Lubricant Maintenance Program Route Planning
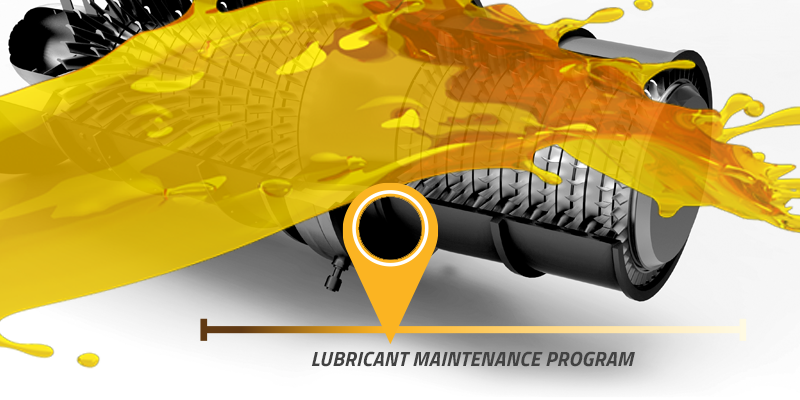
Next Stop: Leveraging Oil Analysis Data to Determine Maintenance Priorities
In part two of our Lubricant Maintenance and Testing series Lubricant Maintenance Program Route Planning, we explore how to leverage oil analysis program data to prioritize requirements and effectively implement maintenance solutions.
As a brief recap from part one in this four-part series, lubricants don’t die suddenly. They usually die after relatively long periods of neglect. The challenge is that few oil-related problems arise in the first half of a lubricant’s life, making it easy to turn a blind eye to the gradual degradation during their service.
Eventually, however, the consequences of unmanaged fluid breakdown surface. The typical results are:
- Increased MPC varnish potential
- Antioxidant additive depletion
- Accumulated oxidation material deposited on equipment surfaces
But lubricant death is not inevitable.
Suppose we consider the root cause of lubricant failure and adjust our maintenance practices to slow down or manage that process. In that case, lubricant aging can be stopped in its tracks, keeping oils healthy and extending their lives significantly. This approach allows for more reliable, sustainable, and profitable operations; it’s simply a better way of doing things.
It starts with the right oil analysis test done at the right time and to the industry standard test method.
Next Stop: Lubricant Maintenance Program Improvements
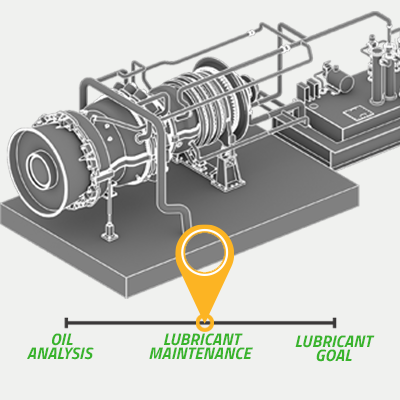
While most users expect their testing programs to meet the demanded standards, two issues are commonly observed that severely limit the effectiveness of the overall maintenance program.
1. To hold or not to hold is the question that needs to be asked when it comes to MPC testing.
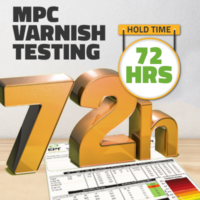
It starts with looking at your reports to see if the MPC value is reported alongside the hold period in hours. If it is not reported, then your MPC testing does not comply with the test standard defined in ASTM D7843.
MPC values can increase the longer the oil is in the sample bottles demanding a 72-hour hold period. As defined in the test standard, all samples must be reset and then aged to a uniform standard.
The challenge for Oil Analysis Labs is that following the test standard makes MPC a 100-hour test which does not fit within the regular operating processes of most labs. What is not readily understood by the labs and users alike is that there is no point in doing MPC testing outside of the established test standards because the reported values are meaningless. By doing the MPC test incorrectly and reporting erroneous MPC values, users are left with many false positives, which causes the misallocation of maintenance resources and makes it impossible for users to assess the effectiveness of existing maintenance programs.
2. Remaining lubricant life is unknown or not understood.
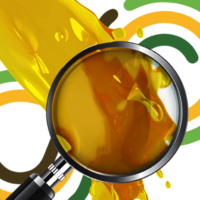
ASTM D4378 is the in-service guide for gas and steam turbine lubricants. Antioxidant testing (LSV) is required as part of this standard and is suggested to be done at least quarterly. The end of a lubricant’s operating life is dictated by a 75% reduction in antioxidants in combination with a high acid number. With quarterly tests as prescribed by the test standard, users can trend these values four times per year, year over year, and determine the average annual consumption rate.
For example, if a lubricant consumes 20% of its primary antioxidant per year, that roughly translates to an expected five-year operating life. With this information, you can advance the sophistication of the program in three important areas:
- Determine lubricant replacement intervals 36 months in advance and coordinate with your maintenance windows. This eliminates surprise oil replacements or the risk of operating lubricants beyond their service life.
- The same oil brand in the same mechanical system type should have similar antioxidant consumption rates. Determining average rates of antioxidant consumption by oil brand and machine type provides insight into lubricant performance, including base oil and additive quality. With operating baselines determined, you can optimize lubricant purchasing decisions and identify situations where abnormal rates of additive consumption exist, suggesting excess temperatures, duty cycle or mechanical issues that are developing.
- From a sustainability perspective, with the rates of antioxidant consumption understood, we can monitor the effectiveness of the overall maintenance program. We can assess the performance of lubricant maintenance programs and optimize towards programs that result in lower rates of additive consumption.
Beyond Oil Analysis: Implementing Effective Maintenance
With an effective Lubricant Analysis program, the next step is to leverage this program to produce results for your entire fleet, determining starting points and priorities for maintenance. With this data, we can classify all lubricant systems as either being in specification or out of specification. Ideally, we want to document compliance that each lubricant reservoir is in specification.
1. Compare lubricant test results to industry limits.
a. In specification and can be maintained in ideal operating condition.
b. Out of specification and can be restored to ideal operating condition.
c. Grossly out of specification and the lubricant needs to be replaced.
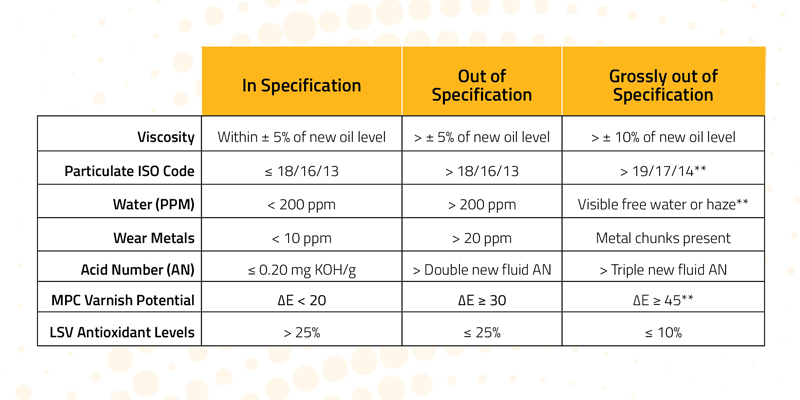
2. Once you have reviewed and classified your fleet according to these three categories, the obvious priorities are to return your units that are outside of specification back to specification within three months or as quickly as possible. In this situation, there will be two approaches based on whether the lubricant is within that range of recovery.
a. For systems within the range of recovery, Lubricant Recovery Programs provide the equipment, hoses, and consumables on a rental basis without any long-term commitments.
b. For units out of specification and requiring replacement, system restoration programs are recommended to clean up the oil while replacement is being scheduled. These programs should be performed on-line for 3 months in advance of oil replacement, allowing existing varnish deposits to be removed from the mechanical components before replacement. This not only protects the new oil, but also eliminates the technical risks associated with incompatibility with the varnish deposits and the new oil. Depending on the circumstances, this can also eliminate the need for flushing between oil changes.
3. For systems in specification, lubricant maintenance programs are recommended to keep you lubricant operating in optional condition. The sooner in the lubricant life cycle that Lubricant Chemistry Management is implemented, the more impact it will have on extending lubricant life by reducing the amount of antioxidants consumed. By managing fluid chemistry consistently, you eliminate the accumulation of oxidative breakdown materials that would otherwise impair the rate of antioxidant consumption. This approach also protects the additive in the new oil added as part of regular operation.
Overall, the Lubricant Maintenance Program Route Planning approach provides condition-based guidance, allowing users to prioritize requirements and implement corrective actions while maximizing the effectiveness of their maintenance programs. For technical questions or support, please email a specialist at [email protected].