Electro-Hydraulic Control Fluid Resistivity Correction
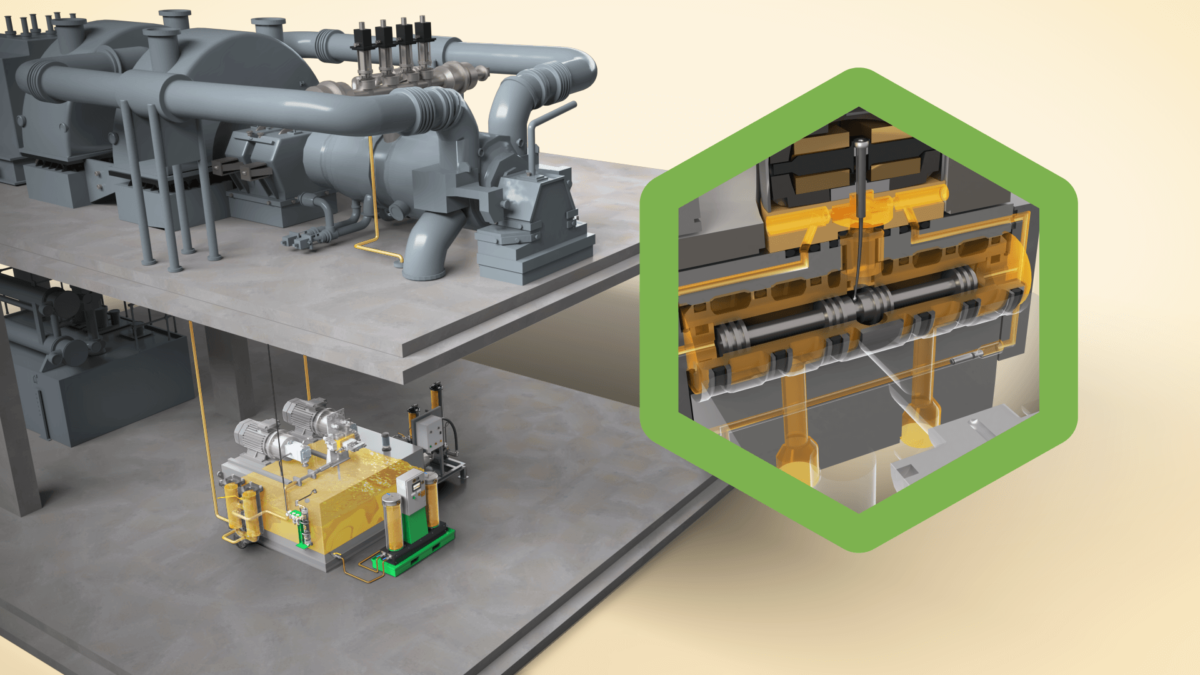
Resistivity is a critical performance indicator for electro-hydraulic control fluid (phosphate ester fluid) quality. Low resistivity values are associated with electro-kinetic wear, a common failure mechanism of servo valves. For decades, users have struggled with maintaining high resistivity over time using a variety of filtration techniques, fluid replacement and sweetening.
The following ASTM paper summary demonstrates that widely used alumina-based adsorbents produce artificial increases in resistivity that can be reversed with filtration. In contrast, the use of ion exchange resin technology, which has historically shown mixed results, is proven to be highly effective at producing authentic increases in resistivity when specific resin types are used.
Electro-Hydraulic control (EHC) fluids are used in hydraulic systems, turbines and compressors for their superior fire-resistant properties. High resistivity is a desirable quality in phosphate ester (PE) fluids used in Electro-Hydraulic Control (EHC) systems as it reduces streaming-current erosion (electro-kinetic wear) of servo valve mechanical surfaces. The build-up of contaminants, such as acids and metals, reduces PE fluid resistivity, increasing the potential for electro-kinetic wear.
PE fluids are typically run through acid-scavenging filters to increase resistivity. However, while higher resistivity values indicate a lower propensity for the PE fluid to cause electro-kinetic wear, as the following study shows, it does not always imply that the fluid is free of damaging contamination.

The build-up of contaminants, such as acids and metals, reduces electro-hydraulic control fluid resistivity, increasing the potential for electrokinetic wear.
Conventional Electro-Hydraulic Control Fluid Treatment Methods
When electro-hydraulic control fluids fall below a specific resistivity threshold, one method to clean them is to use acid-scavenging media, such as Selexsorb® GT activated alumina-based adsorbent (ABA). However, laboratory experiments have shown that this method introduces contaminants from the media in the form of very small, abrasive aluminosilicate particles (Fig. 1).
Because these particles are dielectric, they artificially increase the specific resistance of the PE fluid when suspended, creating the appearance of good fluid condition. When filtration is used to remove the contaminating particles, the measured resistivity of ABA-treated PE fluids drastically decreases. A thorough analysis of four other parameters that affect resistivity: acidity, dissolved metals, chloride and moisture content, unequivocally confirm that the aluminosilicate particles alone result in the artificial increase in resistivity. ABA treatment, therefore, masks the PE fluid’s true resistivity. Moreover, the contaminating particles can catalyze fluid degradation and cause mechanical wear.

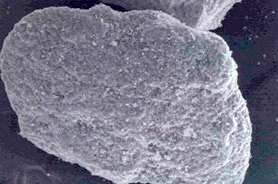
Ion-exchange technology truly extends the functional life of electro-hydraulic control fluids through proper conditioning, without the addition of deleterious contaminants.
Ion Exchange Based Electro-Hydraulic Control Fluid Treatment
An alternative method to treat PE fluids using ion exchange resin technology was also shown to increase resistivity in laboratory tests. At first glance, the ion exchange resin appeared to be less effective than ABA; however, when subjected to the same post-treatment filtration, the PE fluid retained its increase in resistivity (Fig. 2). The other four fluid properties linked to resistivity were also shown to be equal or better following ion exchange versus ABA treatment.

To demonstrate the broad applicability of ion exchange in PE fluid treatment, 11 resins were tested with 50 real-world samples from EHC systems involved in power plant operations. The results showed that different resin families differed in their ability to enhance resistivity while simultaneously improving other fluid properties (Fig. 3). Of the resins examined, a proprietary resin provided the best average resistivity improvement. This extensive study demonstrates that the use of a properly selected ion exchange resin can make PE fluid resistivity a non-issue.

Conclusions
Conventional filtration methods, such as ABA, were shown to release aluminosilicate particle contaminants, which artificially increase PE fluid specific resistance and can result in accelerated equipment wear and fluid degradation rates. Ion exchange technology truly extends the functional life of electro-hydraulic control fluids through proper conditioning, without the addition of deleterious contaminants. Not all ion exchange resins are created equal, with proprietary formulas providing superior performance.