Patented ICB® Ion-Exchange Filters
The Impact of Varnish on Bearings 101
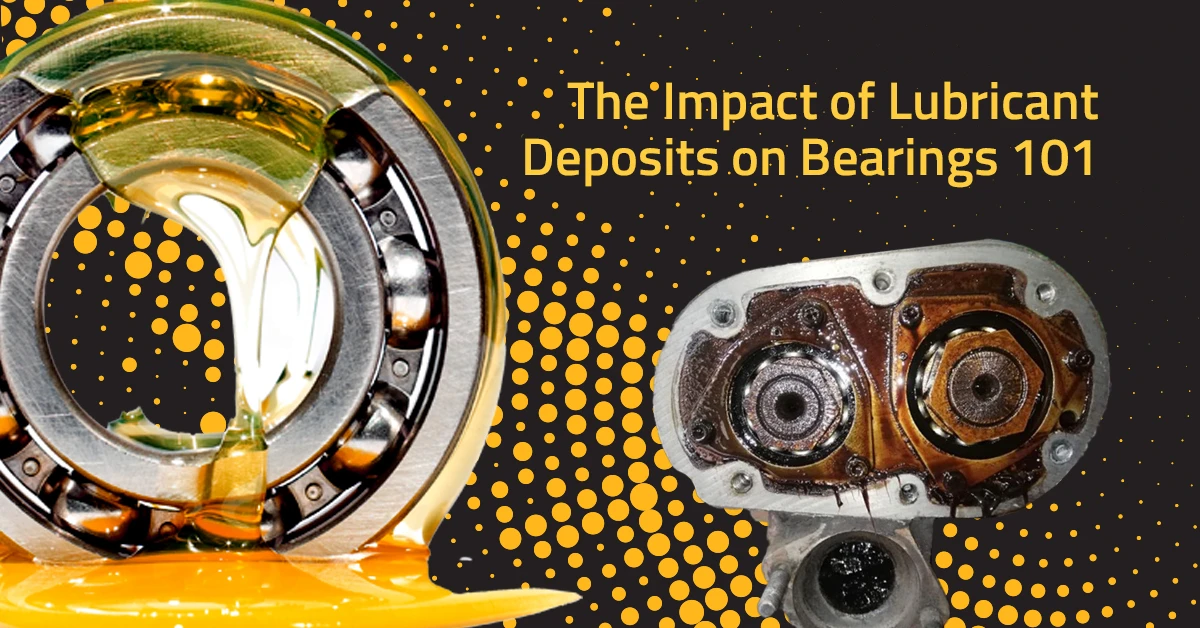
The role of bearings in turbomachinery is critical as it supports the entire shaft load in various types of turbines. Proper bearing lubrication is vital to the operational integrity of a turbine, helping reduce trips and costly downtime. Stoppages and breakdowns will occur without adequate lubrication due to degradation and varnish.
There are three different types of bearings in turbomachinery:
Journal Bearings (Hydrodynamic)
This type of bearing’s function is to support the weight of the turbine’s rotors. A journal bearing comprises two half-cylinders that enclose the shaft and are internally lined with a Babbitt, or a metal alloy, usually consisting of tin, copper, and antimony.

Thrust Bearings (Hydrodynamic)
The function of thrust bearings is to locate the turbine’s rotors axially. This type of bearing is made up of a series of Babbitt-lined pads that run against a locating disk attached to the turbine rotor.
Rolling Bearings
Rolling bearings are mechanical components that support rotating machinery by reducing friction and enabling smooth and efficient motion.
They consist of an outer ring, an inner ring, rolling elements (such as balls or rollers), and a cage to hold the rolling elements in place.
By reducing friction between the rotating parts of a machine, rolling bearings help to improve efficiency, reduce wear-and-tear, and increase the lifespan of the machinery.
What is the Role of Lubrication in Bearings?
In a stopped position, there is metal-to-metal contact, and no oil film layer is present. When the journal starts to rotate, it will climb up the bearing and onto a thin layer of oil, reducing friction and allowing the journal to slide. An increase in rotational speed draws oil into the wedge-shaped clearance space, creating fluid pressure between the journal and the bearing.
At full speed, the oil wedge exists under the journal bearing, with a minimum film thickness on one side called hydrodynamic lubrication. Lubricant film thickness in hydrodynamic lubrication ranges between 10 and 100 microns.
In some turbo machinery applications rolling bearings are used as well, whose function is the same as journal bearings, but their lubrication regime is called elastohydrodynamic.
In elastohydrodynamic lubrication, a lubricant film is formed. At the same time, load transfer between rolling elements and raceways – an elastic deformation- happens with much higher pressures than journal bearings.
As a result, the lubricant film thickness is much smaller than with journal bearings, with a size of half a micron. Any deposit will reduce running clearance and increase bearing temperature and vibrations.
How is Lubricant Film Affected by Varnish Generated by the Lubricant?
Shown in the image below, you see a synthesis gas compressor journal bearing removed due to varnish that had formed on the bearing surface and a compressor used in a petrochemical company with rolling bearings. The varnish deposits caused extreme heat and mechanical vibrations, resulting in premature bearing failure.
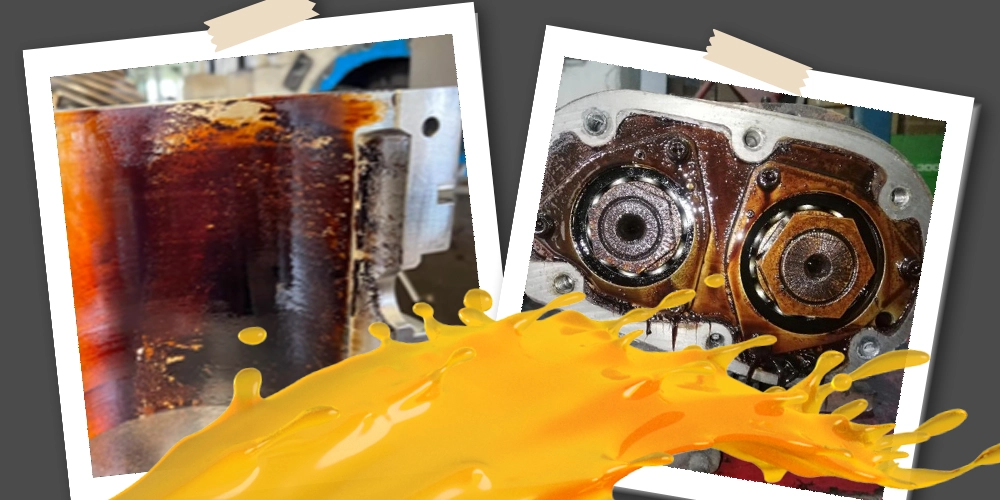
Can Bearings Have Increased Vibrations and Temperature Peaks due to Oil Deposits and Varnish?
In the case of the GE Frame 9 case pictured below, the bearing showed very abnormal vibration peaks and temperature increases, causing a stop in production even though the full-time filtration unit was working. The varnish-induced vibrations and hot spots seem to be appearing and then disappearing.
Since varnish can change its form (soluble or insoluble) when exposed to changes in temperature, pressure, and flow, it can either be deposited on the surface or dissolved back into the oil if it becomes oversaturated.
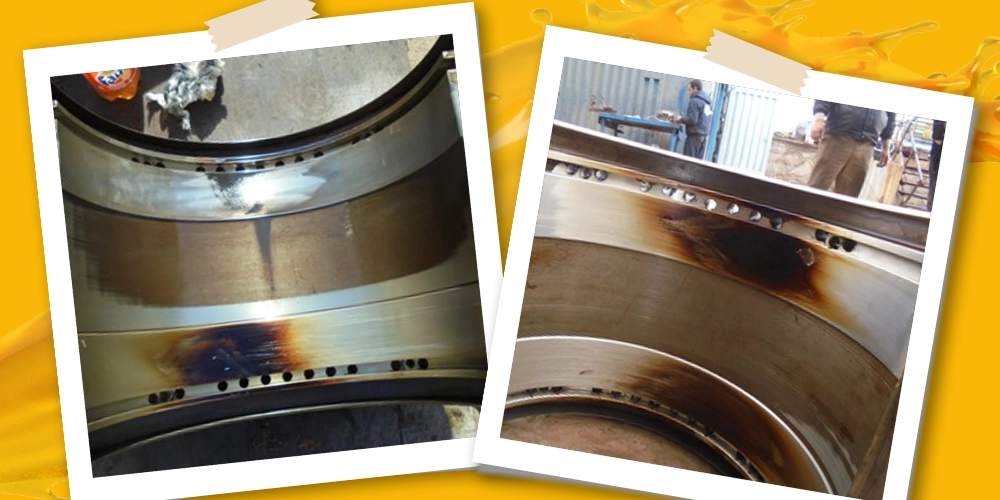
How Can Lubricant Chemistry Management Help to Avoid Premature Bearing Failures?
So how do we ensure varnish deposits never form on bearings? Lubricant Chemistry Management. The best way to remove varnish is to use the lubricant that created it. Since varnish formation is caused when a lubricant becomes saturated with dissolved break-down products, the reaction can be reversed by desaturating the lubricant.
EPT Clean Oil ICB® ion-exchange filters have been engineered to carefully remove dissolved and insoluble breakdown products, returning the lubricant to an unsaturated condition. The lubricant will be in a state of disequilibrium, forcing any solid varnish deposits to be dissolved back into the lubricant, which ICB ion-exchange filters will then remove. This process repeats in a positive feedback loop until all deposits are removed.
The desaturation occurs very quickly, upsetting the equilibrium and removing varnish immediately. This will ensure that bearing vibration and temperature peaks due to deposits never happen again as long as you properly manage your critical assets’ chemistry.
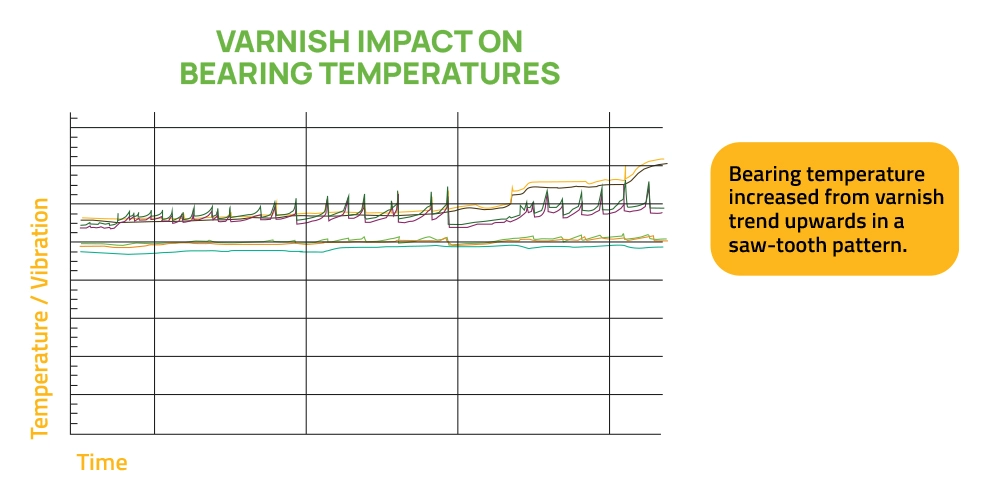
MPC varnish potential may even increase as the lubricant removes the varnish deposits. During this period, monthly filter replacement is recommended to keep the lubricant in an unsaturated state so that it is actively removing deposits. While all systems differ regarding contamination level and varnish deposits, our standardized process is three months operating time, with three sets of filter changes.
The chemistry behind varnish formation and removal has implications for oil changes and flushes. Before a lubricant with high MPC is replaced, an SVR® lubricant conditioning skid backed by ICB ion-exchange filters can be used to clean the mechanical system.
The Impact of Varnish on Bearings 101 Conclusion
By using the correct filtration technology, like the SVR® Oil Varnish Removal System paired with ICB® Ion-Exchange Filters, we avoid flushing in most situations by removing varnish deposits from surfaces. Desaturating the oil with the right Lubricant Chemistry Management solution protects the new oil charge, preventing any immediate additive loss when the new oil is added, with deposits on bearings never forming again.