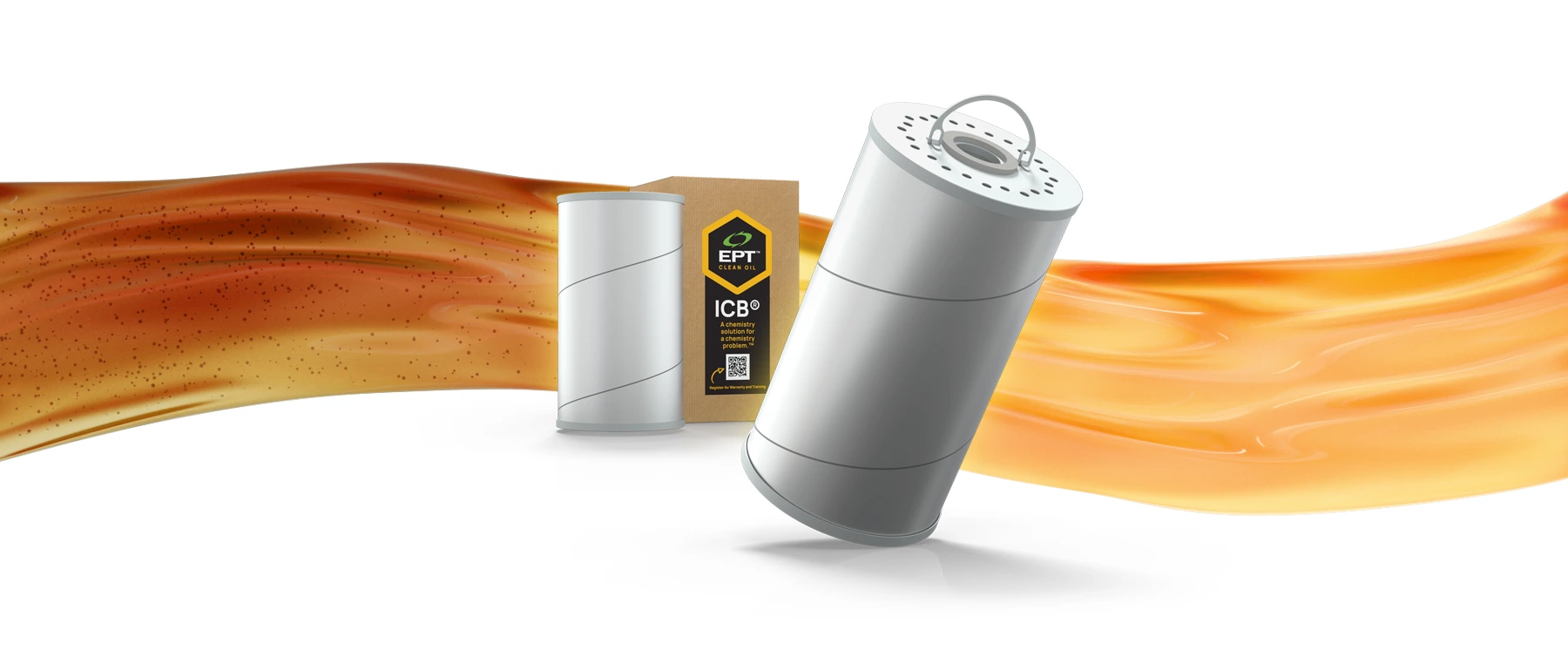
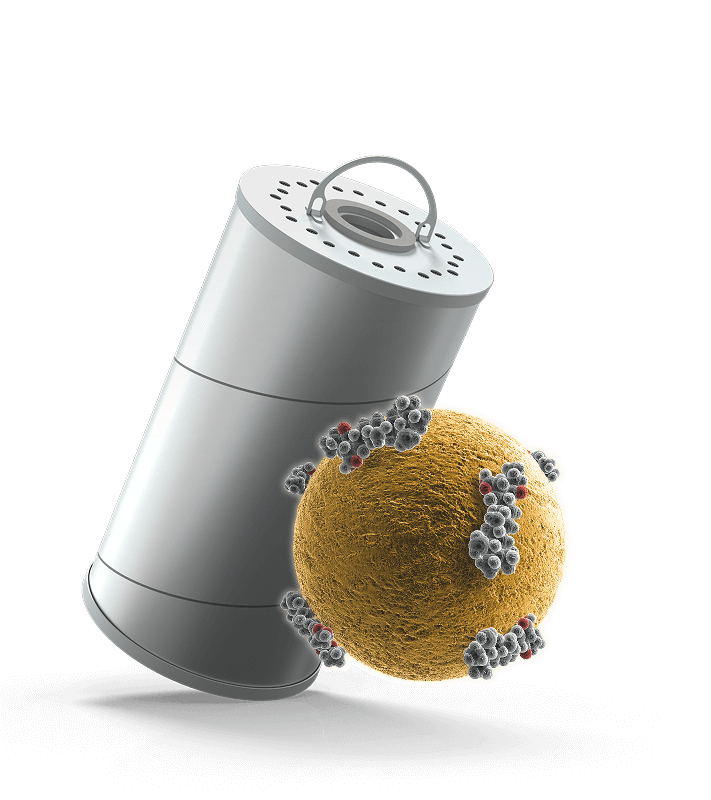
Protect your critical asset with ICB FRF for Phosphate Ester Fluid
Phosphate esters are fire-resistant fluids (FRFs) used in turbine electro-hydraulic control (EHC) systems throughout the power generation industry. Used primarily for their fire-resistant properties and thermal stability, these synthetic fluids hydrolyze and oxidize readily during service, creating harmful acids and phenols. These breakdown products are established varnish precursors that must be removed to ensure reliable servo valve performance in EHC systems.
ICB® FRF, patented ion-exchange technology, is designed to address phosphate ester chemistry, removing acids, phenols and varnish while simultaneously improving resistivity. More importantly, ICB FRF removes varnish precursors responsible for the primary mechanical failure pathways in EHC systems. With 30 years of proven results, ICB FRF is an engineered workhorse designed to address phosphate ester fluid chemistry, preventing EHC failures and saving end-users hundreds of thousands of dollars in costly fluid replacement and system flushing.
Protect your critical turbine electro-hydraulic control (EHC) system with a bulletproof vest.
Meet ICB® Ion-Exchange Filter
WatchICB FRF Features and Benefits
- 10x more acid-scavenging capability
- The only filter system specifically engineered to remove FRF varnish
- Eliminates the cause of servo valve sticking
- Eliminates servo strainer plugging
- Improves resistivity and fluid color
- Manages fluid chemistry, extending fluid life, reducing consumption costs and environmental impacts
- Removes dissolved metals such as calcium, magnesium and sodium which are contributed from obsolete acid filters
- Creates a trouble-free operating environment with predictable outcomes and costs
- Eliminates the need for costly chemical flushes
- Maintains fluid condition standards required by ASTM D8323: Standard Guide for Management of In-Service Phosphate Ester Based Fluids for Steam Turbine Electro-Hydraulic (EHC) Control Systems
- Drop-in replacement for OEM filters, sized to fit existing acid-scavenging systems (retrofit)
CASE STUDY
This case study highlights the reduction of varnish potential by 95% after installing an SVR® FRF.
CASE STUDY
This case study highlights varnish potential and resistivity being brought back into specification after installing an SVR® FRF.
ICB FRF
Safe, reliable and cost-effective chemistry solution for in-service phosphate ester FRFs focused on the root cause of EHC problems: acid formation and varnish accumulation.
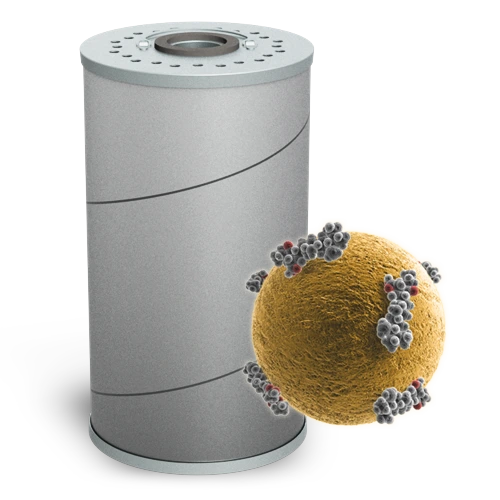
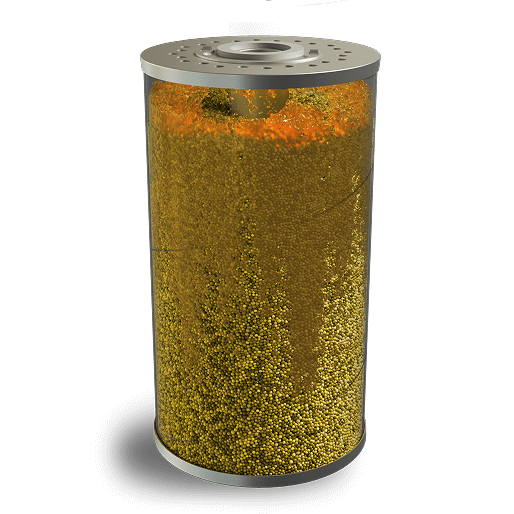
You Are One Step Closer to Trouble-Free Operation
Understanding if you comply with ASTM D8323 is a crucial first step in the trouble-free operation of your critical turbine electro-hydraulic control system. Routine analysis packages offer insight, but they are not submitting the complete picture, providing a false sense of security.
EHC Fluid Case Study
Site “A” featured a Boiling Water Reactor with a generating capacity of 680 MW. Operators at Site “A” relied heavily upon the complementary analyses provided by their fluid manufacturer. These routine analysis reports suggested that their EHC fluid was in good condition. They were, therefore, startled when a servo failure precipitated an unplanned 30-day outage. During this span, the cost of lost production reached the tens of millions of US dollars.
A subsequent root cause investigation revealed that the servo failure had been precipitated by “particulate etching.” This proved to confound since “routine” oil analysis had shown acceptably low particle counts. Indeed, the EHC fluid’s poor condition did not become truly apparent until it was passed through a 0.45 µm filter patch as part of an MPC test. This test revealed that high levels of fine insoluble breakdown products and varnish were present. The particle counts routinely carried out on EHC fluids are blind to these fine contaminants since they’re smaller than 4 µm. Given the high levels of fine material detected by MPC analysis, the finding that servo valves were etched is no longer surprising; it is most unfortunate that the fine varnish responsible for this failure was only discovered after it had already occurred.
This case study highlights a significant inadequacy in the current condition monitoring programs of many EHC users: costly and avoidable failures are occurring as a result of contaminants that aren’t being “routinely” tested for.
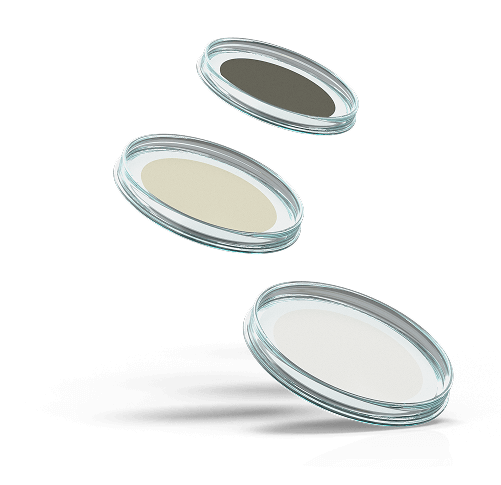
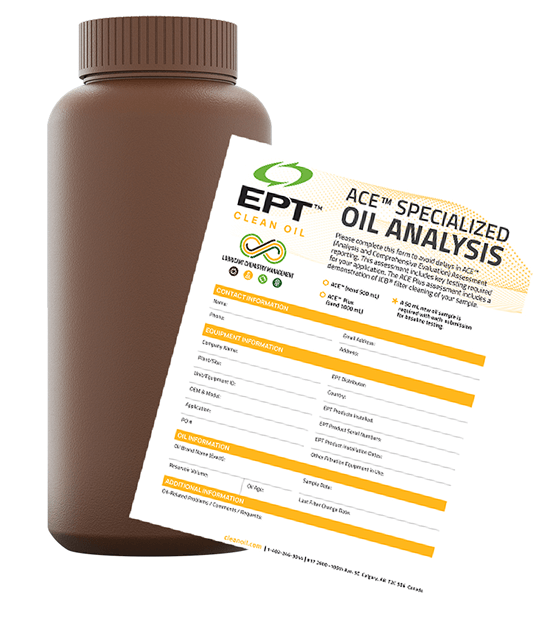
Submit an oil sample today to get a comprehensive, ASTM D4378-compliant understanding of your in-service oil’s condition and remaining lifetime so that it can be aligned with future maintenance windows and proactive strategies for optimization.
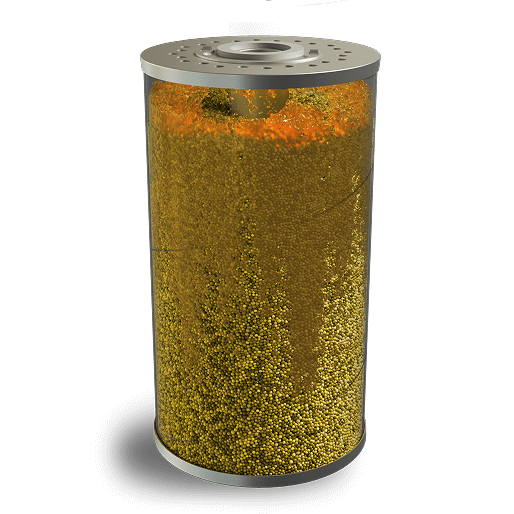
Routine Analysis Isn’t Good Enough When it Comes to Your Critical FRF
An Operator, relying heavily on complementary analyses provided by their fluid manufacturer, was confident their EHC fluid was in good condition. They were, therefore, startled when a servo failure precipitated an unplanned 30-day outage. During this span, the cost of lost production reached the tens of millions of US dollars.
The root cause investigation revealed that the servo failure had been precipitated by particulate etching. While routine oil analysis had shown acceptably low particle counts, when the EHC fluid was passed through a 0.45 µm filter patch as part of an MPC test, the test revealed high levels of fine insoluble breakdown products and varnish were present. Routine analysis is blind to these fine contaminants since they’re smaller than 4 µm.
Our Fluid Technical Center is Your Answer Center
EPT Clean Oil’s Fluid Technical Center is a state-of-the-art lubricant research facility, offering specialized analysis and comprehensive evaluations. We take the routine out of oil analysis, providing a complete picture of your phosphate ester fluid’s condition per the guidelines provided in ASTM D8323.
From advanced testing to the expert interpretation of results, our team of professional and Ph.D. chemists are here to provide the data you need to make informed decisions about your critical assets. You can expect more when you partner with our Fluid Technical Center.
Our Phosphate Ester test package, applicable for electro-hydraulic control (EHC) oils and fire-resistant fluids, includes:
- Acid Number
- MPC Varnish Potential
- Patch Weight
- Resistivity (20°C)
- Phenol Levels
- Water Content
- ISO Particle Count
- Dissolved Metals
- Fluid Color
- Viscosity (40°C)
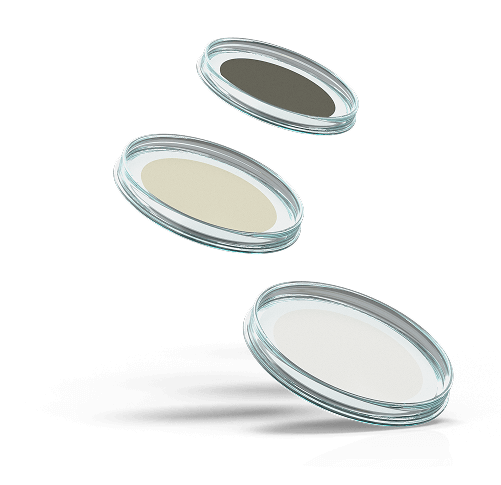
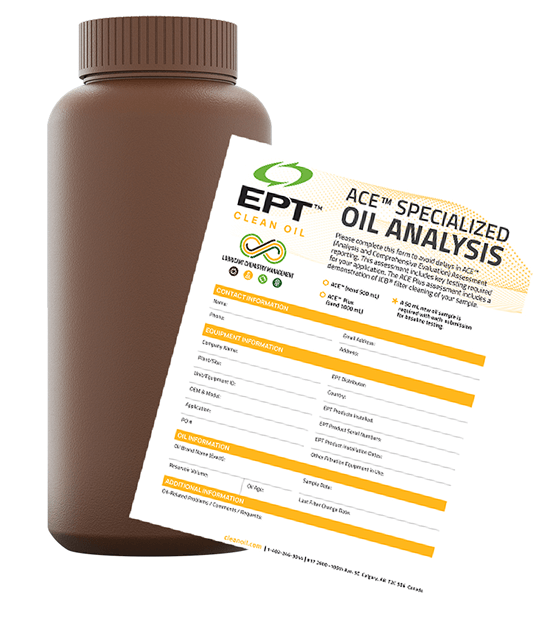
Submit an oil sample today to get a comprehensive, ASTM D4378-compliant understanding of your in-service oil’s condition and remaining lifetime so that it can be aligned with future maintenance windows and proactive strategies for optimization.
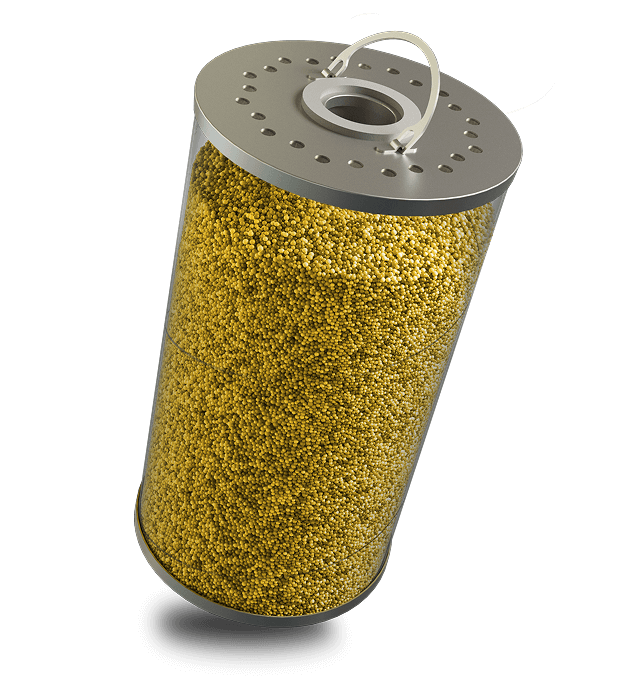
ICB FRF Plug and Play Solution
ICB® FRF is sized to fit existing OEM acid-scavenging systems as a drop-in replacement for obsolete filters. To retrofit ICB FRF into an existing system, there are 3 ‘commandments’ to follow.
- FLUID FLOW
ICB FRF offers optimized axial flow to maximize bed depth and media contact time resulting in lower velocity. For this reason, flow is significant and must be adhered to. Flow is the essential property in determining the performance of your system. Flow measurement via an installed flow meter or manual calibration is required to retrofit. - FLUID TEMPERATURE
ICB FRF is engineered to work at a fluid temperature of ≥40°C (104°F) and <85°C (185°F). Depending on the viscosity working outside of these fluid temperatures can result in increased differential pressure and is not recommended. - OPERATING PRESSURE
The minimum operating pressure when using ICB FRF is 2 bar or 25 psi or 3.5 bar or 50 psi on the high side. Poor fluid quality, low temperatures, or increased flow rate will cause pressure to be higher.
Note: Bleed the filter vessel before installing ICB FRF to ensure there isn’t an airlock. This will ensure that flow between stacked filters is achieved in scenarios where two filters are utilized.
Meet the Ideal Match for ICB FRF
Proactive FRF Conditioning with an SVR® Kidney Loop System
Meet SVR®, an engineered, skid-mounted, kidney loop lubricant conditioning system designed to protect and manage phosphate ester fluid and asset reliability. Backed by patented ion-exchange technology, ICB® FRF, SVR addresses the chemistry of phosphate ester fluids, maintaining key parameters and preventing fluid breakdown. The SVR lubricant conditioning system is ideally used when existing acid removal systems are undersized or if pressure and flow cannot be controlled.
Providing 200-400% more filtration capacity than most OEM systems, SVR provides an engineered solution with redundant fail-safes to return and maintain your phosphate ester fluid reservoir to optimal condition.
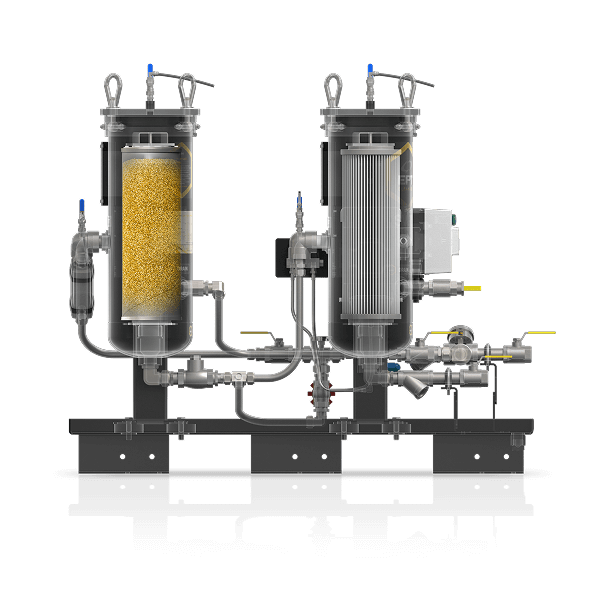
SVR Features and Benefits
- Quickly reduces Acid Number and prevents servo valve sticking
- Uses ICB FRF: the only acid-scavenger specifically engineered to remove FRF varnish
- Proven protection against solid and dissolved varnish
- Significantly improves fluid resistivity, mitigating the risk of current corrosion
- Significantly reduces solid contamination
- Engineer approved system designed to facilitate rapid approval and deployment
- Very low maintenance and time requirements – turn it on and let it run
- No downtime – SVR can be installed without an outage