Reduce Impact and Save Money by Managing Lubricant Chemistry
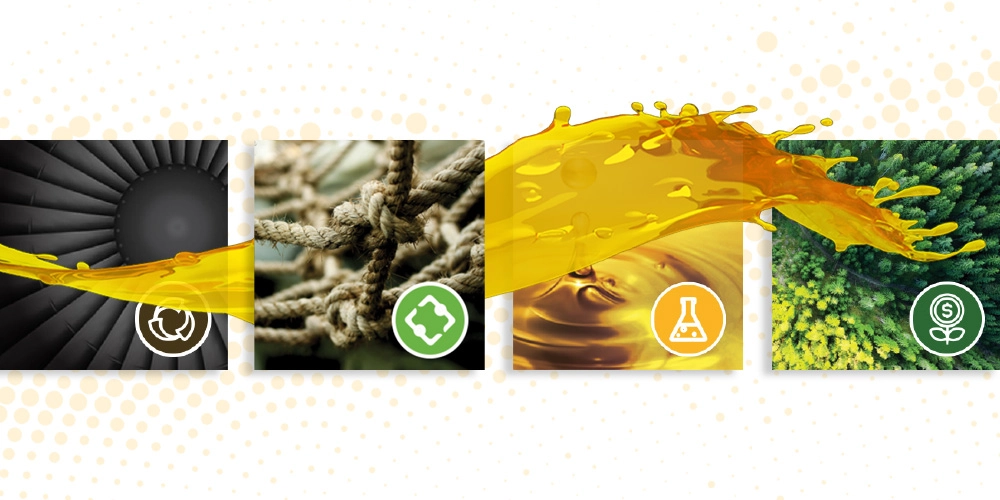
In part one of this four-part series, ‘You Can’t Manage What You’re Blind To’, we learned that lubricants don’t die suddenly; they die after relatively long periods of neglect. Lubricant death is, however, avoidable when the root cause of lubricant failure is considered, and our maintenance practices are adjusted to manage the processes that lead to failures.
In part two, ‘Lubricant Maintenance Program Route Planning‘, we explored how to leverage oil analysis data to prioritize and effectively implement maintenance solutions. Correct MPC testing, understanding remaining lubricant life and, ultimately, implementing an effective Lubricant Analysis program are crucial to staying in-spec, producing results, and establishing priorities for maintenance. So, what’s next?
A Better Way
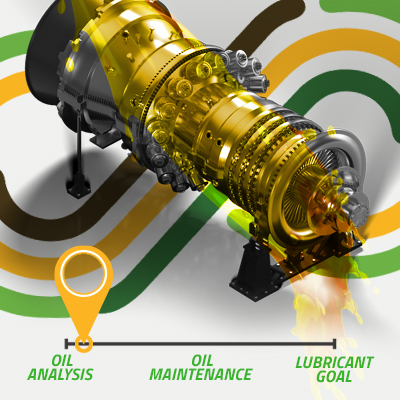
What happens when you use Lubricant Chemistry Management to its full potential? To better understand its impact, let’s take a look at a case study, involving a fleet of 80 turbo-compressors. Since making the decision to use ICB® ion-exchange filters on their equipment decades ago, Lubricant Chemistry Management has led to over $97 million dollars in savings for this operator. While dollars are important, Lubricant Chemistry Management’s more significant return on investment was its environmental impact, as it prevented 15 million kg of carbon emissions since it was implemented.
Current Maintenance Practices
Despite knowing better, many are not managing their oil chemistries or their lifetimes effectively. Worse still, most oil maintenance programs don’t make any consideration for sustainability, which must become an operational tenet going forward.
Business as Usual
Unfortunately, “business as usual” maintenance tends to be reactive, even for some of our most critical assets. For example, we recently met a Frame 7 gas turbine operator who was maintaining their unit reactively, even though the turbine produced all the power and steam required to keep their facility up and running. For this operator, 24-hours of unplanned GT downtime was a typical annual occurrence. “If it ain’t broke, why fix it?” they thought. So, for years they lost (on average) about $370,000 annually and, over the lifetime of their turbine, this amounted to over $9 million in avoidable losses. Why do we say that these losses were avoidable? Because they could easily have been presented with effective Lubricant Chemistry Management.
Lubricant Chemistry Management
So, what do we mean by Lubricant Chemistry Management? Lubricant Chemistry Management is a two-pillar approach; The first pillar is oil analysis. You need to run the right tests, the right way, at the right intervals, and when you get test results, you need to act on them. Oil analysis is your window into your lubricant’s chemistry. If you’re not doing good oil analysis, you may be blind to problems with your fluid’s chemistry.
Get Value From Your Oil Analysis
You can’t manage what you’re blind to, so good oil analysis is an essential part of your maintenance program. Users typically rely on third-party labs with generic test packages, and most of these commercial labs lack expertise when it comes to critical rotating equipment.
Proper oil analysis should answer the important questions:
- Will the oil do its job?
- Could my equipment fail imminently?
- Is my oil chemistry failing?
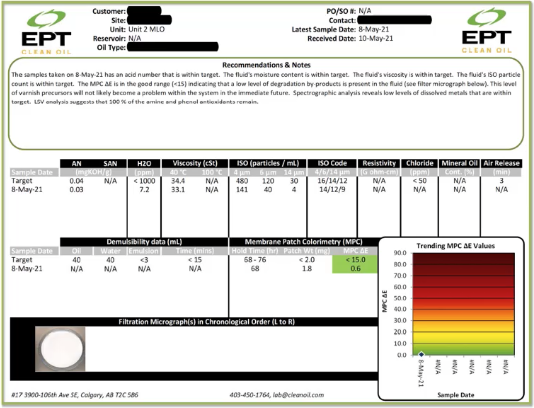
Third-party labs typically address #1 and #2, but often fail to adequately highlight potential issues with oil chemistry. Oil breakdown products such as acids and varnish are the most common cause of lubricant chemistry issues, which leads to equipment downtime and failures.
Knowing your oil’s MPC varnish potential is crucial, and many don’t routinely test for it. Since varnish can form quickly, we highly recommend MPC testing every single time you send in an oil analysis sample and those samples should be taken on an at-least quarterly basis for critical systems.
It’s extremely important that you not only run the right test, but that you run it the right way. Obviously, this includes MPC (membrane path colorimetry) testing, as outlined in ASTM D7843-21. As mentioned in part 2 of this series, your oil analysis program will only prove useful if you can count on the accuracy of the results that it provides. You use these results to make important maintenance decisions, so it’s imperative that you have confidence in them!
Rethink Oil Maintenance
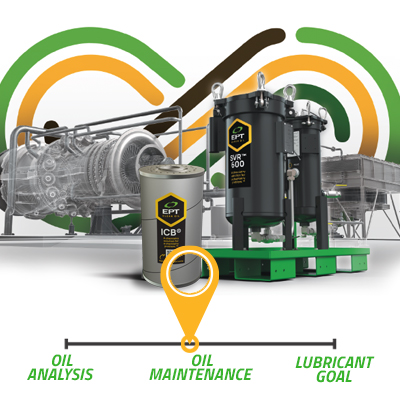
We’ve seen that “business as usual” isn’t enough when it comes to oil maintenance. This is because current maintenance practices tend to focus on reducing particles and water, which are not the basis for the condemning oils. As it turns out, oils are condemned due to chemical breakdown. Keeping your oil clean and dry is important, but you’ll need to manage its chemistry to extend its lifetime and ensure that its helping (and not harming) your system.
This is where the second pillar of Lubricant Chemistry Management comes into play. Now that you’re aware of oil chemistry-related issues, you need to do something about them. The best way to do this is to use ICB® ion-exchange resins. ICB allows you to manage oil chemistry by removing the oil breakdown products that cause reliability issues and lead to oils being condemned.
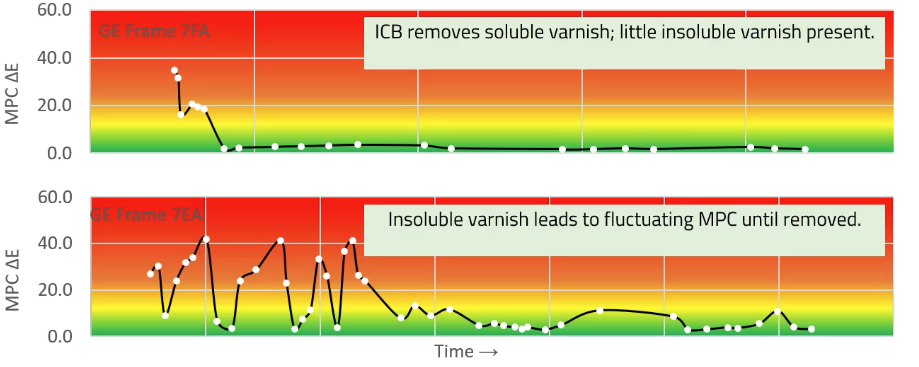
Sustainable Oil Management
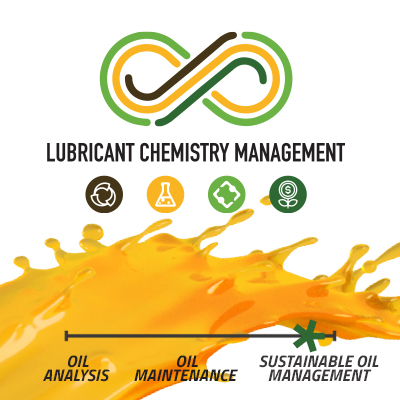
Sustainability is defined as “the ability to be maintained at a steady level without exhausting natural resources or causing severe ecological damage.” As it turns out, lubricant manufacturing is the most carbon-intensive process in an oil refinery. We, therefore, need to be certain that we get all the life that we can out of our lubricants. There’s nothing sustainable about changing your oil needlessly! If we can do better oil maintenance via Lubricant Chemistry Management, we can extend our oils’ lives and, in doing so, reduce our impact.
Cost Comparison: “Business as Usual vs. Lubricant Chemistry Management”
Let’s take a look at the economic and environmental costs associated with poor maintenance on a Frame 7 turbine with a 22,800 L reservoir. Failure to manage lubricant chemistry (aka “business as usual), would see us condemning the oil due to breakdown. Typically, this happens about every 5-years. As a result, the oil would need to be changed at least 5 times over the turbine’s 25-year lifespan; that’s 114,000 liters of oil! Using the chart below, we can calculate the cost and carbon footprint associated with “business as usual.”

With ICB filtration on this same Frame 7 turbine, lubricant chemistry management is possible and we can prevent 4 oil refills, saving 80% of the turbine’s oil-related costs and, more importantly, 80% of the carbon footprint associated with that oil. Even when we factor in the lifetime cost and carbon footprint of ICB conditioning, you can see that Lubricant Chemistry Management provides an economic ROI of 350% and a sustainability ROI of almost 32,000% in reduced emissions!
Restore Reliability While You Address Sustainability!
Last year, 20% of gas turbines lost production due to oil-related problems. If we remove varnish and manage oil chemistry properly, this number drops to near-zero %. Just 24 hours of downtime on a Frame 7 turbine can cost about $164,000. One single loss like this is more costly than a lifetime of ICB ion-exchange filters and conditioning. It’s also worth noting that start-up emissions after a failure are significantly greater than baseload emissions, so we actually reduce our impact when equipment downtime is eliminated completely.
Conclusion
Varnish is the most common cause of oil-related failures and is the end result of not managing your lubricant’s chemistry. Lubricant Chemistry Management provides significant benefits and ROI, economically and environmentally. To manage your lubricant’s chemistry, obtain complete and reliable oil analysis data like our Fluid Technical Center’s ACE™ assessments. Once you’re aware of your oil’s chemistry-related issues, do something about them; rethink your oil maintenance program by using ICB® ion-exchange resins to remove oil breakdown products. By taking these steps to manage your lubricant’s chemistry, you’ll save money, make your own maintenance more predictable and proactive, and reduce your impact by cutting oil-related carbon emissions.