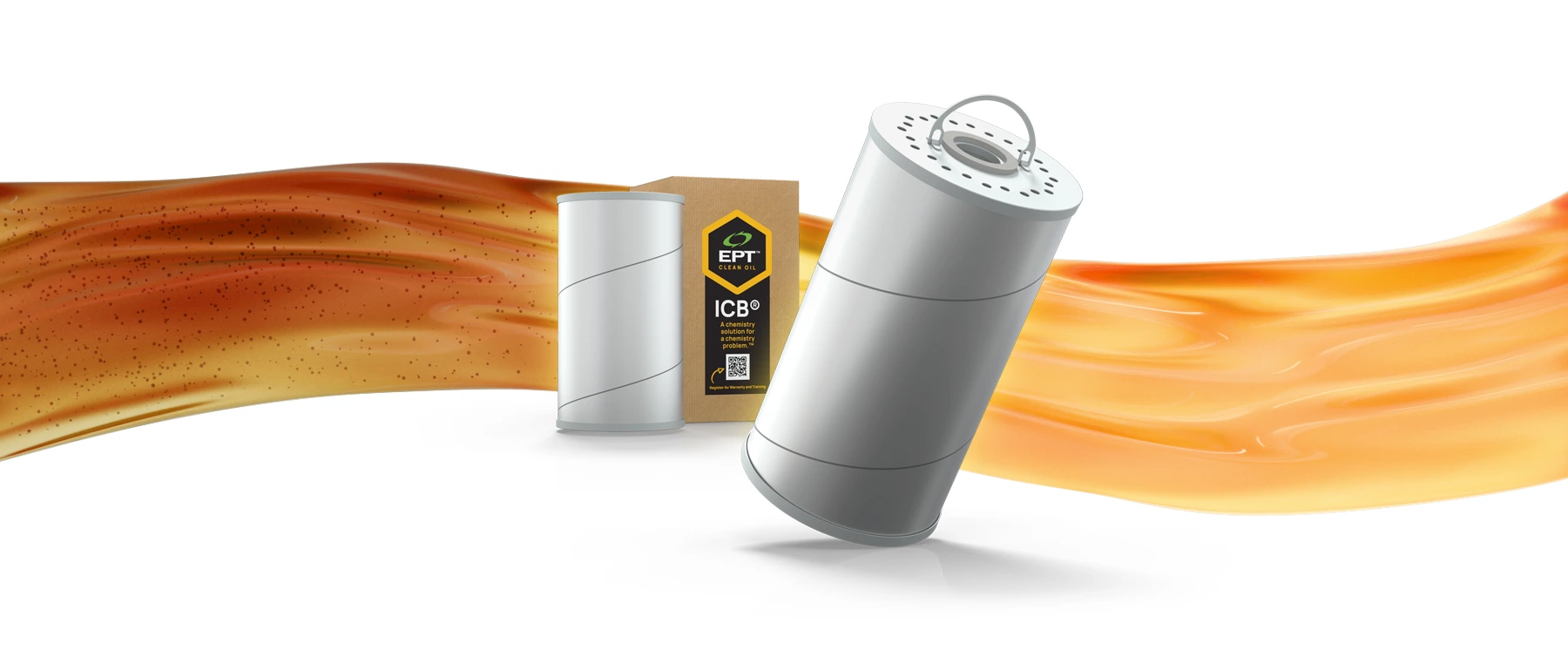
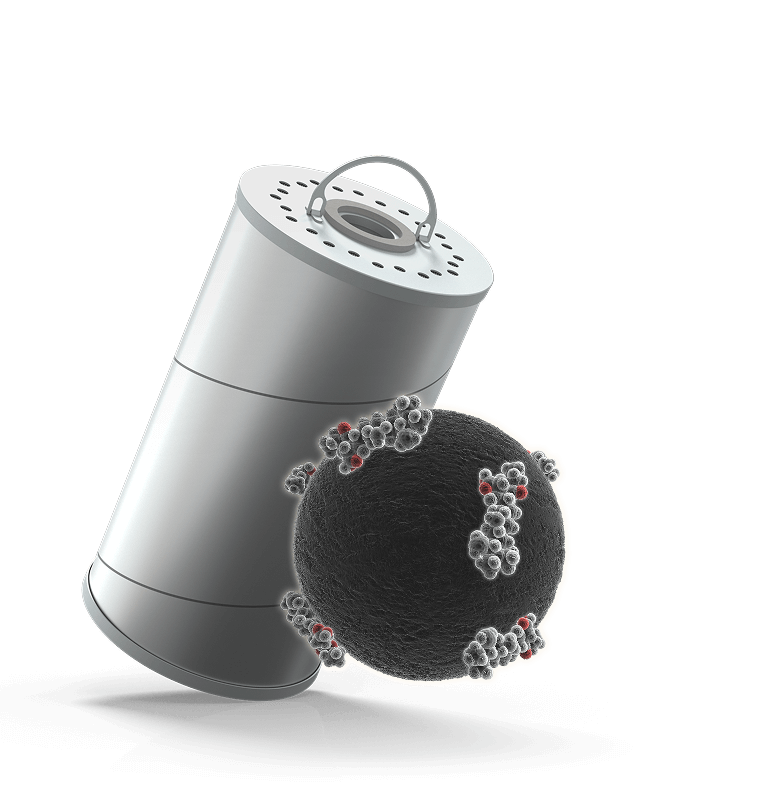
Protect your critical asset with ICB JET for Aeroderivative Turbine Oil
Aeroderivative turbine oil, made from high-quality polyol ester base stocks, is used exclusively in jet lube applications because of its high oxidative stability and unique viscosity requirements. From the first day jet lubes are put into service, they begin to break down due to oxidation and hydrolysis, creating dissolved degradation products. These dissolved contaminants are produced from high temperatures, water content and entrained oxygen. Once the lubricant becomes saturated with these dissolved breakdown products, varnish and coking deposits form.
ICB® JET, patented ion-exchange technology, continuously removes acids, varnish, oil-coking precursors, and dissolved contaminants. Rather than wait for these oxidation products to cause harm, ICB JET breaks the accumulation cycle and eliminates the root cause of deposit formation and equipment failure.
Protect your aeroderivative turbine application with a bulletproof vest.
Meet ICB® Ion-Exchange Filter
WatchICB JET Features and Benefits
- Removes acids and the varnish they produce
- Protects hydraulic variable geometric control systems from sticking
- Resolves known issues when speed changes occur
- Prevents deposits in oil supply lines which otherwise cause supply restrictions, starvation and bearing damage
- Protects against compressor surges and catastrophic engine failure
- Prevents fail-to-start symptoms, protecting production streams
- Manages fluid chemistry and additive consumption levels, extending fluid life, reducing consumption costs and environmental impacts
- Creates a trouble-free operating environment with predictable outcomes and costs
CASE STUDY
This case explores how advanced solutions with the SVR and ICB JET Filters helped reduce MPC varnish potential by 97% maintaining its acid number within the applications required range.
CASE STUDY
This case highlights how the implementation of SVR and ICB JET Filters improved MPC Varnish potential by 78% and 90%, respectively, eliminating oil breakdown problems.
ICB JET
Safe, reliable and cost-effective chemistry solution for in-service aeroderivative turbine oil focused on the root cause of degradation: varnish and coke deposits.
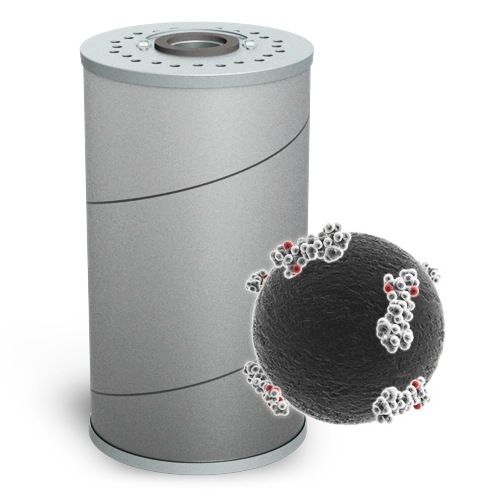
Our Fluid Technical Center is Your Answer Center
EPT Clean Oil’s Fluid Technical Center is a state-of-the-art lubricant research facility, offering specialized analysis and comprehensive evaluations. We take the routine out of oil analysis, providing a complete picture of your aeroderivative lubricant condition.
From advanced testing to the expert interpretation of results, our team of professional and Ph.D. chemists are here to provide the data you need to make informed decisions about your critical assets. You can expect more when you partner with our Fluid Technical Center.
Our Lube Oil test package, applicable for aeroderivative or jet lubes, includes:
- Acid Number
- MPC Varnish Potential and Patch Weight
- Viscosity (40°C)
- Water
- ISO Particle Count
- Dissolved Metals
- Fluid Color
- Antioxidant Levels
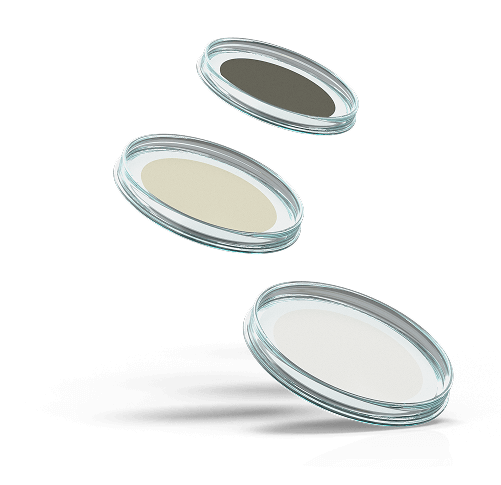
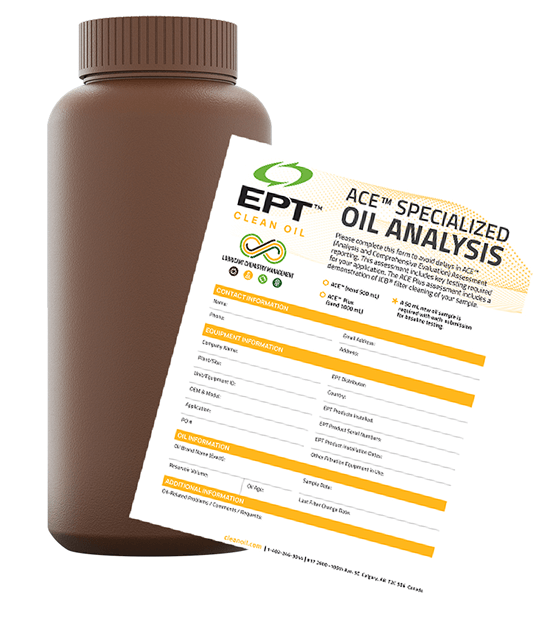
Submit an oil sample today, and let’s get a handle on your aeroderivative turbine oil’s condition.
Meet the Ideal Match for ICB JET
SVR® for Dissolved Contamination Removal
Coking and varnishing are problems that will affect most aeroderivative turbines at some point in their standard service lifetimes, leading to production losses and the need for mechanical overhauls. Coke begins its life as a dissolved oil oxidation product before converting to solid form and depositing on metal surfaces. Most approaches in the marketplace do not address its root cause.
SVR® is a skid-mounted kidney loop lubricant conditioning and water removal system, engineered to include our free-flowing nitrogen blanket system, TMR® N2. SVR eliminates atmospheric water and oxygen ingression, preventing the accumulation of oxidation breakdown material, and eliminating varnish and coke deposit formation pathways. SVR reduces and manages Acid Number and Varnish Potential so that jet lubes no longer be condemned based on normal breakdown.
The combined approach of dissolved contaminant filtration and oxygen/water elimination offers a comprehensive step-change in jet lube maintenance, allowing aeroderivative turbine users to maintain polyol ester lubricants in ideal operating conditions – free of oil breakdown products.
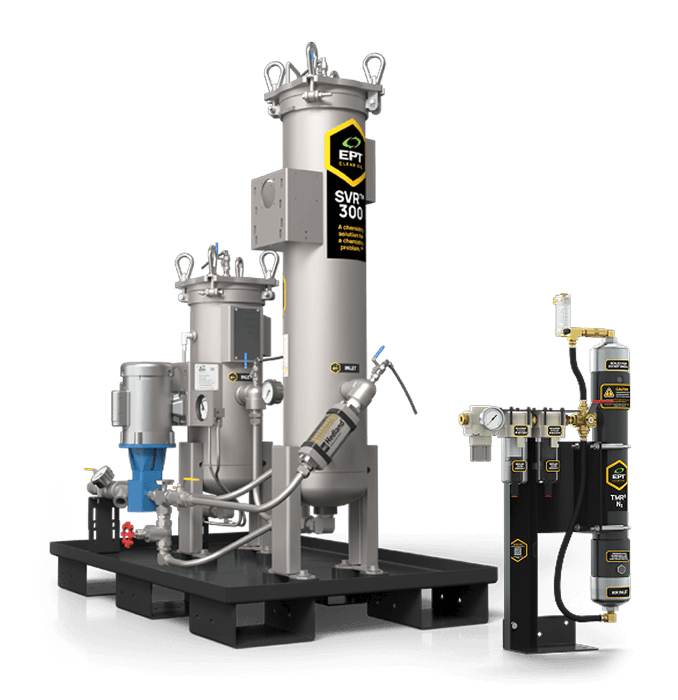
SVR Features and Benefits
- Removes dissolved coking and varnish pre-cursors which are the feedstock from which deposits form
- Protects bearings and other critical components from harmful deposits
- Eliminates the primary ingression pathway for water, thereby promoting the jet lube’s chemical stability and reducing maintenance requirements
- Reduces ISO particle counts crucial for rolling element bearing applications, extending bearing life and the trouble-free operating interval by up to 9x
- Quickly reduces and stabilizes acid number
- Quickly removes and maintains low water levels without consumable elements
- Quickly reduces entrained oxygen and promotes dissolved gas removal
- Nitrogen generator gently eliminates water while also eliminating O2, which is necessary for coke and varnish formation
- Protects oil during standby periods, so water does not accumulate
- Engineer approved system designed to facilitate rapid approval and deployment
- Very low maintenance and time requirements – turn it on and let it run
- No downtime – SVR can be installed without an outage
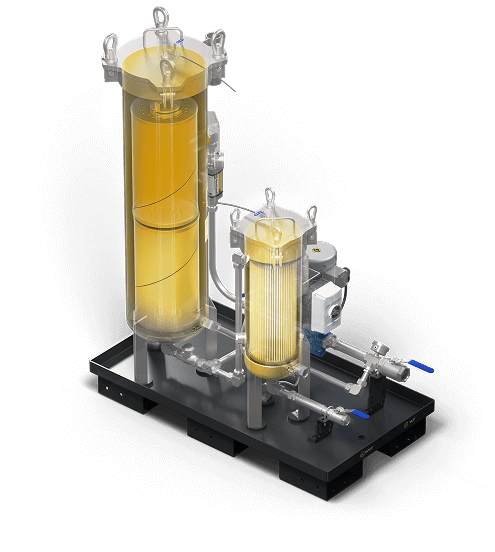