The best way to deal with lubricant varnish, is to never have to.
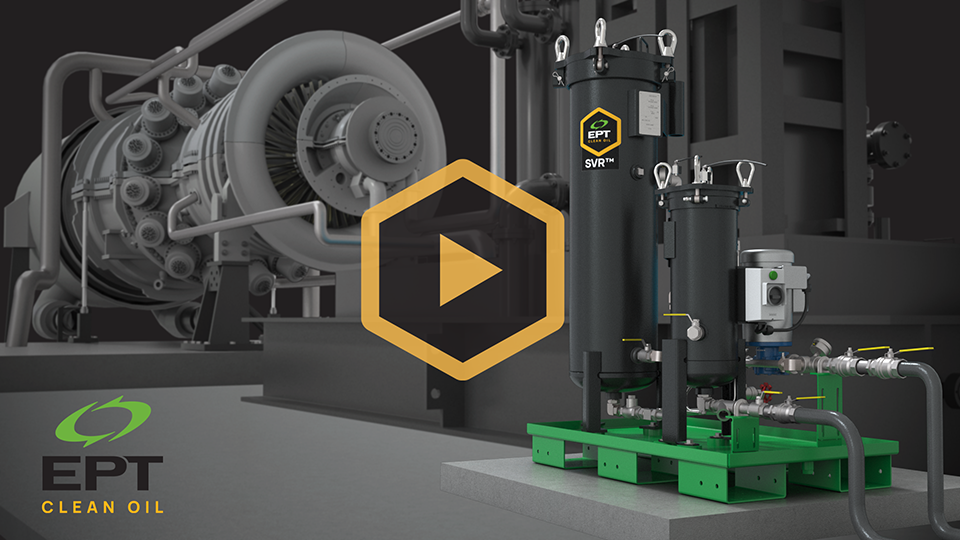
Stop lubricant varnish in its tracks.
From the moment lubricants are put into service, they chemically breakdown. The primary pathway: oxidation.
The result: oxidation waste products dissolve in the oil. This dissolved oxidation material all too often goes unmanaged by routine maintenance.
Modern turbine and compressor oils are non-polar and oxidation material is polar, resulting in a tendency for this oxidation material to be more attracted to metal surfaces than the oil itself. The result: deposits on mechanical surfaces including bearings.
For too long this has been the status quo. It’s time to manage, unmanaged dissolved oxidation material in your lubricant. Meet SVR® – a chemistry solution for a chemistry problem.™ Backed by patented ion exchange technology, ICB®, SVR works 100% of the time, removing acids and dissolved oxidation material as it is generated.
Only by managing oxidation levels and removing oxidation material as it is generated can the root cause of lubricant deposits, or varnish, be eliminated.
SVR® Lubricant Conditioning System
SVR® is an engineered lubricant conditioning system that works 100% of the time, targeting the underlying cause of lubricant failure: chemical breakdown.
Utilizing patented ion-exchange resin technology, ICB®, SVR removes chemical breakdown products and varnish at the molecular level, maintaining optimal lubricant quality. Through full-time, continuous treatment, SVR stops the contamination cycle in its tracks, cleaning the lubricant every time it cycles through the kidney loop circuit. By removing and preventing chemical breakdown material accumulation, lubricant life is extended, mitigating mechanical failures and costly production losses.
As the gold standard in turbine lube oil and phosphate ester fluid maintenance, SVR is designed to facilitate rapid deployment, without downtime. Just install and reap the following rewards:
- Mitigate the risk of servo valve sticking
- Remove bearing deposits
- Restore normal MPC varnish potential and Acid Number (TAN/AN)
- Restore demulsibility values
- Protect against solid and dissolved varnish
- Results qualified by ACE™ oil analysis
- Significantly reduce solid contamination
- Significantly improve fluid resistivity
Transform the way industrial lubricants are used and maintained with the SVR lubricant conditioning system.