Meet the Graduating Class of 2024!
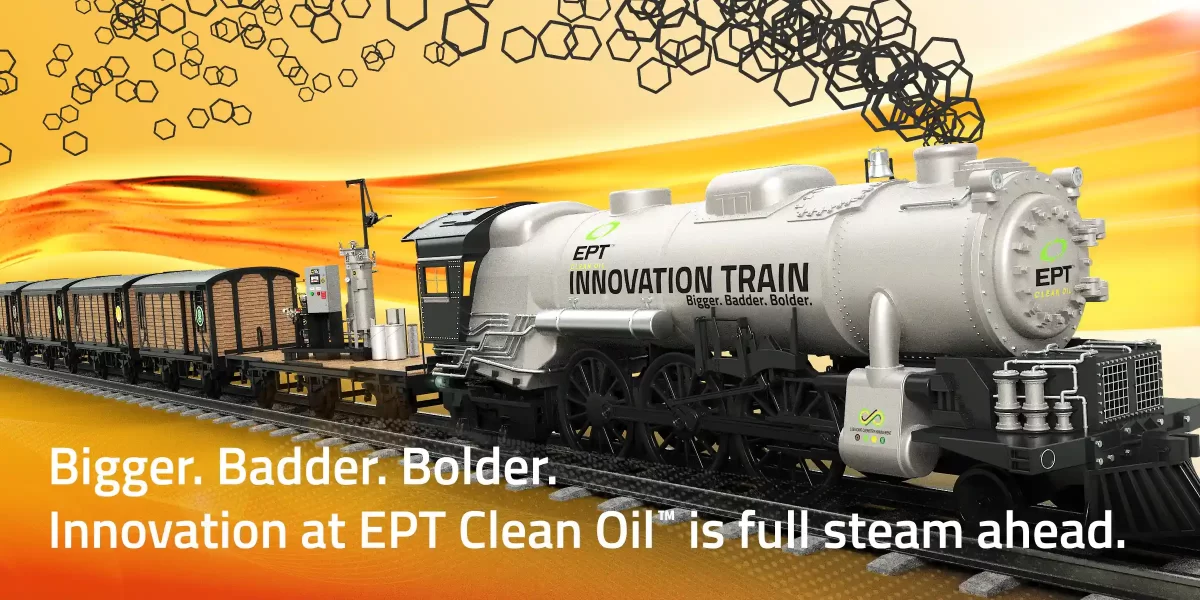
June is an exciting time of year, with change in the air. Spring showers have given way to sunny, summer skies. Gardens are abloom and BBQs aflame. Last but not least, the academic year is ending, and our best and brightest are donning caps and gowns to celebrate moving on to bigger and better things. It’s only appropriate then that we, at EPT Clean Oil, watch with pride as our most recent innovations and advancements prepare to graduate from the school of Lubricant Chemistry Management!
It’s Time to Move On from Phosphate Ester Contamination Problems
Phosphate ester hydraulic fluids are commonly used in power plants, aviation, and other applications where fire resistance is critical. While best practices for phosphate ester maintenance are well-established in ASTM D8323, many turbine and electro-hydraulic control (EHC) system users experience fluid-related problems and failures, which cost hundreds of millions of dollars each year and generate headaches and waste instead of power.
To avoid this, phosphate ester contaminant-removal is crucial. Effective contaminant-removal also allows users to maintain the performance and reliability of their critical systems, extend the lifetime of their fluids, and reduce their impact. Like many journeys, the first step can be the most important one and the first step to effective phosphate ester maintenance involves addressing solid/insoluble contamination using advanced filtration technologies.
Solids Contamination in Phosphate Ester Fluids
In phosphate esters, solid contaminants can be lumped into one of two categories:
- Particles ≥ 4 microns.
- Insolubles < 4 microns and ultrafine (sub-micron) solids.
Most phosphate ester maintenance focuses on the larger particles from category 1. Indeed, these are routinely measured by ISO 4406 particle counts and are targeted by conventional EHC system filters. Every phosphate ester user should be aware of these contaminants, their impact, and they should know how to remove them.
What’s less well-known, is the prevalence and impact of smaller solid contaminants. In fact, many phosphate ester users are all-together blind to the existence of these erosive solids since the industry’s most common particle count test (ISO 4406) only detects insolubles that are ≥ 4 microns. To detect smaller insolubles, MPC and patch weight testing are extremely useful, but rarely applied (despite being required regularly by ASTM D8323). Shockingly, studies have shown that up to 90% of the total insoluble material in an EHC system can be <4 microns in size. Imagine being blind to 90% of the contamination in a critical control system? Sadly, many phosphate ester users are!
What’s worse than being blind to insoluble contamination? Being unable to do anything about it! Conventional filters only remove particles ≥ 3 microns. Even specialized filters only remove particles larger than 1 micron (to varying degrees of efficiency). The finer solids that conventional filters leave behind include harmful species like insoluble varnish and soot. These are responsible for fluid darkening, and they can easily deposit on or erode the high-precision servo valves that make up the heart of an EHC system. Clearly, these critical systems require advanced filtration solutions that actually manage the harmful contaminants that cause costly losses, failures, headaches and waste.
Graduate to the Next Generation ECR® Product Line-up
Recently you’ve met EPT Clean Oil’s NEW ECR® 10000 , backed by patented ICB® technology, proprietary ECR® Collectors, TMR® N2 water removal, and high-efficiency filtration. ECR 10000 puts these complimentary technologies on a single platform that provides results greater than the sum of its parts. But don’t just rely on any old electrostatic collector in that beautiful EHC fluid conditioning system…
It’s time to graduate to EPT Clean Oil’s Next Generation ECR Collector, which offers advanced particle capture efficiency dedicated to cleaning even the most used and abused phosphate ester fluids.
This “new grad” has 5x the capacity to remove harmful sub-micron solids like soot and insoluble varnish. Better-still, it is constructed with next-gen materials and techniques, that ensure superior performance and longevity. Make sure that you maintain control of your critical electrohydraulic control system with the newest graduate from the school of Lubricant Chemistry Management: EPT Clean Oil’s NEW ECR Collector.
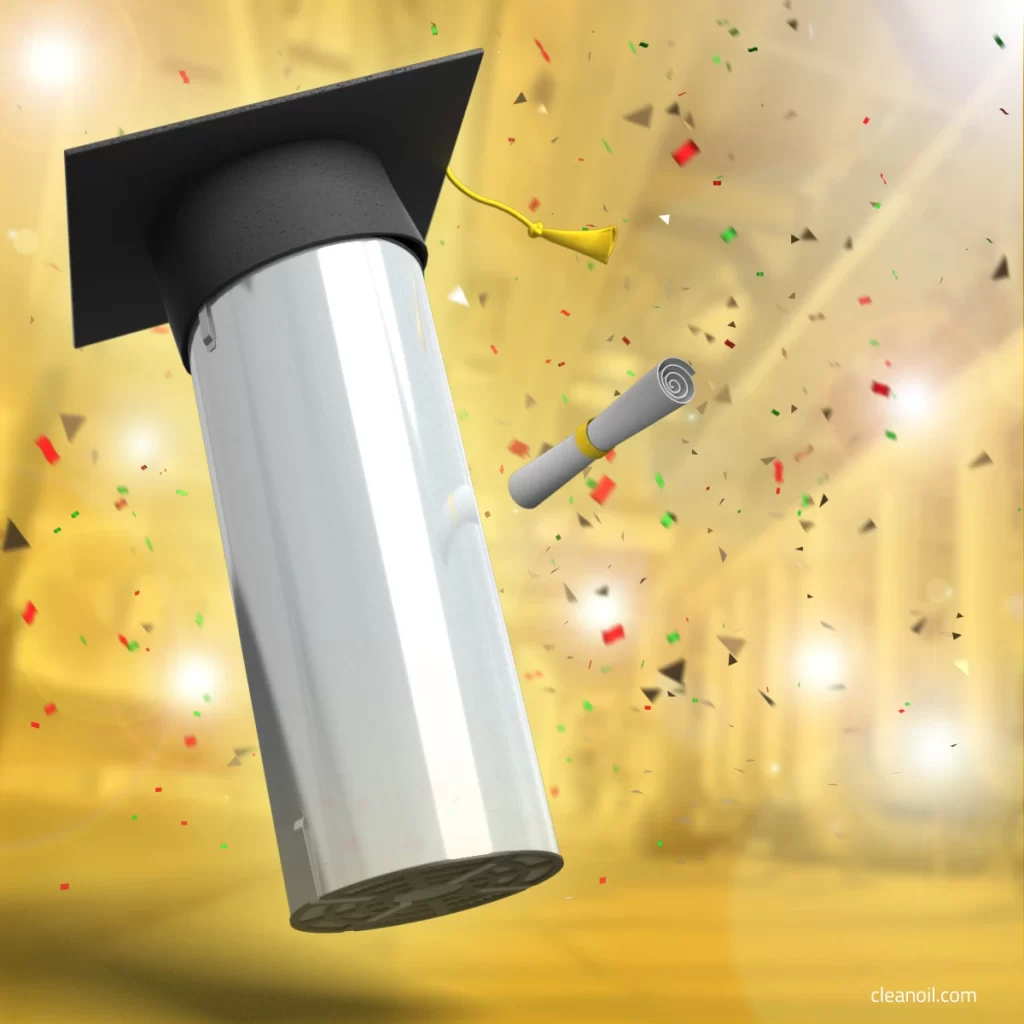
It’s June. Isn’t it time that your phosphate ester maintenance program got ready to graduate to the next level?
.