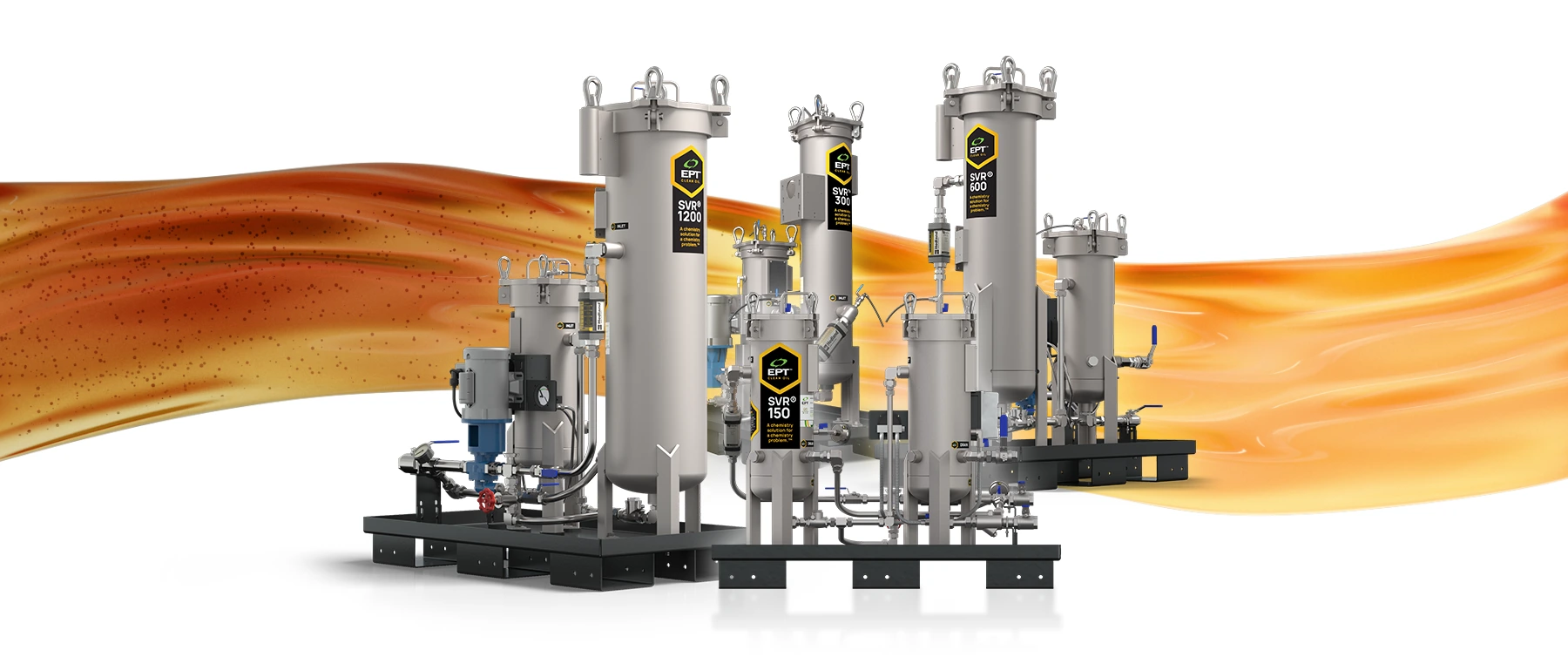
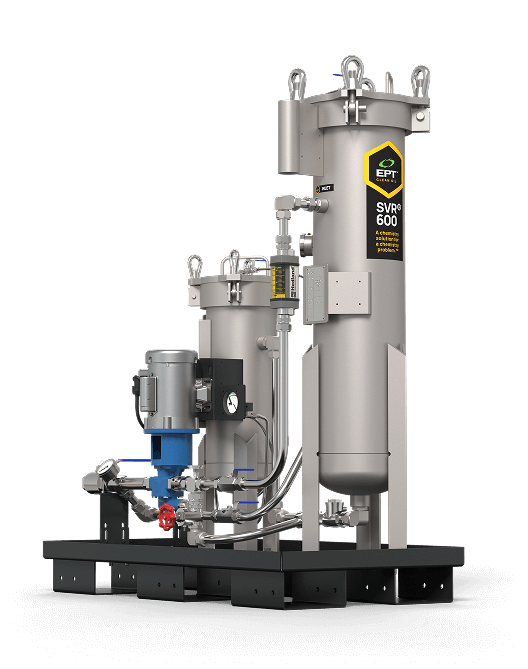
MEET SVR® RO FOR RUST & OXIDATION TURBINE OIL
From the first day, a lubricant is put into service, it begins to accumulate dissolved oxidation by-products – the feedstock of varnish, constraining the life of the oil. These oxidation by-products accumulate until the lubricant has no remaining capacity, forcing any excess into insoluble material. Based on their polarity, this insoluble material is more attracted to metal surfaces, creating solid varnish – a common failure mechanism. In the absence of active lubricant chemistry management, oxidation by-products will accumulate, guaranteeing this failure mechanism will occur. Furthermore, this contamination increases the rate at which additives are consumed, significantly reducing the life of the oil.
SVR® RO is an engineered skid-mounted dialysis-style lubricant conditioning system that manages fluid chemistry full-time, removing oxidation by-products as they are created. Backed by patented ion-exchange technology, ICB® RO, SVR RO eliminates the molecules that should not be in the oil, returning the lubricant to a highly unsaturated condition, forcing any existing varnish deposits to be dissolved back into the oil via chemical equilibrium.
By employing SVR RO to continuously eliminating the dissolved oxidation material during regular turbine operation, the root cause of varnish is eliminated. The result: the acid number never increases, MPC never increases, and oil performance is consistent throughout its lifecycle. Additive life is also extended as the secondary reactions with accumulated oxidation by-products that would otherwise occur are eliminated, significantly extending lubricant life.
CASE STUDY
This case highlights how SVR® RO solved varnish formation in turbine lubricants caused by oxidation by-products, improving MPC varnish potential by 94%.
CASE STUDY
This case explores how advanced solutions with the SVR® RO helped resolve varnish-related failures and prevent further disruptions.
SVR RO Features and Benefits
- Utilizes patented ICB® RO ion-exchange filters to remove soluble varnish contaminants at the molecular level preventing the oil from becoming saturated and forming varnish deposits
- Dramatically reduces varnish potential as measured by the Membrane Patch Colorimetry test (ASTM D7843-21)
- Eliminates varnish-related problems in all turbine-system components
- Quickly removes varnish deposits
- Reduces ISO particle-counts
- Manages fluid life with as little as 5% annual top up
- Creates potential for fluid life to be extended for the life of the turbine
- Avoids flushing and related downtime
- Eliminates need for expensive after-market additives
- Engineer approved system designed to facilitate rapid approval and deployment
- Manufactured to ISO 9001 standards
- Very low maintenance and time requirements outside of routine ICB and mechanical filter replacement (results dependent)
- No downtime – SVR RO can be installed without an outage
SVR RO owners receive a complete support program, including complimentary oil analysis and expert interpretation from our professional and Ph.D. Chemists until the results have been documented. After results have been confirmed, owners are given the option to continue the analysis program for a quarterly fee.
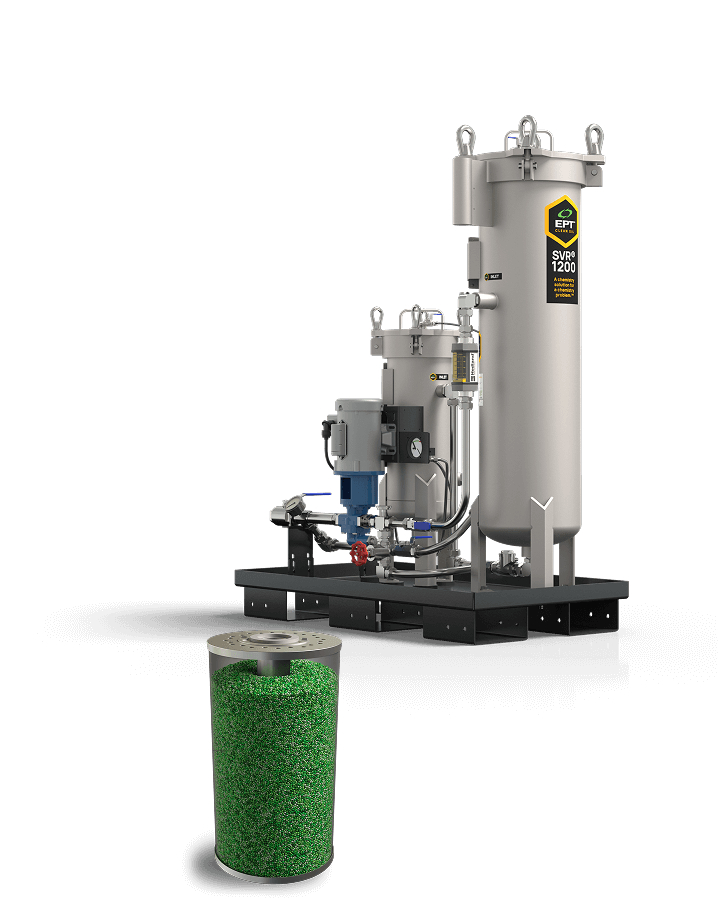
SVR RO Sizing Comparison Chart
For normal turbine or compressor oil maintenance, the desirable flow rate is to exchange the fluid reservoir volume 1 – 2x per day. For recovery projects, higher exchange rates are desired.
Use the comparison tool to gain a comprehensive comparison of the SVR RO with other SVR OIL varnish removal systems, highlighting key differences and benefits.
SVR® HYDRO | SVR® 150 | SVR® 300 | SVR® 600 | SVR® 1200 | |
![]() | ![]() | ![]() | ![]() | ![]() | |
Reservoir Volume (Mineral Oil) | Minimum: 2,500 L/ 660 gal Maximum: 15,000 L / 3,963 gal | Minimum: 715 L / 189 gal Maximum: 2,870 L / 758 gal | Minimum: 1,440 L / 380 gal Maximum: 5,740 L / 1,516 gal | Minimum: 3,785 L / 1,000 gal Maximum: 16,278 L / 4,300 gal | Minimum: 5,980 L / 1,579 gal Maximum: 27,255 L / 7,200 gal |
Reservoir Volume (Synthetic Oil) | Minimum: 240 L / 63 gal Maximum: 960 L / 253 gal | Minimum: 480 L / 126 gal Maximum: 1,912 L / 505 gal | Minimum: 1,435 L / 379 gal Maximum: 5,680 L / 1,500 gal | Minimum: 2,272 L / 600 gal Maximum: 9,085 L / 2,400 gal | |
ICB Flow Rate | 19.0 lpm / 5.0 gpm | 2.0 lpm / 0.5 gpm | 4.0 lpm / 1.0 gpm | 12.0 lpm / 3.0 gpm | 19.0 lpm / 5.0 gpm |
System flow rate through high efficiency filtration | 38.61 lpm / 10.2 gpm | 8.0 lpm / 2.1 gpm | 8.0 lpm / 2.1 gpm | 38.61 lpm / 10.2 gpm | 38.61 lpm / 10.2 gpm |
ICB Filter Model | RO | RO FRF JET AW | JRO FRF JET AW | RO FRF JET AW | RO FRF JET AW |
Fluid Applications | Rust and oxidation turbine oil only at this time | Rust & Oxidation Turbine Oil (RO) Phosphate Ester Fluid (FRF) Aeroderivative Turbine Oil (JET) Anti-Wear Hydraulic Oil (AW) | Rust & Oxidation Turbine Oil (RO) Phosphate Ester Fluid (FRF) Aeroderivative Turbine Oil (JET) Anti-Wear Hydraulic Oil (AW) | Rust & Oxidation Turbine Oil (RO) Phosphate Ester Fluid (FRF) Aeroderivative Turbine Oil (JET) Anti-Wear Hydraulic Oil (AW) | Rust & Oxidation Turbine Oil (RO) Phosphate Ester Fluid (FRF) Aeroderivative Turbine Oil (JET) Anti-Wear Hydraulic Oil (AW) |
Other Proprietary Filters and System Requirements | TMR® AquaPurge Coalescer | For synthetic oils, it is advised to combine a TMR® N2 for water removal | For synthetic oils, it is advised to combine a TMR® N2 for water removal | For synthetic oils, it is advised to combine a TMR® N2 for water removal | For synthetic oils, it is advised to combine a TMR® N2 for water removal |
Contaminant Targets | Soluble Varnish Insoluble Varnish Oxidation by-products Water Particulate removal | Soluble Varnish Insoluble Varnish Particulate removal | Soluble Varnish Insoluble Varnish Particulate removal | Soluble Varnish Insoluble Varnish Particulate removal | Soluble Varnish Insoluble Varnish Particulate removal |
Electrical Options | General Purpose electrical only at this time | General Purpose with 50 Hz and 60 Hz electrical voltage options CSA Class 1 Div 1 Group C&D with 50 Hz and 60Hz electrical voltage options CSA Class 1 Div 2 Group A, B, C & D with 50 Hz and 60 Hz electrical voltage options IECeX and ATEX-approved configurations are available. Please get in touch with us for more information. | General Purpose with 50 Hz and 60 Hz electrical voltage options CSA Class 1 Div 1 Group C&D with 50 Hz and 60Hz electrical voltage options CSA Class 1 Div 2 Group A, B, C & D with 50 Hz and 60 Hz electrical voltage options IECeX and ATEX-approved configurations are available. Please get in touch with us for more information. | General Purpose with 50 Hz and 60 Hz electrical voltage options CSA Class 1 Div 1 Group C&D with 50 Hz and 60Hz electrical voltage options CSA Class 1 Div 2 Group A, B, C & D with 50 Hz and 60 Hz electrical voltage options IECeX and ATEX-approved configurations are available. Please get in touch with us for more information. | General Purpose with 50 Hz and 60 Hz electrical voltage options CSA Class 1 Div 1 Group C&D with 50 Hz and 60Hz electrical voltage options CSA Class 1 Div 2 Group A, B, C & D with 50 Hz and 60 Hz electrical voltage options IECeX and ATEX-approved configurations are available. Please get in touch with us for more information. |
The Truth About Solid (Insoluble) Contamination
In many critical applications, particularly gas turbines, varnish contamination is not the result of insoluble contamination. While removing insoluble contaminants is a benefit to any oil system. Removing deposited varnish requires very clean fluid for prolonged periods and an environment where the varnish is not being continuously produced. Short-term benefits are possible from removing insoluble material, but varnish deposits often re-emerge after a short period because insoluble removal is not directly correlated with varnish production.
Lubricant varnish usually is dissolved in the oil during equipment operation when the oil is hot. Insoluble contamination removal using particulate removal technologies is ineffective when the oil is at operating temperature because the varnish is not in the particulate form. Therefore, particulate removal devices, including electrostatic oil cleaners, agglomeration devices, and depth filtration systems, offer no benefit from varnish mitigation during regular equipment operation.
Insoluble contamination is only part of the equation. Together soluble and insoluble contamination accounts for 98%+ of the contamination that creates varnish.
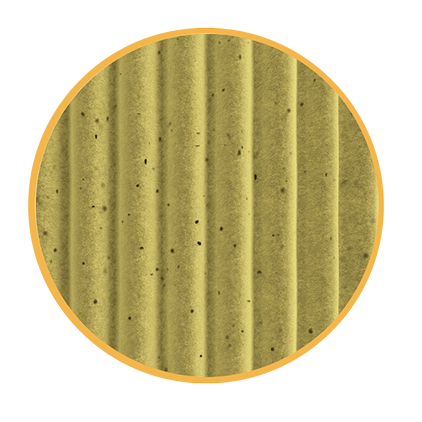
Soluble and Insoluble Contamination Create Varnish
During regular turbine operation, in-service turbine lubricants break down due to oxidation, producing dissolved oil breakdown products – this soluble contamination is the feedstock for varnish deposits. Depending on the level of soluble contaminants, lube oil systems with low-flow areas such as peaking/cycling gas turbines are particularly susceptible to varnish problems. In these low-flow areas, the varnish will form on valves during downtime when the fluid temperature cools and soluble contaminants accumulate to form varnish.
The lubricant’s solvency can be restored and maintained at new fluid values by removing the dissolved breakdown products as they are formed. More importantly, any deposits created from the same lubricant will be dissolved back into the oil.
Widely used worldwide to restore and maintain very low varnish potential numbers, SVR RO removes the contamination that causes varnish deposits without waiting for the varnish to form during regular turbine operation when dissolved in the oil. As a result, saturation cannot occur under any lubricant condition, preventing varnish formation. Other varnish removal equipment offerings fail to address this primary cause of varnish.
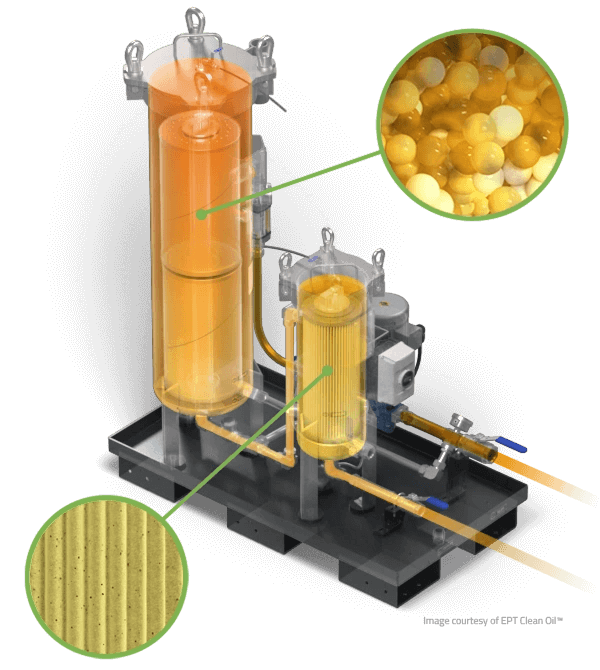
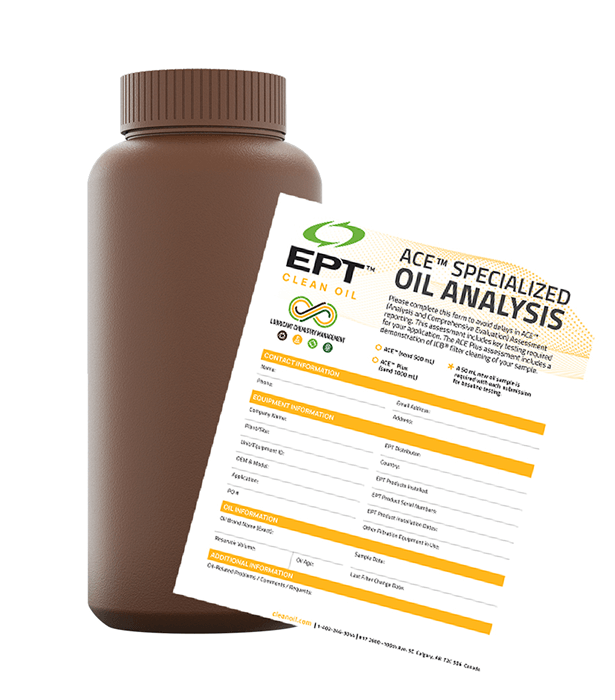
Is it time to re-evaluate your turbine lube oil maintenance strategy?
ASTM D4378 is the in-service guide for managing lubricants in turbines and compressors, stating, “oil replacement occurs when both the acid number increases 2-3x and antioxidants decrease by 75%.” Operating within this standard demands an optimized lube oil maintenance strategy focused on the rate of oxidation, acid production and additive consumption. Why?
- Oxidation material accumulates in the oil as a dissolved waste product resulting in varnish after the oil becomes saturated.
- Modern turbine oils are non-polar, and the waste products generated from oxidation are polar. This causes the oxidation material to be more attracted to metal surfaces than the oil itself.
- Oxidation material accumulation impacts oil performance, with common operating issues occurring in the middle or second half of the oil life cycle.
- The effectiveness of oil top-up decreases over time, as the additive in the new oil immediately reacts with the accumulated oxidation material in the oil.
Make Informed Decisions with our ACE™ Oil Analysis
At EPT Clean Oil, we specialize in lubricant analysis for critical rotating equipment and EHC systems. We don’t want to be a jack of all trades; our focus is on being the masters of what we do. Each sample that is sent to the Fluid Technical Center is, therefore, examined uniquely.
Our expert chemists drive the advancement of lubricant testing and management through collaboration with industry-leading organizations such as ASTM, STLE, and ICML. We thoroughly review and critically analyze your results before presenting our findings, ensuring precision and reliability. Our commitment is to deliver accurate solutions, always prioritizing quality and providing the insights you need.
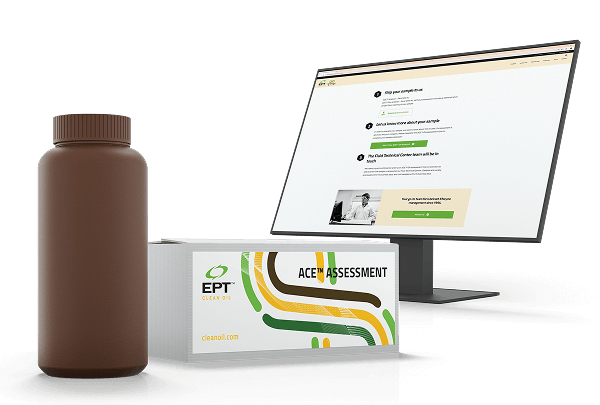