Four Questions To Ask When Selecting Varnish Removal Systems
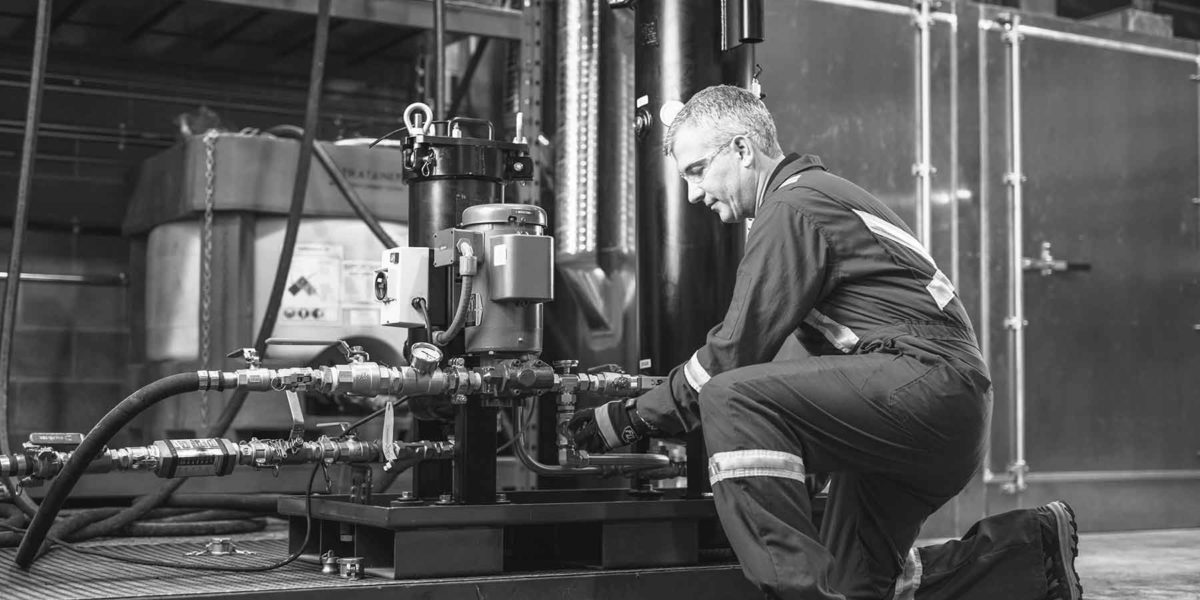
1. Does the system work during normal turbine operation when the varnish is dissolved in the oil?
While particulate removal technologies offer very important benefits, such as reducing wear, they are ill equipped to remove varnish. Why? It can take up to 72 hours to precipitate or deposit after oil is cooled. Particulate removal technologies are capable of removing insoluble contaminants from a varnish-saturated oil but they cannot prevent saturation. As a result they cannot truly solve the varnish issue.
In an effort to accelerate insoluble varnish precipitation, some particulate removal systems use a cooler on the inlet. This is an attempt to force dissolved varnish out of solution before it goes through the filter. Using ion-exchange technology that can remove varnish and its precursors when they are dissolved is much more effective. This also offers 24/7 protection regardless of asset operating conditions.

2. What is the flow rate of the system?
Optimal lubricant varnish prevention using ion-exchange requires a system that cycles the entire reservoir volume >1x / day through the filtration system. Because the flow rate is constrained based on the volume of ion exchange resin used, attention needs to be paid to the filter size. Be careful; some varnish removal systems take 90 days to cycle the reservoir volume one time. Don’t be persuaded to buy a system that’s a few $1000 cheaper when the flow rate is insufficient – size matters!
For lubricants with high varnish levels requiring restoration, higher reservoir exchange rates may be in order.
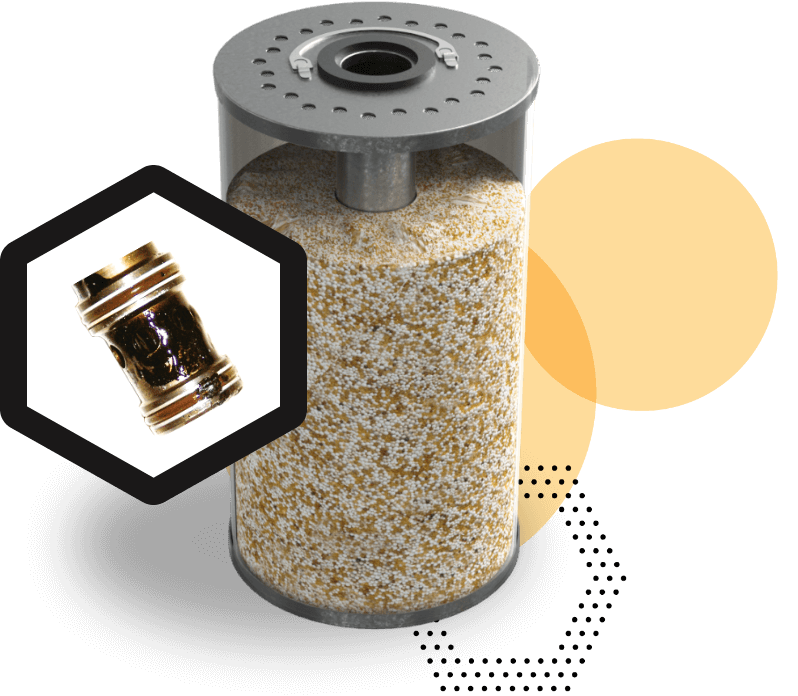
3. What is the cost of ownership over the lifespan of the system?
The cost of ownership of a varnish removal system includes the initial cost, maintenance and consumables over its lifetime. The latter can be calculated by the volume of the resin filter (e.g. per in3 or cm3). You’ll find that some systems will be up to 5x more expensive to operate than others.
Special care is required when evaluating this key point. As stated in question 2, the volume of resin used also determines the flow rate of the system, so attention must be paid to the filter size.
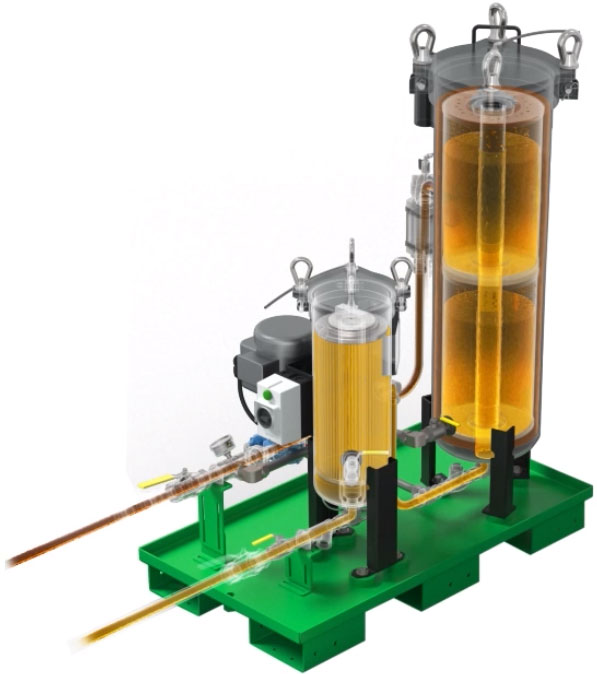
4. What is the support for the system?
Quality vendors should be available for on-site start-up and training and ongoing monitoring to document the system’s success. In addition, users need to evaluate the oil analysis used to determine the initial oil condition and show success, as standard testing often misses critical indicators.
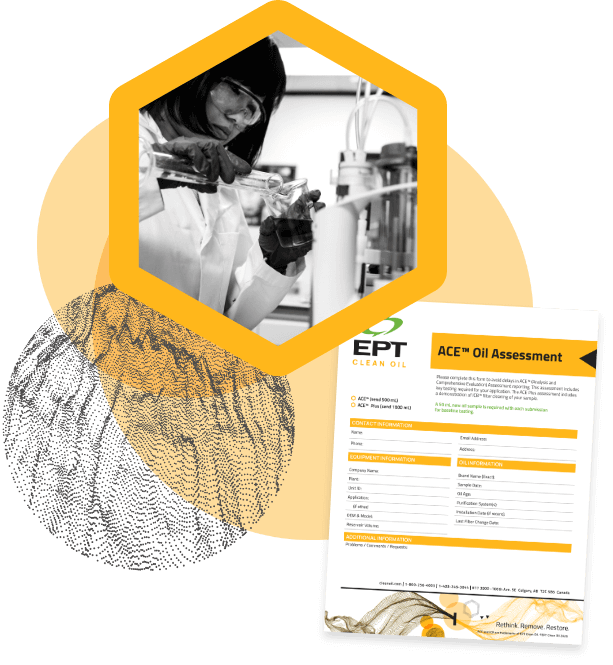