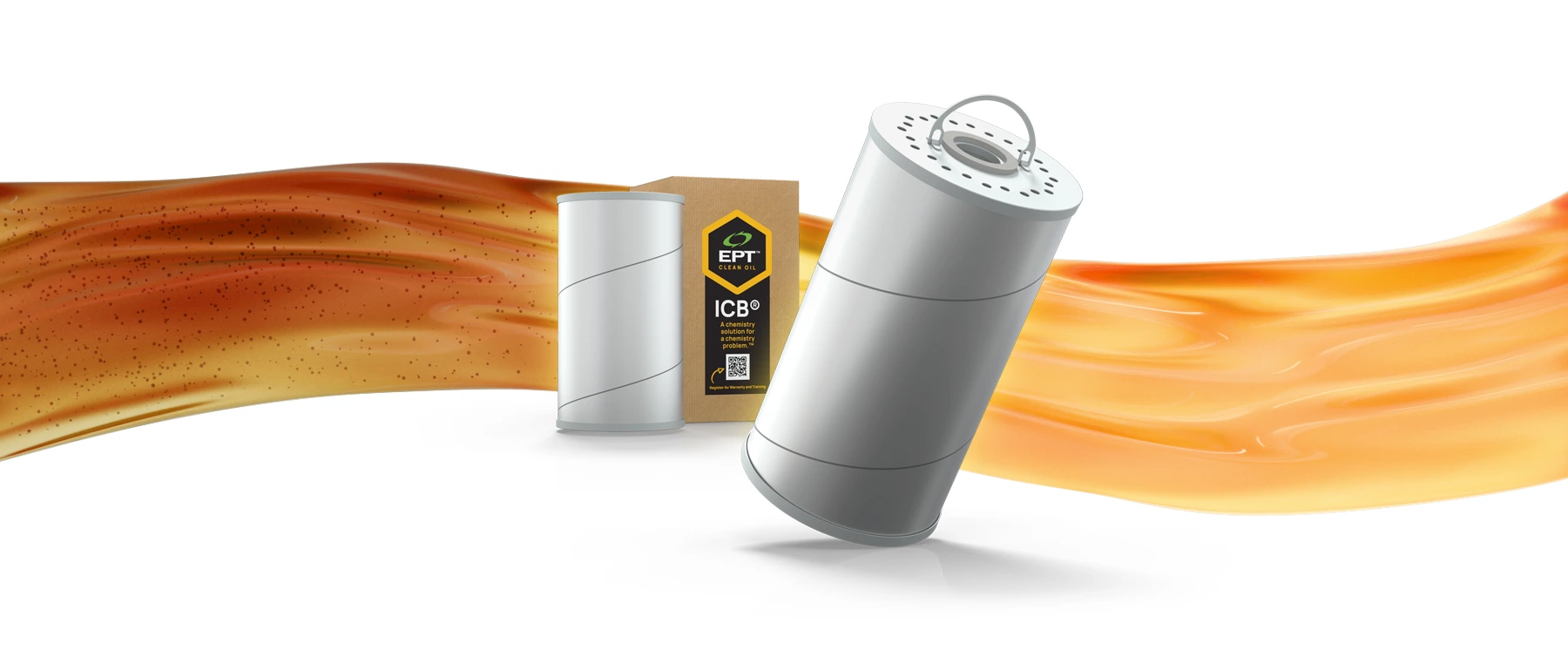
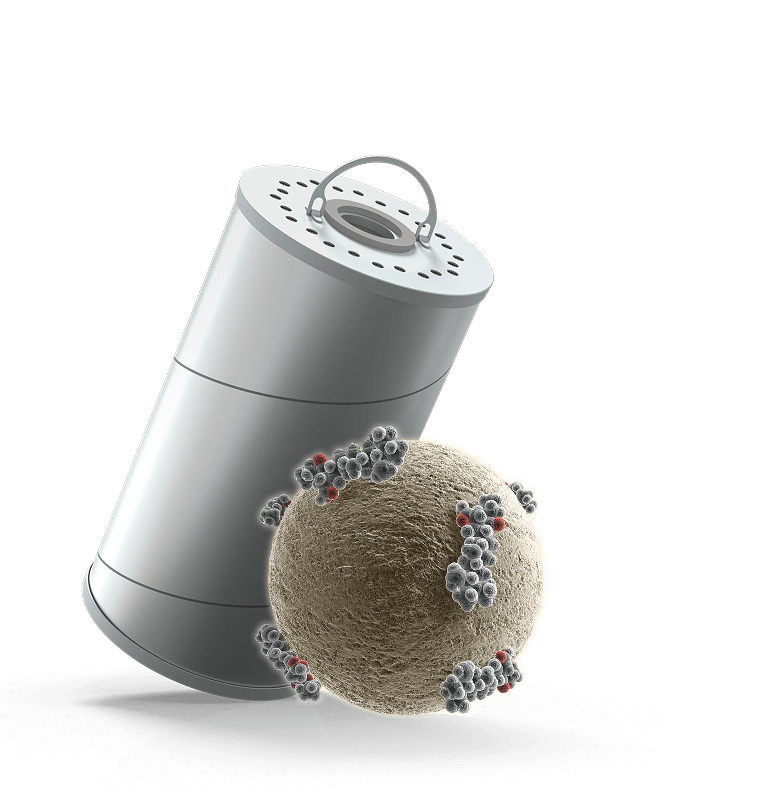
Protect your critical asset with ICB AW for Anti-wear Hydraulic Oil
Anti-wear (AW) hydraulic oils are found in various applications, from small assembly processes to integrated steel and paper mill applications. Offering excellent protection against corrosive acid and metal surface wear in critical hydraulic systems, Anti-wear hydraulic oils break down to form varnish due to oxidation of their base oil and additive depletion.
ICB® AW, patented ion-exchange technology, selectively removes varnish and key varnish feedstocks continuously. Rather than wait for these breakdown products to cause harm, ICB AW breaks the accumulation cycle preventing varnish problems.
Proactively manage anti-wear hydraulic oil chemistry with ICB AW.
Meet ICB® Ion-Exchange Filter
WatchICB AW Features and Benefits
- Selectively removes varnish and key varnish feedstocks
- Does not impact the lubricant’s antioxidant or AW additive levels (verified in advance)
- Reduces high MPC varnish potentials and maintains them when they are low
- Reduces fluid waste, disposal costs and environmental impacts
- Reduces system maintenance and failure costs
- Creates a trouble-free operating environment with predictable outcomes and costs
CASE STUDY
This case explores how advanced solutions with the SVR and ICB AW Filters helped reduce MPC varnish potential by 87%.
ICB AW
Safe, reliable and cost-effective chemistry solution for in-service anti-wear hydraulic oils focused on the root cause of degradation: oxidation.
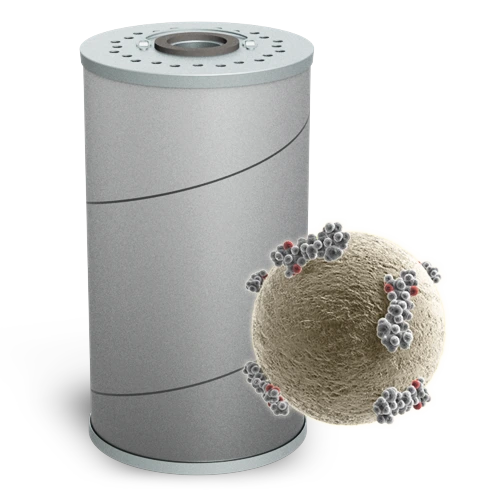
Our Fluid Technical Center is Your Answer Center
EPT Clean Oil’s Fluid Technical Center is a state-of-the-art lubricant research facility, offering specialized analysis and comprehensive evaluations. We take the routine out of oil analysis, providing a complete picture of your anti-wear hydraulic oil condition as per the guidelines provided in ASTM D6224.
From advanced testing to the expert interpretation of results, our team of professional and Ph.D. chemists are here to provide the data you need to make informed decisions about your critical assets. You can expect more when you partner with our Fluid Technical Center.
Our Lube Oil test package, applicable for anti-wear hydraulic oils includes:
- Acid Number
- MPC Varnish Potential
- Antioxidant and AW Additive Levels
- Viscosity (40°C)
- Water
- ISO Particle Count
- Dissolved Metals
- Fluid Color
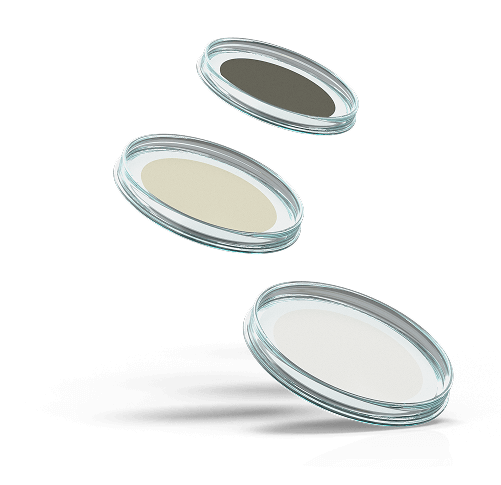
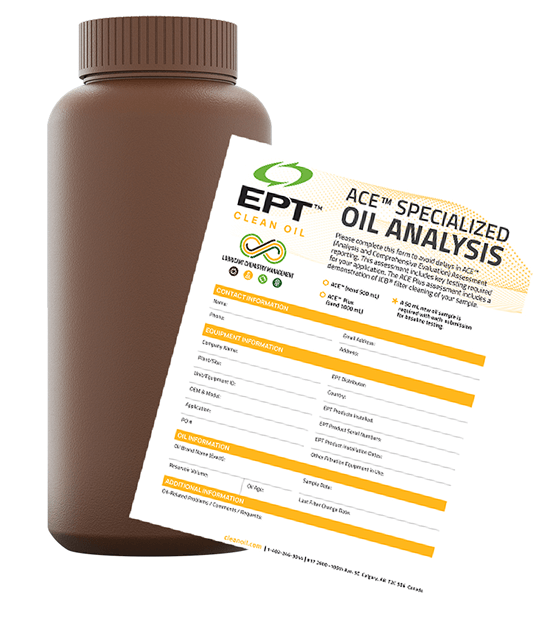
Submit an oil sample today, and let’s get a handle on your aeroderivative turbine oil’s condition.
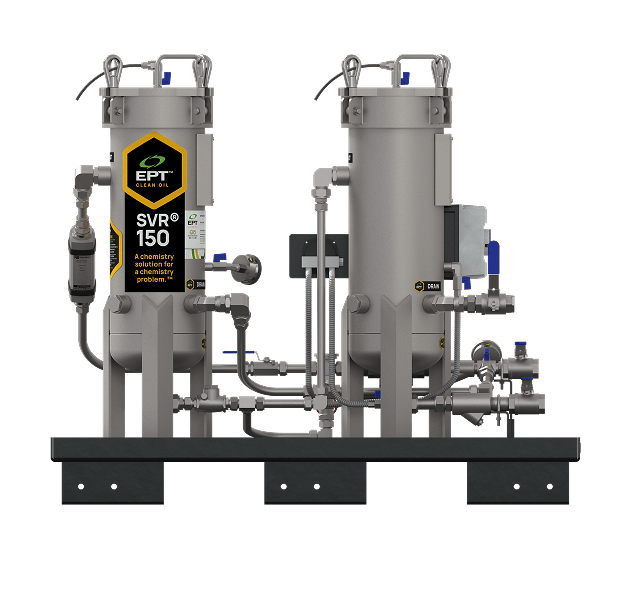
Meet the Ideal Match for ICB AW
SVR® for Dissolved Contamination Removal
While the presence of anti-wear additive packages protects hydraulic components, these mineral oil-based lubricants chemically break down over time. As operational demands fluctuate in the critical hydraulic systems, two variables are often overlooked: oxygen and heat. As oils chemically break down, acids attack the oil and mechanical components. Even more harmful, varnish precursors are generated, increasing the tendency for varnish deposits to form on mechanical surfaces. When this happens, the performance and reliability of hydraulic equipment suffer.
SVR® is an engineered lubricant conditioning system that works 100% of the time, targeting the underlying cause of lubricant failure: chemical breakdown. Backed by patented ion-exchange technology, ICB AW, SVR removes acids and dissolved oxidation material as it is generated. Only by managing oxidation levels can the root cause of lubricant deposits, or varnish, be eliminated.
SVR Features and Benefits
- Eliminates soluble varnish at the molecular level, preventing the oil from becoming saturated and forming varnish deposits
- Maintains consistent fluid quality and performance
- Improves hydraulic system performance and reliability (cycle times etc.)
- Restores low MPC varnish potential
- Manages fluid life with as little as 5% annual top-up annually
- Significantly extends oil life
- Avoids flushing and related downtime
- Eliminates the need for expensive after-market additives
- Engineer approved system designed to facilitate rapid approval and deployment
- Very low maintenance and time requirements – turn it on and let it run
- No downtime – SVR can be installed without an outage
SVR can be combined with TMR® N2, an engineered nitrogen generation system that removes water and oxygen within lubricant reservoirs. The combined approach of dissolved contaminant filtration and removing oxygen and water offers a comprehensive step-change in hydraulic oil maintenance, maintaining these oils in ideal operating condition – free of oxidation products, significantly extending oil life.
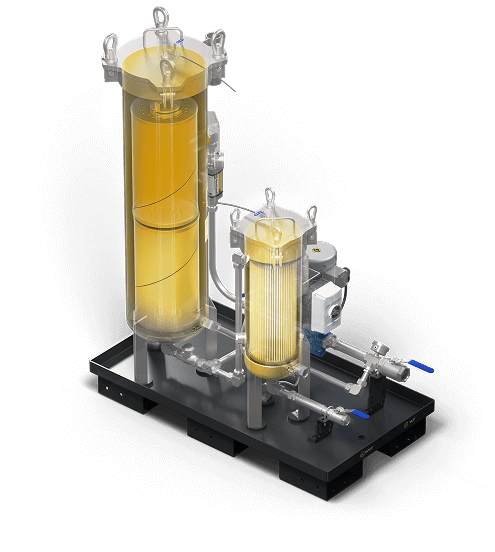