MPC Varnish Potential Testing (ASTM D7843)
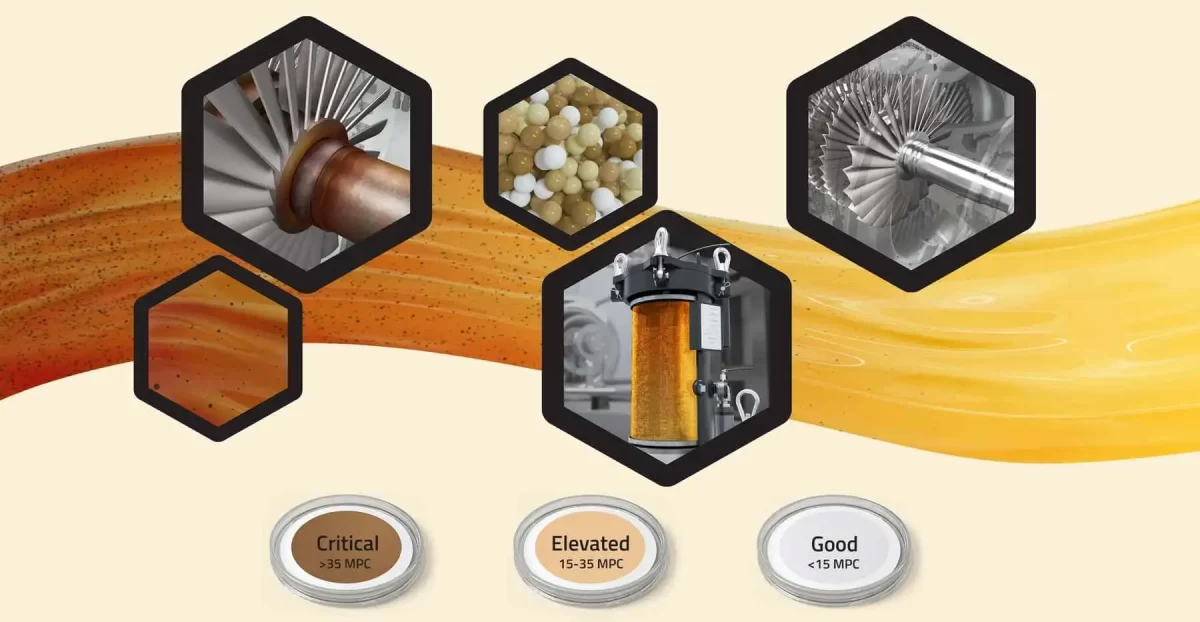
MPC varnish potential testing (ASTM D7843) is an essential analytical test to determine the propensity for a lubricant to form varnish deposits. With the probability of varnish-related failures reported to be as high as 100% (GE TIL 1528-3), monthly MPC testing is recommended for all critical turbine installations. The ASTM approved MPC test is straightforward and can be completed as part of your existing lubricant analysis testing program. It can also be performed on-site using a modified test method for rapid assessment of potential varnish-related problems.
MPC Varnish Potential Testing Overview
There are two main parts to the MPC test: filtration and color measurement. During the first part, 50 mL of the lubricant to be tested is diluted with an equal volume of petroleum ether. This mixture is then filtered through a 0.45 μm nitrocellulose patch which is then rinsed with petroleum ether and dried. The intensity and color of the patch are then measured against a control patch using a spectrophotometer that calculates the color difference, or ΔE value. The ΔE value and the corresponding propensity for the formation of lubricant varnish deposits are then assessed according to an MPC scale.
MPC Scale
EPT Clean Oil’s MPC scale is then used as a guideline to help users assess their lubricant’s potential for varnish formation. There is three levels on the varnish potential scale: Good (∆E<15), Elevated (∆E 15-35) and Critical (∆E>35). The higher the MPC value, the higher the amount of varnish deposits and precursors dissolved in the lubricant and the greater the propensity for the lubricant to form harmful varnish deposits.
Monthly MPC testing is recommended for all critical turbine installations.
Operating Target MPC Value
Ideal lubricant operating condition (from a varnish perspective) is achieved when the MPC ΔE value is <15. When the MPC ΔE value is continually maintained at below this value, the lubricant‘s solvency characteristics are maximized, which prevents varnish deposit formation and forces existing deposits back into their less harmful dissolved form.
MPC values increase as dissolved oil breakdown products (varnish precursors) accumulate. These breakdown products are produced by oxidation and begin to accumulate from the first moment that the lubricant goes into service. Each lubricant has a finite capacity (saturation point) to hold these dissolved oxidation products in solution. Once this point is reached, the lubricant becomes saturated and excess breakdown products are forced from the fluid, forming harmful lubricant varnish deposits.
Once formed, lubricant varnish has a natural attraction for metal surfaces because of the polar nature of both the varnish and the metal. As varnish begins to coat metal surfaces, mechanical clearances are reduced, decreasing equipment performance and, ultimately, leading to failure.
Complicating matters, the saturation point varies with lubricant temperature, pressure and flow. These parameters are dynamic in most mechanical systems. For this reason, varnish is often deposited in sensitive mechanical areas prior to appearing in the oil reservoir. It is, therefore, important to select a varnish prevention program that addresses the issue during normal turbine operation when the varnish precursors are dissolved in the oil.
When MPC values are maintained at ΔE <15, the lubricant contains very few varnish precursors and is not prone to deposit formation. Moreover, the lubricant will have high solvency characteristics under all system operating conditions and will actively remove any existing varnish deposits from metal surfaces.
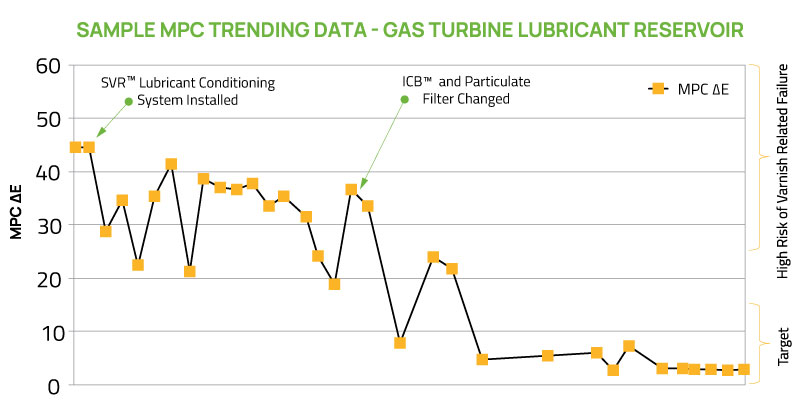
system gas turbine lubricant reservoir installation