Proactively manage fluid chemistry and physical contamination to ASTM D8323 standards
Eliminating Particulate Contamination from Industrial Lubricants 101
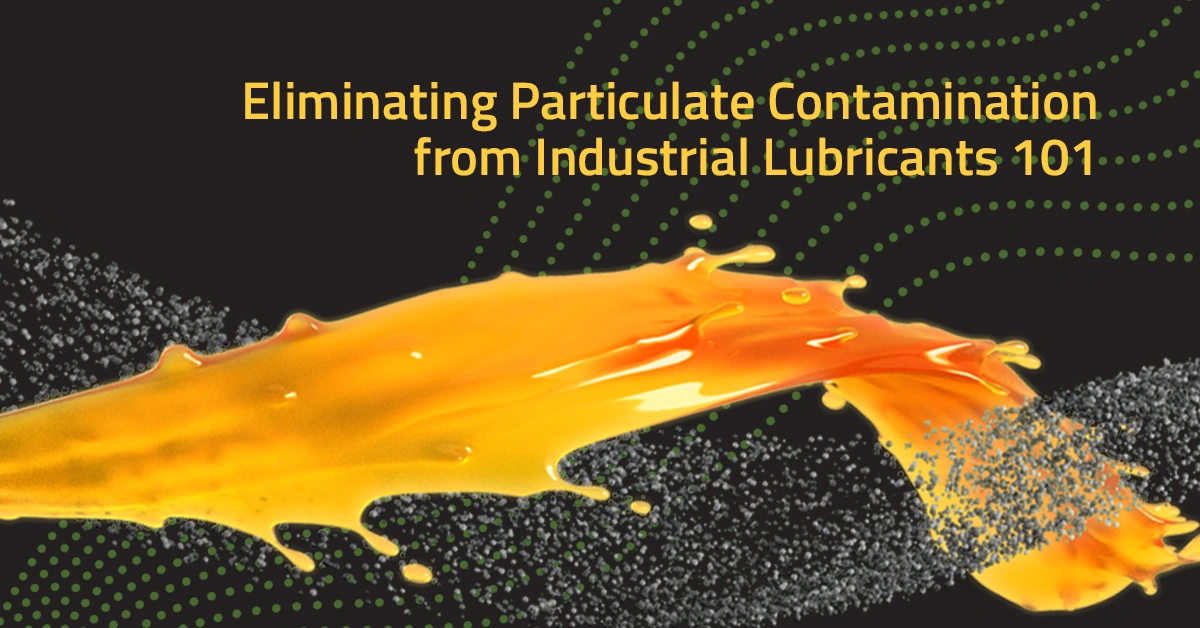
The most common physical contaminant in lubricants is particulate contamination. Significantly impacting lubricant reliability, particulate contamination impairs the ability to lubricate, leading to wear, failure and plugging.
There are two basic categories of particulate contamination: > 4-micron particulate, measured by ISO 4406, and < 4-micron particulate, which is not measured. Within hydraulic lubricants, the limit is 16/14/11, and in lube oils, it is 17/15/12.
Within EHC systems, our investigations have shown that up to 90% of total particulate contamination is below 4 microns and, therefore, not reported in ISO 4406 particle code testing. This particulate contamination also cannot be removed by standard mechanical filters. Fine particulate contaminants pass through these filtration systems, impacting fluid life and component wear.
At EPT Clean Oil, we have designed Lubricant Chemistry Management solutions that target and eliminate particulate contamination, extending the lifecycle of lubricants and mitigating critical asset failures. Our targeted solutions include the following:
ECR is an electrostatic system that combines high-voltage electrostatic fields with a proprietary collector element to remove particles below the range of mechanical filters. Hyper-focused on sub-micron particulate contamination, ECR removes particulates below the range of mechanical filters. The result – improved fluid color and drastically reduced solid contamination levels.
ICB is manufactured with one goal: to remove the dissolved molecules that accumulate and cause mechanical problems in hydraulic systems and lube oil applications. These filters are engineered workhorses based on patented ion exchange technology, combining best-in-class chemistry and materials with precision robotic welding to provide the most robust filter available.
ICB is chemically engineered to remove a wide range of contamination, including acid, varnish, and metals. In EHC systems, ICB filters remove the contamination responsible for servo valve sticking, restoring fluid resistivity. ICB filters offer a step-change in performance, protecting system reliability and production with many benefits beyond acid removal.
Can all particulate contamination be removed with a mechanical filter?
No. Standard mechanical filters cannot remove over 90% of total solid contamination in industrial lubricants. Fine particulate contaminants can easily pass through, impacting fluid life and component wear.
What are the two main categories of particulate contamination in phosphate ester fluids?
> 4-micron particulate measured and classified by ISO 11500/4406 and < 4-micron particulate, which is not measured.
When cleaning or restoring EHC fluid, why is it important to remove insoluble particulate contamination?
Removing insoluble particulate contamination in EHC fluid via ECR® technology helps not only to reduce patch weight but also increases the fluid’s resistivity value.
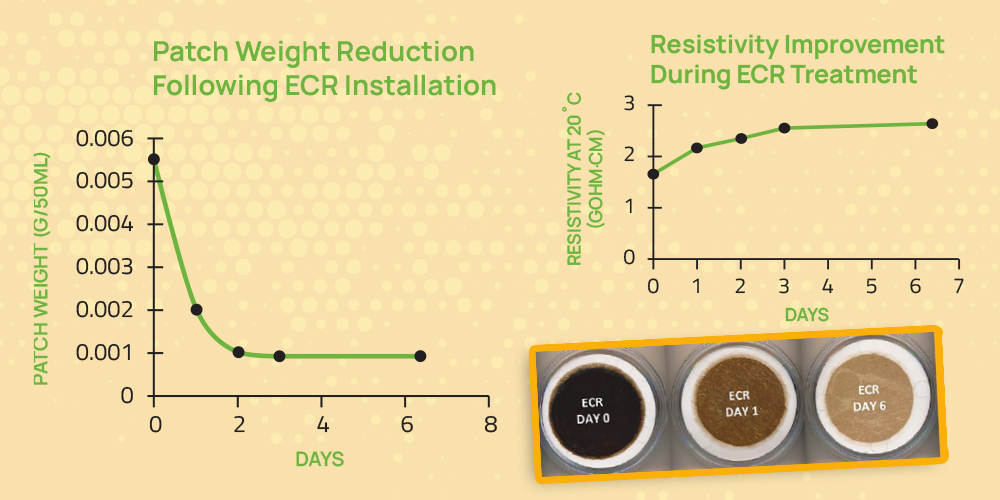
How can I reduce contaminant particles below the range of mechanical filters?
Standard mechanical filters cannot remove most of the total solid contamination. These ultra-fine particulate contaminants pass through these filtration systems, impacting the life of the fluid and increasing component wear. ECR® Particulate Removal is an electrostatic system that combines high-voltage electrostatic fields with a proprietary collector element to remove particles below the range of mechanical filters.
What is the standard guide for the management of in-service Phosphate Ester-based Fluids for Steam Turbine Electro-Hydraulic Control (EHC) Systems?
ASTM D8323 outlines the requirements for monitoring the performance of in-service fire-resistant fluids based on triaryl phosphate esters to accomplish safe and reliable turbine electro-hydraulic control systems operation. ECR® 10000 is the only integrated system to condition EHC fluids to the requirements outlined in this guide.
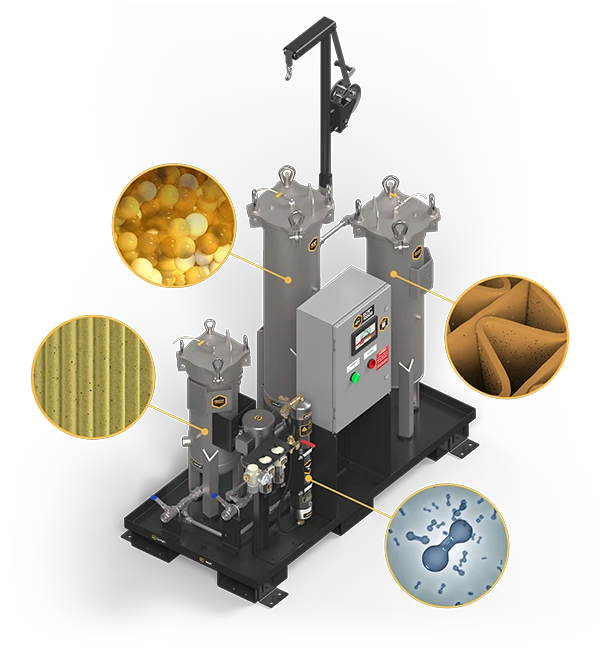
How does the ECR® 10000 remove ultra-fine solids AND dissolved contaminants from phosphate esters?
Solid contamination is removed with electrostatic collector elements, engineered to remove sub-micron particles that are too fine to be captured with normal filters. The ECR collector media removes hard and soft contaminants as small as 0.01 microns through electrophoretic and dielectrophoretic processes. Dissolved contamination is addressed with patented ICB® ion-exchange filters, engineered to remove acids and soluble varnish at the molecular level. Other acid scavengers cannot remove phosphate ester varnish and its precursors.
How does the ECR® 10000 stack up against competing systems?
The ECR 10000 not only significantly reduces varnish potential (MPC), but also solid contamination (patch weight), improves fluid colour, and is best-in-class in terms of performance for acid number and fluid resistivity improvement. Meet ECR® 10000, an integrated skid-mounted kidney loop filtration system designed for phosphate ester fluid, primarily electro-hydraulic control (EHC) applications, equipped with three proprietary filtration technologies to achieve fluid standards as defined in ASTM D8323-21. The ECR 10000 includes 4 integrated filtration technologies, including electrostatics, our patented ICB® ion exchange, high-efficiency particulate removal and TMR® N2 for water ingression management.