You can’t manage what you’re blind to
Aeroderivative Turbine Oil Maintenance 101
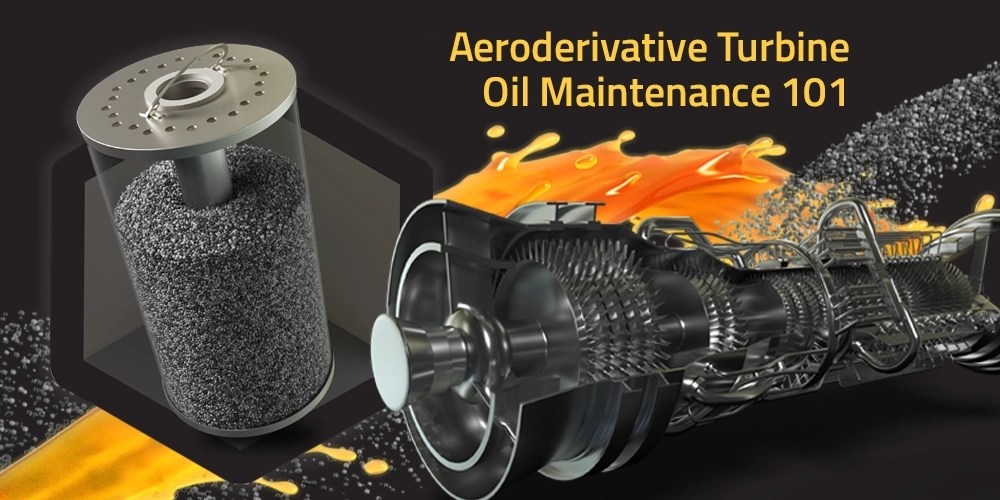
Jet lube applications exclusively utilize aeroderivative turbine oil, formulated using high-quality polyol ester base stocks. This oil is preferred due to its exceptional oxidative stability and unique viscosity requirements.
Upon deployment, aeroderivative turbine oil’s begin to degrade from the very first day, primarily due to oxidation and hydrolysis. These processes generate dissolved degradation products due to high temperatures, water content, and entrained oxygen. Once the lubricant becomes saturated with these dissolved breakdown products, it forms varnish and coking deposits.
Coking and varnishing pose challenges for aeroderivative turbines, leading to production losses and mechanical overhauls. Coke, initially a dissolved oil oxidation by-product, solidifies and deposits on metal surfaces. Conventional approaches fail to address the root cause.
To combat these issues, SVR® backed by patented ion-exchange ICB® JET, offers a continuous solution by removing acids, varnish, oil-coking precursors, and dissolved contaminants. By breaking the accumulation cycle and addressing the root cause of deposit formation and equipment failure, SVR and ICB JET prevent the harmful effects of oxidation products. SVR and ICB JET reduce acid number and varnish potential, ensuring jet lubes are not condemned due to normal breakdown.
By combining SVR and ICB with oxygen and water elimination utilizing our TMR® N2 water removal system, our Lubricant Chemistry Management solutions offer a significant advancement in jet lube maintenance. It enables aeroderivative turbine users to maintain polyol ester lubricants in optimal operating conditions, free from oil breakdown products.
What is an industrial aeroderivative turbine?
Industrial aeroderivative turbines are based on aircraft engines and are generally smaller and a lighter weight variation of heavy-duty industrial gas turbines.
What are the advantages of industrial aeroderivative turbines?
Industrial aeroderivative turbines are more efficient (ie: they produce more power per unit of fuel consumed), and they respond faster than their heavy-duty industrial analogs. This makes them well-suited to support renewables in a peaking capacity.
What are aeroderivative turbine oil‘s?
Aeroderivative turbine oil’s are a polyol ester-based fluid developed to operate at higher temperatures in aeroderivative gas turbine engines.
Why are aeroderivative turbine oil‘s condemned?
Aeroderivative turbine oil’s are condemned due to chemical breakdown as determined by evaluating their acid numbers and remaining antioxidant additive levels.
What are the condemning limits of aeroderivative turbine oil‘s?
The most common condemning limit for aeroderivative turbine oil’s is AN ≥ 2.0 mg KOH/g but some fluid suppliers recommend condemning the oils when they exceed the AN ≥ 0.33 – 0.43 mg KOH/g range.
What byproducts are produced when an aeroderivative turbine oil breaks down?
Like other ester-based lubricants, acids are the most common oil breakdown products produced when aeroderivative turbine oil’s are degraded. These acids are; however, varnish precursors, and they can produce insoluble varnish and coke deposits that deleteriously impact GT performance and reliability.
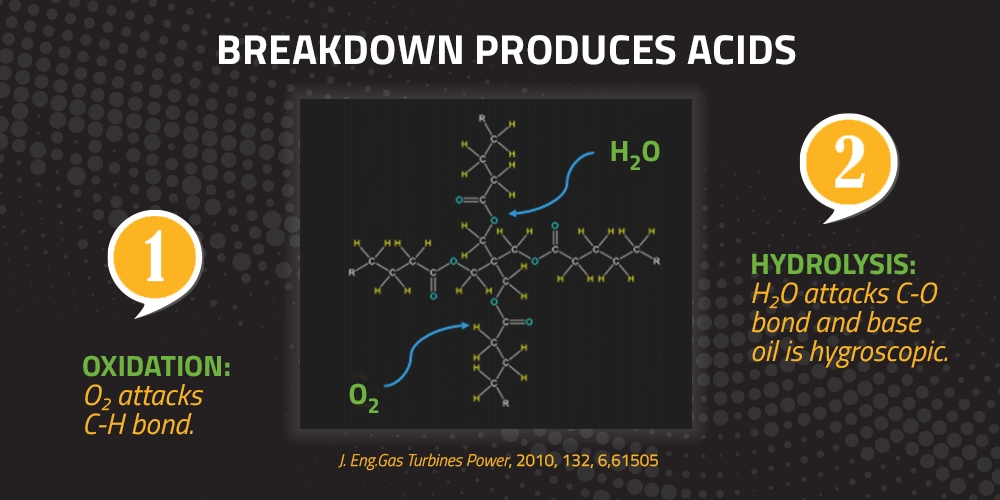
Is the current approach to aeroderivative turbine oil maintenance outdated?
Yes. Most current aeroderivative turbine oil maintenance programs focus on particle filtration, which is not the basis for condemning these fluids. Typical aeroderivative turbine oil analysis testing also misses key tests and doesn’t properly measure the most common cause of failures in this application. Finally, most jet lube maintenance programs do not consider sustainability and treat the oil like a consumable which is used for a short period and then disposed of.
What is the impact of high acid levels on aeroderivative turbine oil’s?
High acid numbers correlate with varnish potentials and an oil’s propensity to coke. Coking is a common failure mechanism that impacts aeroderivative turbines, leading to production losses and often requiring costly repairs. Existing oil analysis and maintenance programs do not address this contamination leading to poor equipment reliability and shortened oil lifetimes.
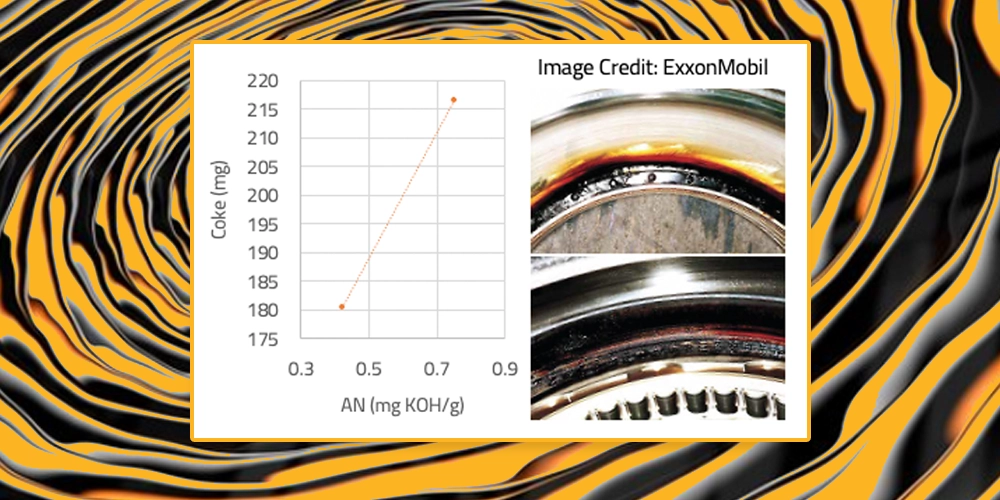
What are the right tests to run for your aeroderivative turbine oil’s?
Oil analysis is a key part of maintenance programs, and its value depends on the right tests being run and then understanding and acting on the obtained results. Many users outsource testing, and generic test packages often miss the mark regarding the specific testing required for aeroderivative turbine oil’s. Notably, most jet lube users do not monitor their fluid’s MPC varnish potential, which provides a valuable indication of oil breakdown and coking propensity.
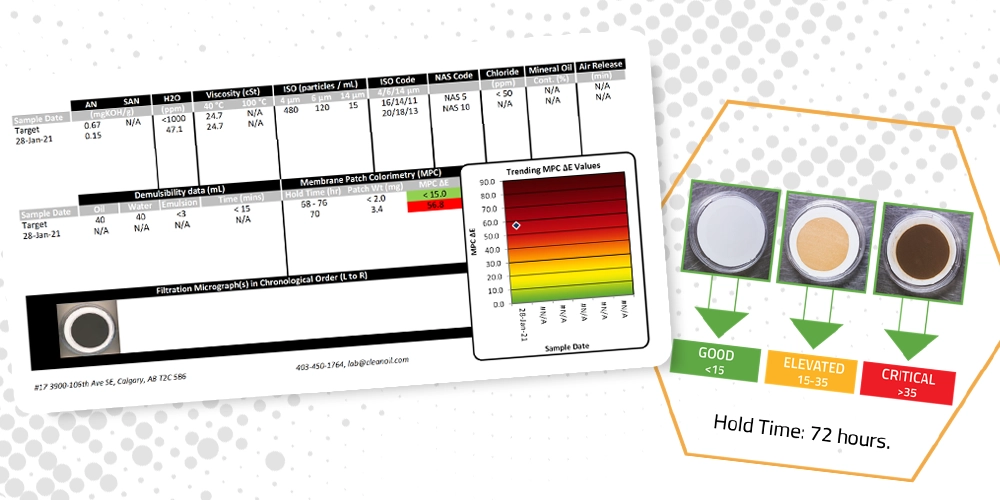
How can I prevent failure and extend the life of my aeroderivative turbine oil?
Installing an EPT Clean Oil™ SVR JET conditioning skid protects your aeroderiviative turbine with a bulletproof vest. Engineered to remove acids, varnish, coking precursors, particulate and water, SVR JET uses patented ICB® ion-exchange technology so that jet lubes no longer must be condemned and replaced. SVR JET combines ICB ion-exchange with our TMR® N2 Water Removal System, eliminating atmospheric water ingression, dissolved oxygen is removed and surface contact with oxygen in the lube oil tank is prevented, mitigating the risk of oxidation.