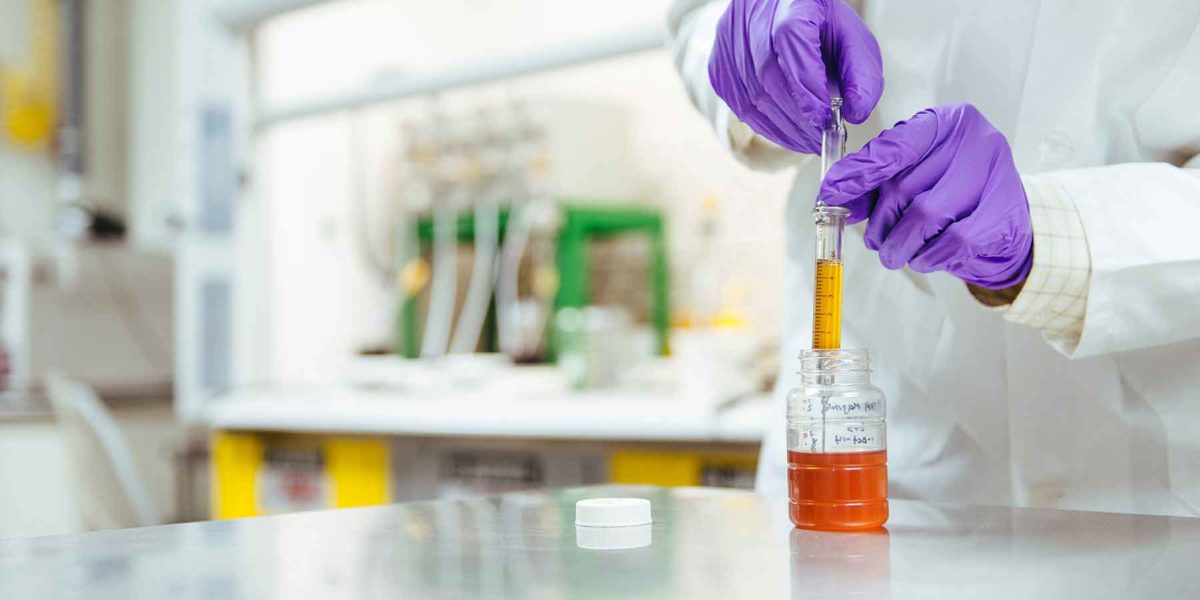

Fluid testing
EPT Clean Oil’s phosphate ester fluid maintenance and testing program measures the hidden contamination that accumulates in most EHC systems. While water, acid and particulate testing is routinely performed, EPT Clean Oil also measures the dissolved breakdown products that are responsible for varnishing, servo valve sticking, low resistivity and high rates of fluid breakdown. Our EHC fluid testing program precisely measures contamination levels to identify problem areas and to track fluid cleaning progress.

Remove the contamination that is responsible for mechanical issues
ICB® filters, a specialized ion exchange product developed by EPT Clean Oil, are used to remove acids as well as the dissolved contaminants that are responsible for servo valve sticking. The ability to remove this contamination using ICB® filters is a game changer for phosphate ester fluid maintenance, significantly improving servo valve operation.

Remove water and prevent atmospheric contamination
Water is the most damaging contaminant found in ester-based hydraulic and lubricating systems. Oil and water don’t mix and water does not possess the lubricating or hydraulic properties required to keep systems operating. Moreover, water actually reacts with phosphate esters turning them into acid. The primary mode of water ingression in most applications is atmosphere itself. When the moisture content of the atmosphere is higher than the moisture content in the lubricant, the atmosphere provides an unlimited source of water. Our TMR™ N2 system can be used to remove existing water and, more importantly, to prevent additional water and other atmospheric contamination from entering the system. As an added benefit, this system also blankets the fluid reservoir with inert nitrogen gas, mitigating the risk of oxidative breakdown as well.

EHC system review and fluid monitoring
Excess fluid flows from improperly set relief valves or high-pressure pumps decrease the available settling time the lubricant has to release air in the reservoir. Low fluid operating levels or fluid return lines that are above the reservoir level will increase air entrainment and the amount of settling time required. The consequence of air release issues or insufficient settling time is micro-dieseling, which literally cooks the oil, causing fluid darkening and increasing overall fluid maintenance requirements.
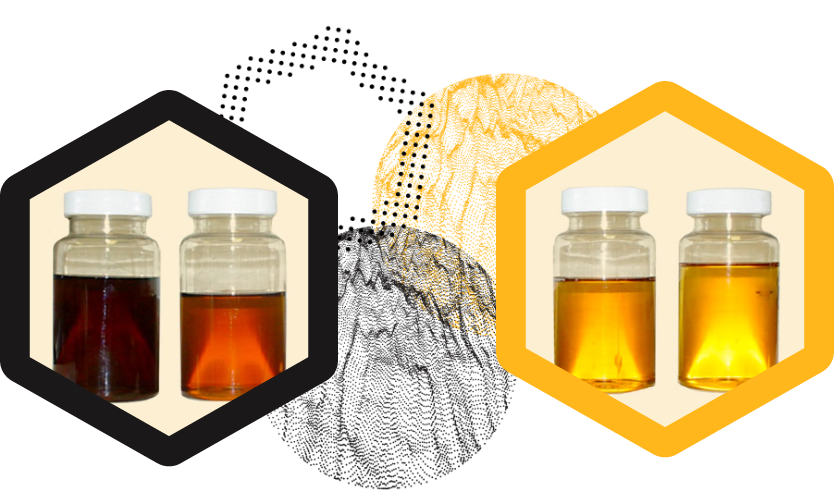
Micro Studies
Economic analysis is provided for a fleet of 100 turbines operating over a 37 year period (Hobbs and Dufresne, 2014).
- Traditional lubricant and fluid maintenance was costing $5 million per year and mechanical failure costs from poor lubricant condition another $13 million per year.
- EPT Clean Oil’s optimized fluid maintenance reduced maintenance costs by over 80% and no further lubricant-related mechanical failures were observed.
- Fluid and maintenance cost savings totaled $97 million for the fleet or on average $1 million per turbine.
- Mechanical and failure cost reductions totaled $243 million or on average $2.4 million per turbine.
- Ongoing ROI is >600% per year versus previous lubricant maintenance spending.
One of the largest power stations in the southeastern United States had to de-rate their 1300 MW steam turbine to 1000 MW because of serious EHC mechanical issues associated with fluid quality.
- Using EPT’s program, which was installed on-line without replacing any mechanical components, the EHC problems were eliminated and the output was increased to 1300 MW within 30 days.
- With the cost per MWh averaging $50/MWh at an average capacity factor of 75%, the lost production and resulting cost savings were an estimated $11 million per month.