The Importance of Varnish and Contamination Removal in Nuclear Power Plants
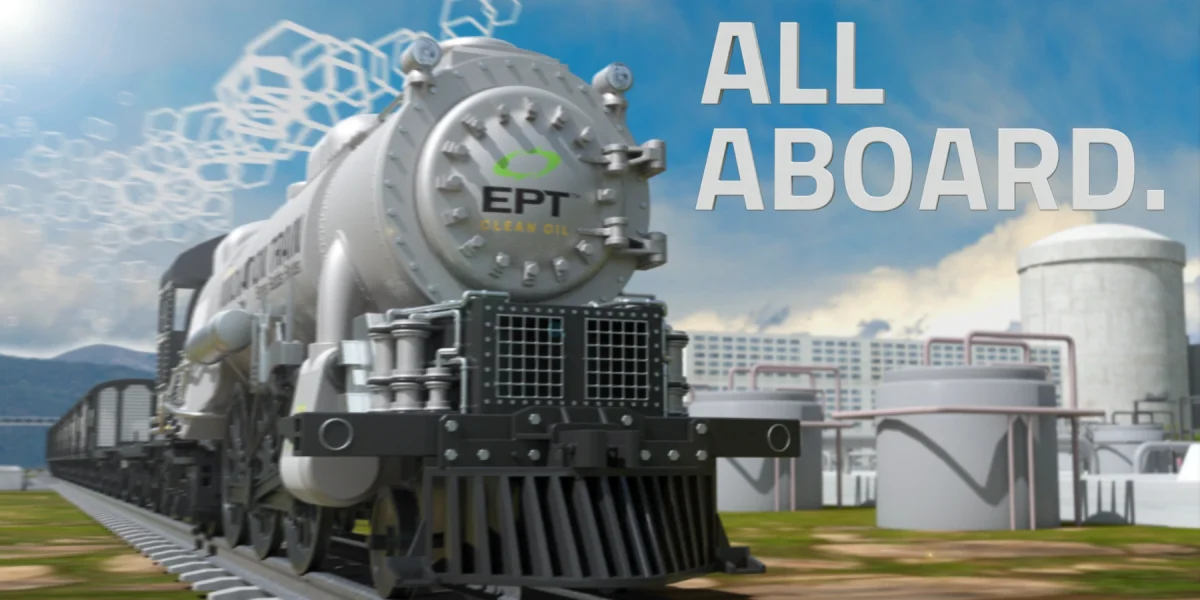
Varnish formation in nuclear power plants is a significant issue that can result in substantial operational risks, decreased efficiency, and expensive downtime. Nuclear power plants depend on turbine and auxiliary lubrication systems, including critical Electro-Hydraulic Control (EHC) systems, to ensure smooth and continuous operation, making varnish removal an essential maintenance practice. In high-temperature environments like nuclear power plants, lubricant breakdown causes the accumulation of soft sludge and hard varnish deposits on crucial components.
EHC systems play a vital role in the safe and efficient operation of nuclear power plants. These systems are responsible for precisely controlling steam turbines, reactor coolant pumps, and other critical processes, using high-pressure phosphate ester-based hydraulic fluid to regulate steam turbine valves and other safety-critical components. These systems must maintain optimal reliability to ensure smooth load transitions, emergency shutdowns, and system stability. Failures in EHC systems can lead to expensive downtime, safety hazards, and regulatory non-compliance.
Why Varnish and Contamination Removal Is Crucial in Nuclear Power Plants
Prevents Equipment Failures
- Varnish buildup can cause servo valves, bearings, and control systems to stick or malfunction.
- Restricted oil flow due to varnish deposits leads to overheating and potential turbine shutdowns.
Maintains Operational Efficiency
- Clean lubrication systems ensure optimal turbine performance.
- Reducing varnish prevents unnecessary energy losses and maintains power output.
Reduces Unplanned Downtime
- Varnish-related failures can result in costly outages, affecting power supply reliability.
- Regular varnish removal ensures continuous operation and reduces emergency maintenance costs.
- Unplanned outages are costly. A turbine trip due to EHC system failure can lead to immediate power generation loss. Estimated downtime costs can range from $500,000 to $1 million per day for a 1,000 MW plant.
Extends Lubricant and Equipment Life
- Removing varnish prevents premature oil degradation, reducing the frequency of oil changes. A complete fluid change can cost $250,000 or more, plus downtime for flushing and refilling.
- Protects turbine components, reducing wear and tear and extending asset life.
- Valve replacements can cost $50,000–$100,000, and actuator failures may require full system overhauls.
Enhances Nuclear Safety and Compliance
- A malfunctioning turbine lubrication system due to varnish increases the risk of system failures. EHC system failures can lead to loss of turbine control, forcing emergency shutdowns.
- Nuclear plants must comply with strict maintenance standards, with varnish control being key to complying with European Nuclear Safety Regulators Group(ENSREG) and Nuclear Regulatory Commission (NRC) regulations.
- Regulatory compliance violations can result in significant fines and operational restrictions.
Prevent EHC System Failures with Proactive Fluid Conditioning and Contamination Control
Meet ECR® 12000
ECR® 12000 is a fully integrated complete contamination removal skid designed to meet and exceed fluid quality requirements under ASTM D8323-24 and GEK 46357_K. The ECR 12000 incorporates four proprietary filtration technologies, including patented ICB® ion-exchange filtration to control acid, phenol, metal, varnish removal, and resistivity correction, proprietary ECR® electrostatics to manage nanoparticulate, varnish, color, and patch weight reduction, TMR® water removal to maintain moisture levels <500 ppm to prevent hydrolysis and acid formation, and high-efficiency particulate filtration at 1um β1000, extending fluid life.
Using the in-line real-time condition monitoring sensors that monitor temperature, ISO particulate count and water content, early detection of fluid degradation is available through daily automated reports and on-demand monitoring.
The Proof is in the User Experience
An Operator has three coal-fired steam power plants that use phosphate ester hydraulics for the turbine main steam stop/control valves. These three plants have suffered greatly from varnishing, high acid levels, water ingress, and particulate contamination for years and have experienced horrible reliability.
- ETD pilot spools/directional valves sticking constantly
- Internal components of the main control header pressure block prematurely fail due to high acid levels
- Actuator cylinder wear patterns and chrome etching due to high varnish and acid levels in the phosphate ester fluids
After introducing the legacy ECR® 8000 skid years ago, they started seeing improved reliability in their weekly ETD servo tests, as well as less wear and corrosion on hydraulic components in the main control header pressure block.
The ECR 12000 skid took the technology from the ECR 8000 and added patented ICB® ion-exchange technology, TMR® water removal and particulate filters into one package. The ECR 12000 system at the plant has seen a significant decrease in weekly ETD servo tests that result in stuck or failed tests. Hydraulic component inspections on plant/turbine overhauls indicate cleaner and functional conditions of the components.
The added onboard inline sensing of moisture, ISO codes, ECR voltages, and milliamp draw helps operators monitor the skid’s performance. It also helps operators to determine the frequency of filter changes on these skids. This is the only filtration technology the operator has seen on the market that can address all the common fluid contamination issues found on EHC systems using phosphate ester fluids.
ECR® 12000 is a must-have specialized solution for hydraulic and turbine EHC systems and the steam turbine power generation industry. The technology, delivered as a compact skid, can tackle all the common fluid contamination issues in phosphate ester fluids.
Power Generation Operator
The Proof is in the Results
H.B. Robinson Nuclear Power Plant in Hartsville, South Carolina, the first nuclear power plant in SE USA, commissioned on March 7, 1971, operating a Westinghouse 759 MW PWR utilizing Fyrquel 220 phosphate ester fluid, was experiencing routine failures.
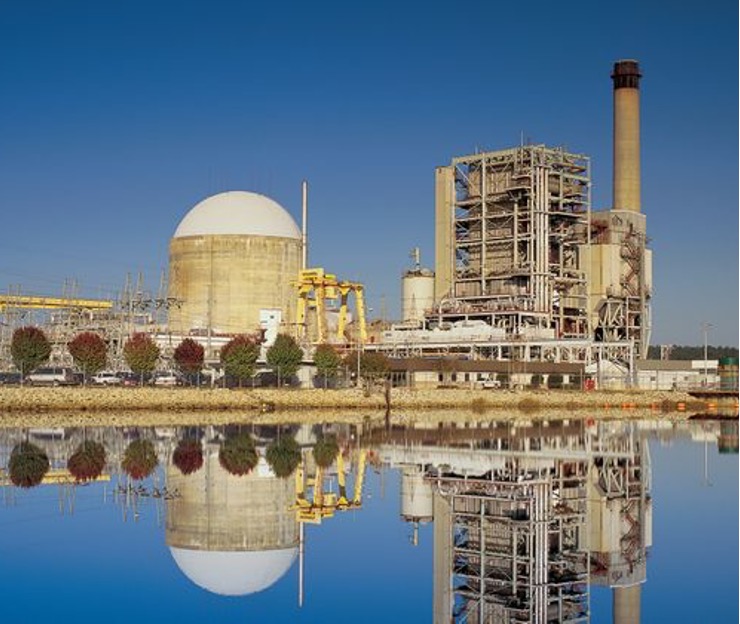
The original filtration system design included a 10-micron Fuller’s Earth filter at the pump discharge and a polishing filter loop. Later, a 3-micron mechanical filter was added in a kidney loop, as well as a dry air reservoir blanket.
The Westinghouse experienced many mechanical failures, including replacing the mechanical trip device, repeated fluid replacement, valve sticking and failure to actuate or return to position (sluggish movements). The plant had relied on the free fluid testing provided by the EHC fluid supplier, reporting routinely that fluid was within OEM specifications. In 2022, the lab raised concerns over fluid darkening. The team started digging and found our paper published in 2019 with EPRI: “What Routine EHC Fluid Analysis Misses.” The paper discussed the importance of MPC testing and other parameters that were not in the testing provided by the EHC fluid supplier.
EPT Clean Oil was engaged at this time, requesting an ACE™ Assessment. The results revealed critical MPC values (ΔL = 66), a high amount of submicron particulate with a patch weight of 7.1 mg/50mL, high foaming tendency, elevated levels of dissolved metals and over-dried fluid with water content <100 ppm.
EPT Clean Oil recommended the ECR 12000 to solve the fluid issues resulting in:
- MPC (varnish): -99%
- Varnish Precursors (phenols): -82%
- Patch Weight: -93%
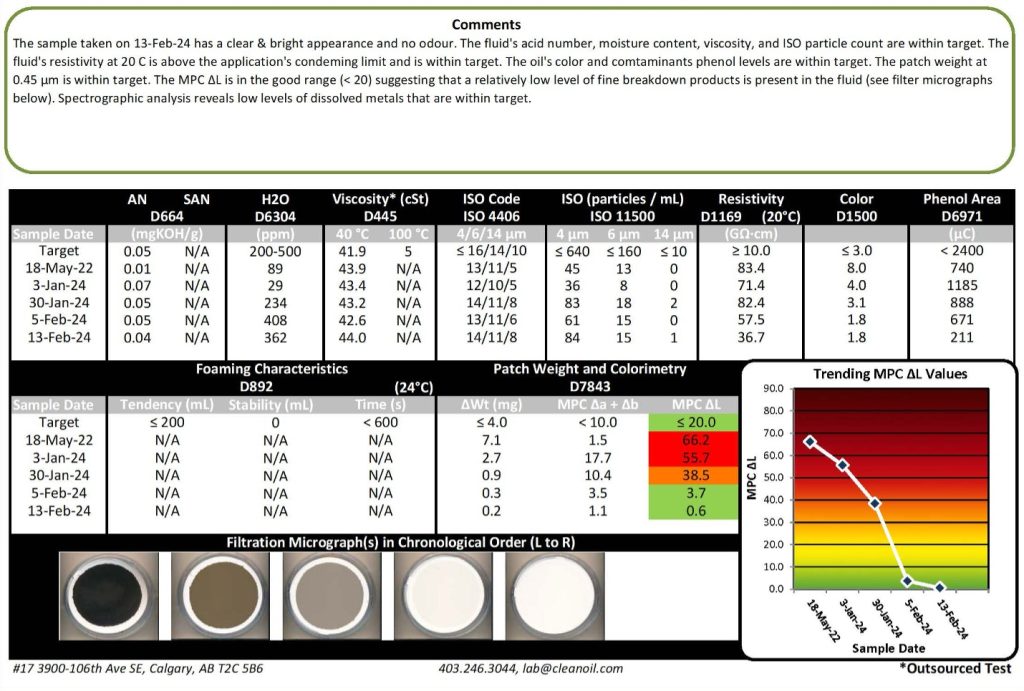
Conclusion
Maintaining clean lubrication systems is essential for the efficiency and safety of nuclear power plants. Implementing proactive strategies to remove varnish and contaminants helps prevent equipment failures, reduce maintenance costs, and ensure continuous power generation.
By utilizing advanced technologies for varnish and contamination mitigation, such as ECR 12000, along with proactive maintenance strategies, we can extend the lifespan of components, minimize costly failures, and comply with regulatory standards. This approach safeguards critical assets and supports optimal operational performance.
It’s time to take action. All Aboard!
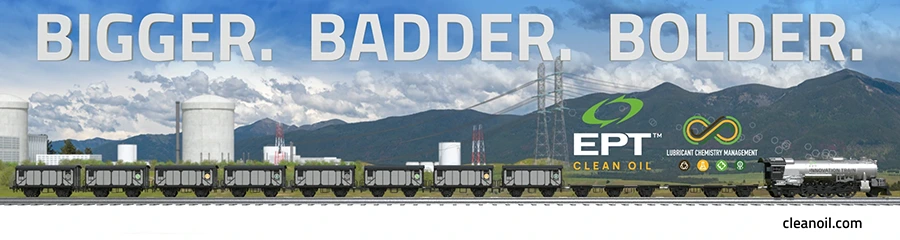