ACE™ Oil Analysis
Lubricant Chemistry Management
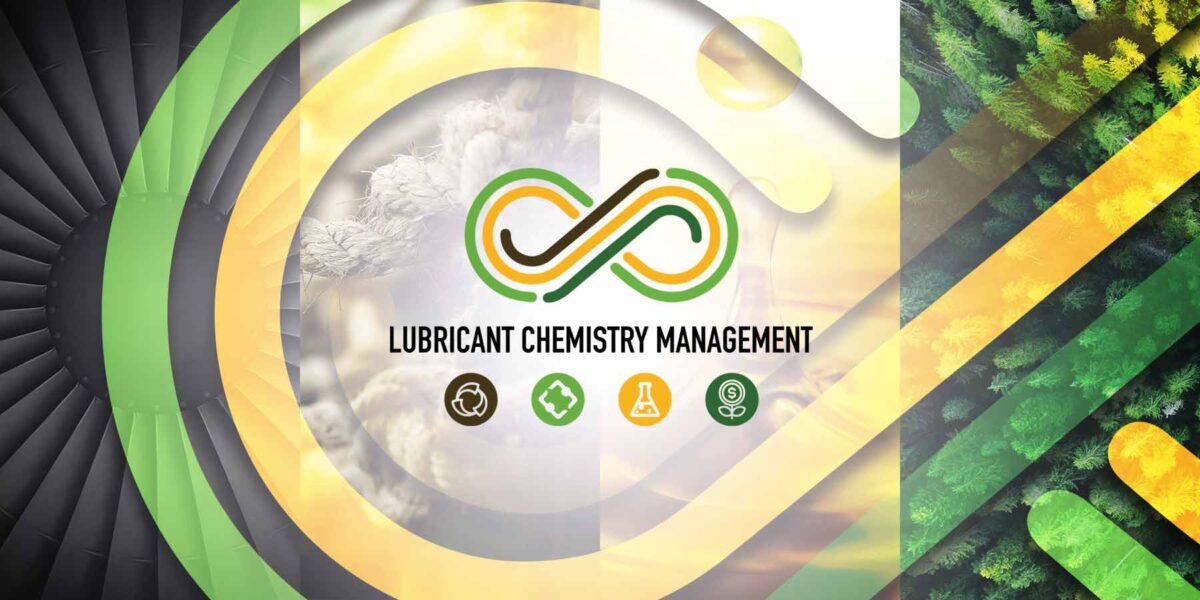
Dating back to the inception of EPT Clean Oil in 1994, Peter Dufresne has hit the ground running focused on one thing: Lubricant Chemistry Management. If you are in a room with him or consulting him via email or phone he will consistently lead with one question, “Is your lubricant chemistry managed or unmanaged?”
Lubricants chemically break down from the first day they are put into service – the primary pathway is oxidation. If lubricant chemistry is not in a fully managed state on critical machines, it’s not a matter of if but when varnish issues will rear their ugly head.
The Future of Turbomachinery and Compressor Lubricant Maintenance
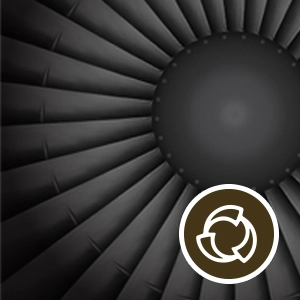
Asset Availability, Predictability and Reliability Are Critical
Uptime and availability are key performance indicators for critical turbomachinery. These critical assets must be available at a moment’s notice 100% of the time. What is missing from this equation is that turbine lubricant maintenance focuses on particulate removal only, leaving chemistry in an unmanaged state.
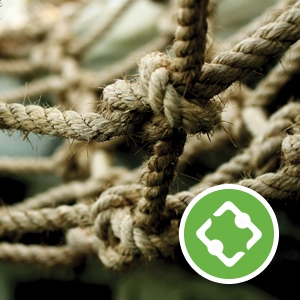
EPT Clean Oil Exists To Eliminate Lubricant-Related Failures
From the first day a lubricant is put into service, it begins to chemically break down, slowly impairing its physical properties and performance. EPT Clean Oil partners with you to address the root cause of lubricant breakdown, applying science and solutions to transform the way industrial lubricants are used and maintained. We call this Lubricant Chemistry Management.
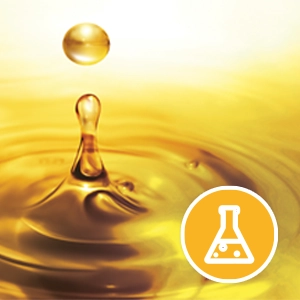
Manage Uptime with Lubricant Chemistry Management
Lubricant Chemistry Management places a protective shield over your critical assets. Going beyond particulate removal, we apply technology that actively eliminates chemical breakdown products including varnish precursors and oxidation materials, managing the chemistry in your system on a permanent basis and eliminating lubricant-related failure.
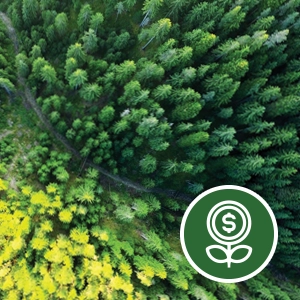
Deliver Unmatched Results and Asset Performance
Lubricant Chemistry Management delivers unmatched economic and environmental returns, mitigating failure costs and lubricant-related carbon emissions. Target the root cause of oil breakdown and failure and take your maintenance program to the next level.
Partner with EPT Clean Oil and change the economic and environmental performance at your plant with Lubricant Chemistry Management.
Submit an oil sample to our Fluid Technical Center, and let us help you get a handle on the condition of your turbine lube oil or control fluid. Our comprehensive ACE™ assessment establishes your fluid condition to ASTM standards, providing key fluid parameters and overall recommendations to reestablish the fluid quality your application demands.
Why is lubricant chemistry management important?
As we move towards net zero in 2050 we have a duty to decrease our environmental footprint. By maintaining oil in its original form as long as possible, we eliminate unnecessary environmental waste and carbon emissions with every litre produced, resulting in 3.5 kg of CO2 emissions. Lubricant Chemistry Management targets the root cause of breakdown and oil failure, eliminating the failure pathways mechanical systems suffer that are lubricant related, extending the lifecycle of the oil in alignment with the asset’s lifecycle.
How do you manage the chemistry of lubricants?
The fundamental breakdown pathway of a lubricant is oxidation, and the life of a lubricant is based on the number of antioxidants remaining. Patented ion-exchange ICB® filters were engineered in 1994 to address chemical breakdown, targeting the root cause of lubricant contamination at the molecular level, and addressing the factors that cause oxidation. It’s not enough to remove dirt and water; we need to remove oil breakdown products as they form through lubricant chemistry management.
Why is it important to have a permanent lubricant maintenance system in place?
Oil begins breaking down from the first day it’s put into service. It is much easier to maintain lubricant quality with a dialysis-style system that prevents varnish, extends the life of additives, and corrects demulsibility than it is to recover one that is in poor condition. Permanent installs are crucial as rotating equipment causes a step-change in the rate of lubricant breakdown when it is removed from the critical asset.
What is it about the partnership between SVR® and ICB® that creates a chemistry solution to a chemistry problem?
The SVR® Lubricant Conditioning System backed by patented ion-exchange ICB® filters goes beyond physical filtration, adding chemistry management to your maintenance program. With the root cause of oil failure being oxidation, and with most mechanical issues also related to oxidation, SVR and ICB will maintain the chemistry to remove both failure pathways. SVR and ICB will manage the amount of breakdown and remove breakdown products so they do not further damage the oil or the equipment.