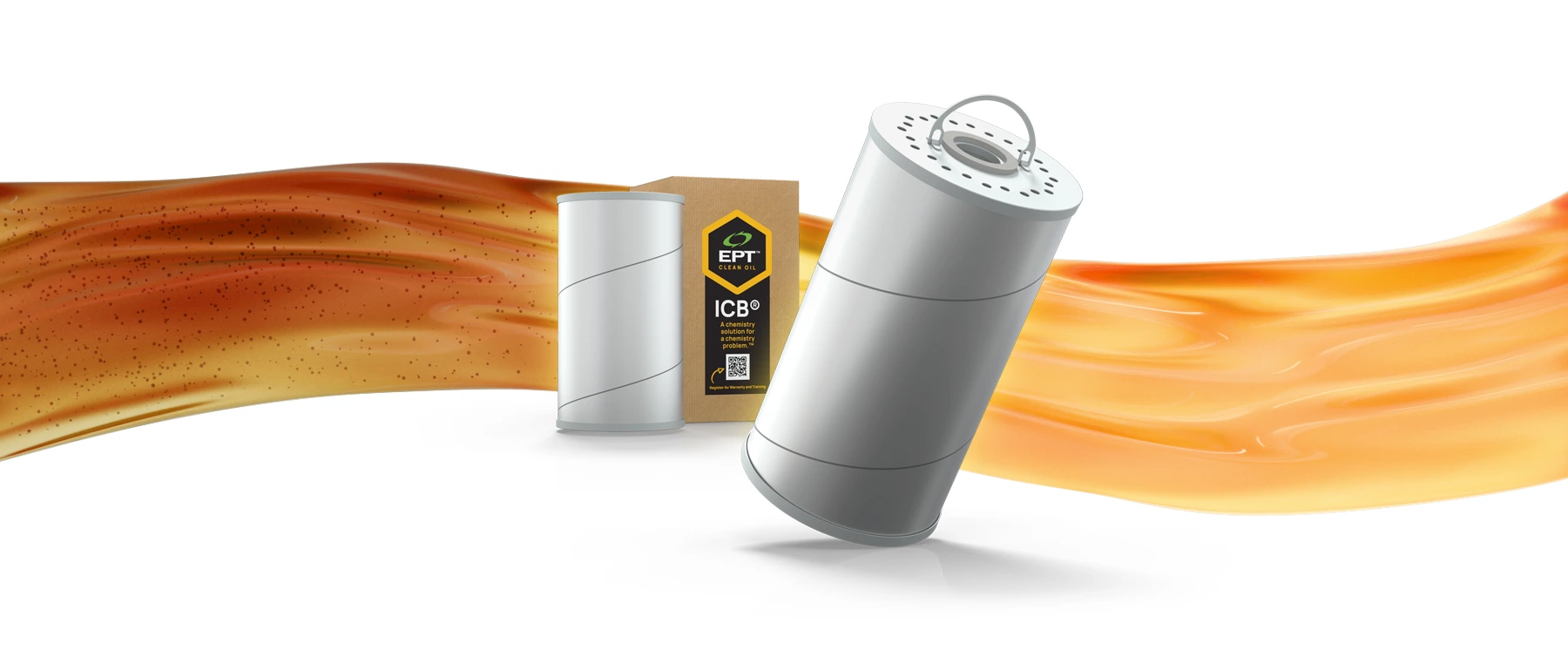
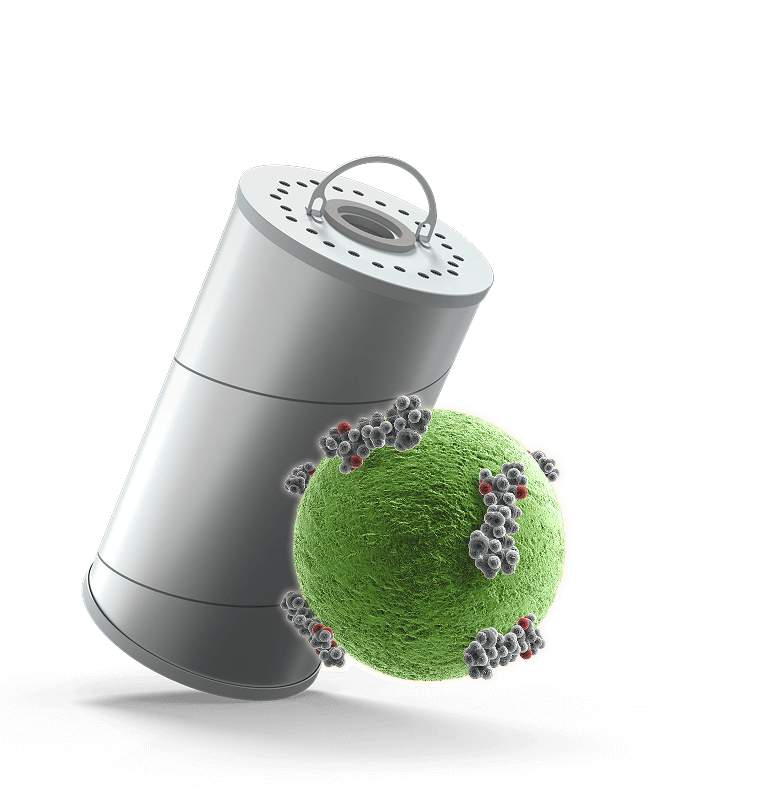
Protect your critical asset with ICB RO for Rust & Oxidation Turbine Oil
Rust and oxidation inhibited oils, also known as R&O Oils or Turbine oils, are designed for use in turbines, compressors and other rotating applications. Offering outstanding lubricating properties, these lubricants break down due to oxidation, creating dissolved contaminants from day one. These dissolved oil breakdown products accumulate until they saturate the oil, forming varnish.
ICB® RO, patented ion-exchange technology, continuously removes varnish precursors and dissolved breakdown products. Rather than waiting for these oxidation products to cause harm, ICB RO breaks the accumulation cycle, eliminating the root cause of varnish formation and improving lubricant performance.
Meet ICB® Ion-Exchange Filter
WatchICB RO Features and Benefits
- Removes and prevents all forms of varnish (solid and dissolved)
- Removes dissolved breakdown molecules that are formed as part of standard equipment operation, preventing the varnish formation cycle from starting
- Reverses the varnish formation cycle, restoring lubricant solvency and removing varnish deposits via chemical equilibrium
- Prevents varnish related bearing and servo valve failures
- Reduces MPC values and keeps them low
- Manages the fluid chemistry, minimizing the impact of oxidation, decreasing anti-oxidant additive consumption rates and extending the lubricant life
- Does not affect turbine oil additives
- Creates a trouble-free operating environment with predictable outcomes and costs
- Maintains oil condition standards required by ASTM D4378: Standard Practice for In-Service Monitoring of Mineral Turbine Oils for Steam, Gas and Combined Cycle Turbines
CASE STUDY
This case study highlights the improvement of the MPC value by 94% since installing the SVR® RO.
CASE STUDY
This case study highlights a gas plant that has been able to maintain a near 0 MPC varnish potential and 0 oil-related issues since installing an SVR® RO.
CASE STUDY
This case study highlights a power plant that reduced emulsions by 95% allowing the units coalescer to do its job after installing an SVR® RO.
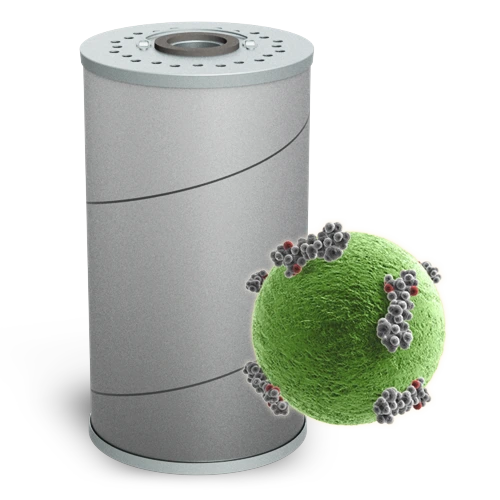
ICB RO
Safe, reliable and cost-effective chemistry solution for in-service rust and oxidation inhibited oils focused on the root cause of varnish formation: oxidation.
You Are One Step Closer to Trouble-Free Operation
Understanding your oil’s MPC varnish potential is a crucial first step in the trouble-free operation of your critical rotating equipment. MPC testing is one of the pillars of turbine oil maintenance required by ASTM D4378. As you know, other tests like Acid Number, FTIR and Antioxidant Analysis offer insight into turbine oil breakdown levels. Still, they do not provide the complete picture and can give a false sense of security on their own.
Varnish is the most common cause of oil-related downtime in critical rotating equipment. By monitoring your oil’s varnish potential, you’ll know what you’re up against, allowing you to make effective maintenance decisions that can keep your production asset up and running.
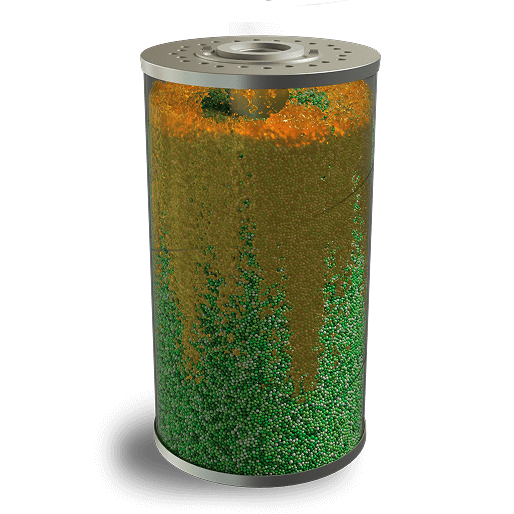
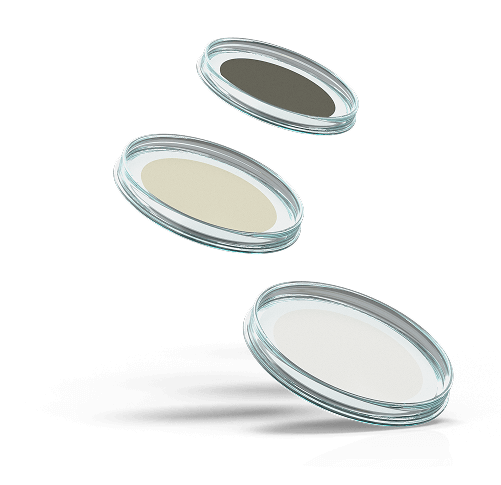
Why Routine Testing Isn’t Enough
A compressor station operator with a 44,500-horsepower turbine relied on routine testing, including Acid Number and Antioxidant Analysis, to monitor oil breakdown levels. This routine testing showed no issue with either. However, the operator noticed that their power turbine was running hot as time went on. The turbine was running so hot that its production had to be curtailed. De-rating the turbine allowed for continued operation but resulted in the loss of hundreds of thousands of dollars of potential revenue over the long term.
After running an MPC varnish potential test, the oil’s varnish potential was found to be high. The tests didn’t detect the varnish that the end-user was routinely running and had deposited on bearing and oil cooler surfaces. As a result, the turbine exceeded acceptable operating temperatures.
Submit an oil sample today to get a comprehensive, ASTM D4378-compliant understanding of your in-service oil’s condition and remaining lifetime so that it can be aligned with future maintenance windows and proactive strategies for optimization.
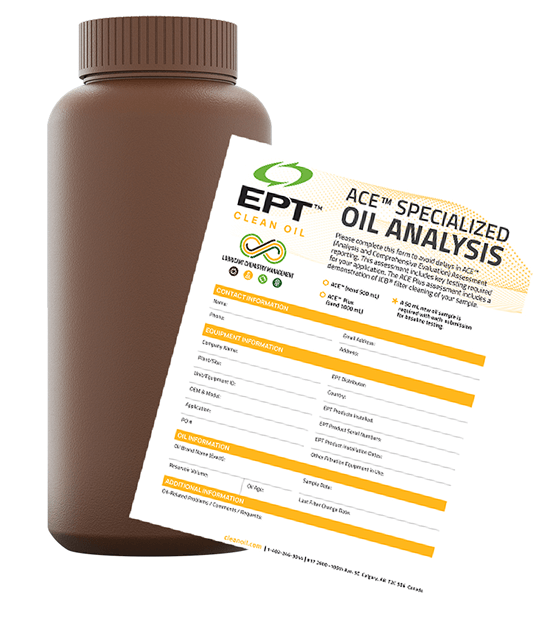
Varnish: The Most Common Cause of Oil-related Downtime in Rotating Equipment Applications
Fortunately, varnish potential testing has become a reality in the 21st century, thanks to membrane patch colorimetry (MPC). Despite widespread acceptance and ASTM approval of the MPC (D7843) test method, some turbine users still don’t monitor their oil’s varnish potential regularly. Alternative tests (Acid Number, FTIR and Antioxidant analysis) provide insight into oil breakdown, but MPC is the only test that directly looks for varnish.
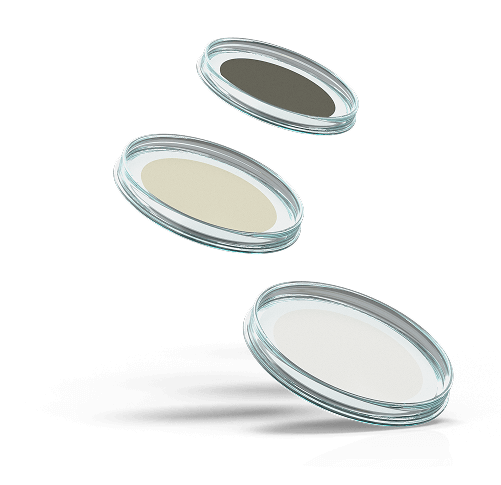
R&O Lube Oil Case Study – Why You Need to Know Your Oil’s Varnish Potential
As part of their oil maintenance program, a compressor station operator used a third-party lab to monitor their 44,500-horsepower turbine’s oil condition. The lab’s default analysis package included Acid Number and Antioxidant Analysis testing to monitor oil breakdown levels. This routine testing showed no issue with either. However, the operator noticed that their power turbine was running hot as time went on. The turbine was running so hot that its production had to be curtailed. De-rating the turbine allowed for continued operation but resulted in the loss of hundreds of thousands of dollars of potential revenue over the long term.
When the end-user asked their lab to run an MPC varnish potential test as outlined in ASTM D7843 and required by ASTM D4378, the oil’s varnish potential was found to be high. The tests didn’t detect the varnish that the end-user was routinely running and had deposited on bearing and oil cooler surfaces. As a result, the turbine exceeded acceptable operating temperatures; it is most unfortunate that this varnish was only discovered after it had already occurred.
This case study highlights a significant inadequacy in many oil analysis programs/packages: costly and avoidable problems are occurring due to contaminants that aren’t being “routinely” tested for.
Our Fluid Technical Center is Your Answer Center
EPT Clean Oil’s Fluid Technical Center is a state-of-the-art lubricant research facility, offering specialized analysis and comprehensive evaluations. We take the routine out of oil analysis, providing a complete picture of your R&O Oil’s condition as per the guidelines provided in ASTM D4378.
From advanced testing to the expert interpretation of results, our team of professional and Ph.D. chemists are here to provide the data you need to make informed decisions about your critical assets. You can expect more when you partner with our Fluid Technical Center.
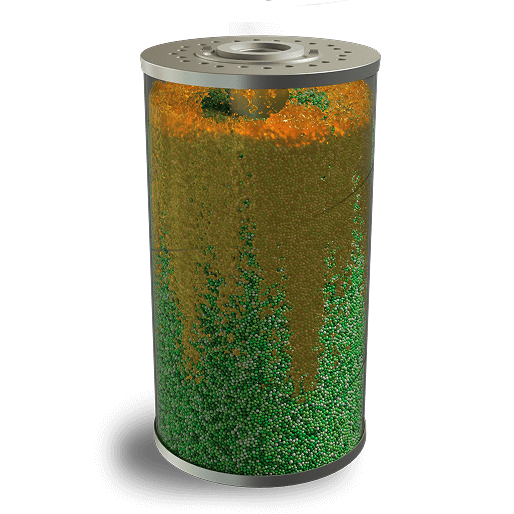
Our Lube Oil test package, applicable for mineral-based turbine lubricants and synthetic fluids with R&O additive packages, includes:
- MPC Varnish Potential
- Acid Number
- Fluid Color
- Viscosity (40°C)
- Water
- ISO Particle Count
- Dissolved Metals
- Antioxidant Levels
- Demulsibility (Steam Turbine Lube Oils)
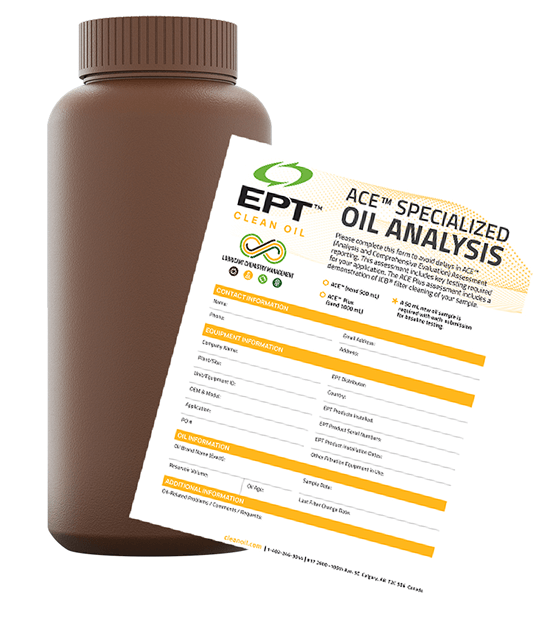
Submit an oil sample today to get a comprehensive, ASTM D4378-compliant understanding of your in-service oil’s condition and remaining lifetime so that it can be aligned with future maintenance windows and proactive strategies for optimization.
Meet the Ideal Match for ICB RO
SVR® for Varnish Removal
From the moment lubricants are put into service, they chemically break down. The primary pathway: oxidation. The result: oxidation products that dissolve in the oil. All too often, this dissolved oxidation material goes unmanaged by routine maintenance.
Modern turbine and compressor oils are non-polar, and oxidation material is polar, resulting in a tendency for this oxidation material to be more attracted to metal surfaces than the oil itself—the result: deposits on mechanical surfaces including bearings and valves.
SVR® is an engineered lubricant conditioning system that works 100% of the time, targeting the underlying cause of lubricant failure: chemical breakdown. Backed by patented ion-exchange technology, ICB RO, SVR removes acids and dissolved oxidation material as they are generated. Only by managing oxidation levels and removing oxidation material can the root cause of lubricant deposits, or varnish, be eliminated.
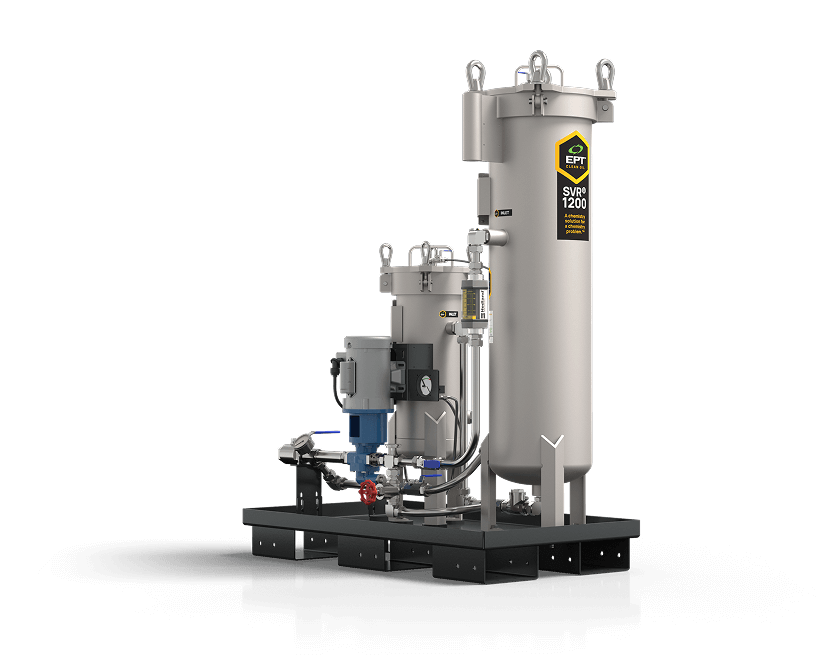
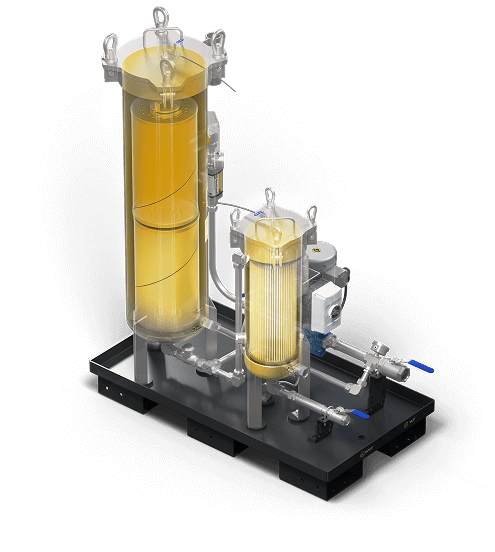
SVR Features and Benefits
- Eliminates soluble varnish at the molecular level preventing the oil from becoming saturated and forming varnish deposits
- Maintains consistent fluid quality and performance
- Restores acceptable MPC varnish potential and Acid Number (TAN/AN)
- Manages fluid life with as little as 5% annual top-up
- Creates potential for fluid life to be extended for the life of the turbine
- Avoids flushing and related downtime
- Eliminates the need for expensive after-market additives
- Engineer approved system designed to facilitate rapid approval and deployment
- Very low maintenance and time requirements – turn it on and let it run
- No downtime – SVR can be installed without an outage