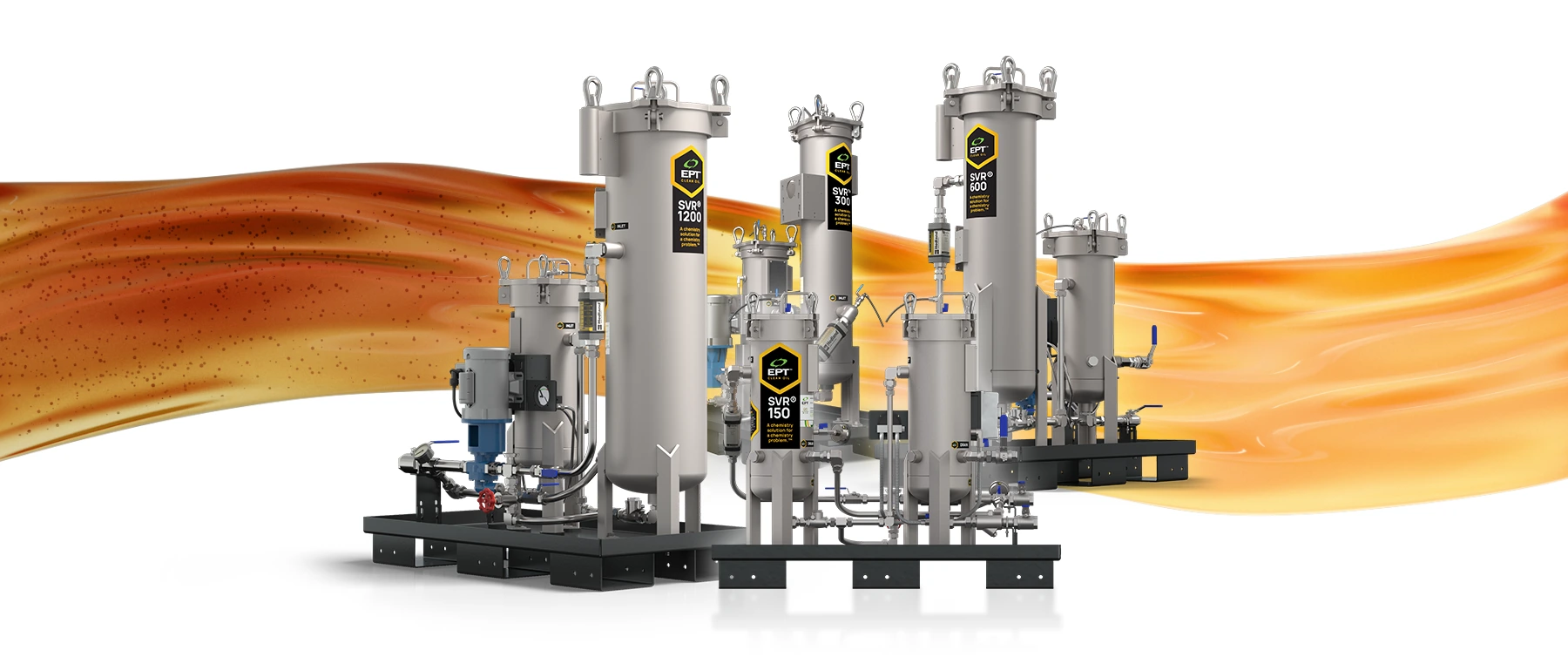
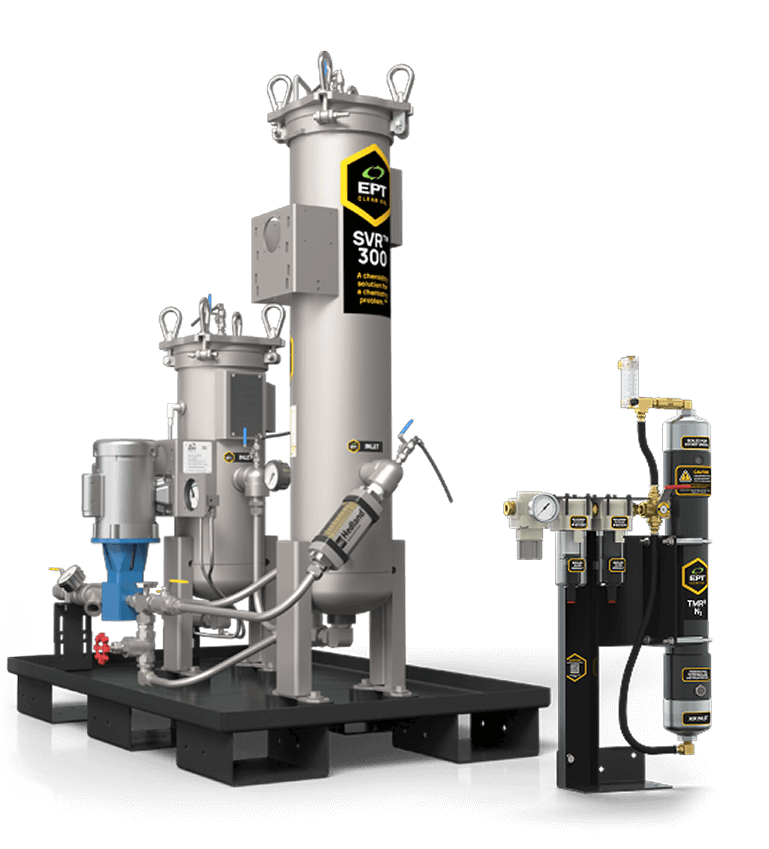
MEET SVR JET FOR AERODERIVATIVE TURBINE OIL
Coking is a failure mechanism that will affect most aeroderivative turbines in their operating life leading to premature mechanical overhauls and production losses. Coke begins as a dissolved oxidation by-product produced by high temperatures, water content and entrained oxygen before converting to a solid form and depositing on metal surfaces. Existing oil analysis and maintenance programs do not consider this contamination leading to high acid numbers, coking or varnish deposits, and shortened oil life.
SVR® JET is a skid-mounted dialysis-style lubricant conditioning system engineered to remove varnish, coking pre-cursors and particulate. When combined with our TMR® N2 water removal system, atmospheric water ingression is eliminated, dissolved oxygen is removed, and surface contact with oxygen in the lube oil tank is prevented, severely restricting oil breakdown. Backed by patented ion-exchange technology, ICB® JET, the acid number is reduced and managed, so jet lubes no longer have to be condemned based on the acid number.
The combined approach of dissolved contaminant filtration and removing oxygen and water offers a comprehensive step-change in jet lube maintenance, allowing aeroderivative turbine users to maintain oils in ideal operating conditions.
CASE STUDY
This case explores how advanced solutions with the SVR and ICB JET Filters helped reduce MPC varnish potential by 97% maintaining its acid number within the applications required range.
CASE STUDY
This case highlights how the implementation of SVR and ICB JET Filters improved MPC Varnish potential by 78% and 90%, respectively, eliminating oil breakdown problems.
SVR JET Features and Benefits
- Utilizes patented ICB® JET ion-exchange technology with over 30 million successful operating hours
- Removes dissolved oxidation by-products, or coking precursors, which are the feedstock from which all coking deposits are formed, breaking the lubricant deposit formation cycle, protecting bearings and other critical components
- Selectively removes acids and stabilizes the acid number providing optimal lubricant quality throughout the lubricant lifecycle while protecting mechanical components
- Protects hydraulic variable geometric control systems from sticking
- Resolves known issues when speed changes occur
- Protects against compressor surges and catastrophic engine failure
- TMR® N2 generates high purity nitrogen from a standard compressed air source to blanket the oil reservoir removing water and eliminating contact with oxygen, protecting the lubricant and eliminating catalysts that contribute to oxidation
- Quickly removes and maintains low water levels without consumable elements
- Quickly reduces entrained oxygen and promotes dissolved gas removal
- Eliminates the primary ingression pathway for water and metal contamination, thereby promoting chemical stability of the lubricant and reducing maintenance requirements
- Reduces ISO particle counts, protecting and extending roller element bearings trouble-free operating window
- Manufactured to ISO 9001 standards
- Low maintenance: Turn it on and let it run; that’s it
- No downtime – SVR can be installed without an outage
SVR JET owners gain access to a complete support program, including complimentary oil analysis and expert interpretation from our professional and Ph.D. Chemists until results have been documented. After results have been confirmed, owners are given the option to continue the analysis program for a quarterly fee.
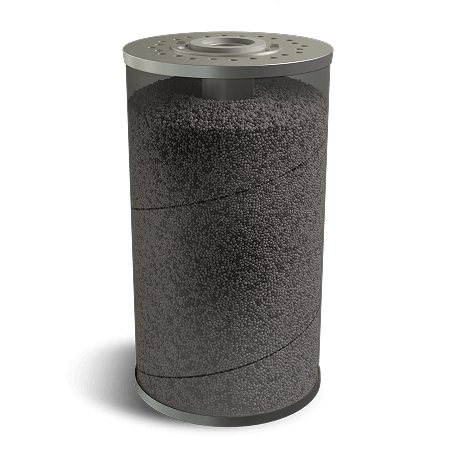
SVR JET Sizing Comparison Chart
SVR® HYDRO | SVR® 150 | SVR® 300 | SVR® 600 | SVR® 1200 | |
![]() | ![]() | ![]() | ![]() | ![]() | |
Reservoir Volume (Mineral Oil) | Minimum: 2,500 L/ 660 gal Maximum: 15,000 L / 3,963 gal | Minimum: 715 L / 189 gal Maximum: 2,870 L / 758 gal | Minimum: 1,440 L / 380 gal Maximum: 5,740 L / 1,516 gal | Minimum: 3,785 L / 1,000 gal Maximum: 16,278 L / 4,300 gal | Minimum: 5,980 L / 1,579 gal Maximum: 27,255 L / 7,200 gal |
Reservoir Volume (Synthetic Oil) | Minimum: 240 L / 63 gal Maximum: 960 L / 253 gal | Minimum: 480 L / 126 gal Maximum: 1,912 L / 505 gal | Minimum: 1,435 L / 379 gal Maximum: 5,680 L / 1,500 gal | Minimum: 2,272 L / 600 gal Maximum: 9,085 L / 2,400 gal | |
ICB Flow Rate | 19.0 lpm / 5.0 gpm | 2.0 lpm / 0.5 gpm | 4.0 lpm / 1.0 gpm | 12.0 lpm / 3.0 gpm | 19.0 lpm / 5.0 gpm |
System flow rate through high efficiency filtration | 38.61 lpm / 10.2 gpm | 8.0 lpm / 2.1 gpm | 8.0 lpm / 2.1 gpm | 38.61 lpm / 10.2 gpm | 38.61 lpm / 10.2 gpm |
ICB Filter Model | RO | RO FRF JET AW | JRO FRF JET AW | RO FRF JET AW | RO FRF JET AW |
Fluid Applications | Rust and oxidation turbine oil only at this time | Rust & Oxidation Turbine Oil (RO) Phosphate Ester Fluid (FRF) Aeroderivative Turbine Oil (JET) Anti-Wear Hydraulic Oil (AW) | Rust & Oxidation Turbine Oil (RO) Phosphate Ester Fluid (FRF) Aeroderivative Turbine Oil (JET) Anti-Wear Hydraulic Oil (AW) | Rust & Oxidation Turbine Oil (RO) Phosphate Ester Fluid (FRF) Aeroderivative Turbine Oil (JET) Anti-Wear Hydraulic Oil (AW) | Rust & Oxidation Turbine Oil (RO) Phosphate Ester Fluid (FRF) Aeroderivative Turbine Oil (JET) Anti-Wear Hydraulic Oil (AW) |
Other Proprietary Filters and System Requirements | TMR® AquaPurge Coalescer | For synthetic oils, it is advised to combine a TMR® N2 for water removal | For synthetic oils, it is advised to combine a TMR® N2 for water removal | For synthetic oils, it is advised to combine a TMR® N2 for water removal | For synthetic oils, it is advised to combine a TMR® N2 for water removal |
Contaminant Targets | Soluble Varnish Insoluble Varnish Oxidation by-products Water Particulate removal | Soluble Varnish Insoluble Varnish Particulate removal | Soluble Varnish Insoluble Varnish Particulate removal | Soluble Varnish Insoluble Varnish Particulate removal | Soluble Varnish Insoluble Varnish Particulate removal |
Electrical Options | General Purpose electrical only at this time | General Purpose with 50 Hz and 60 Hz electrical voltage options CSA Class 1 Div 1 Group C&D with 50 Hz and 60Hz electrical voltage options CSA Class 1 Div 2 Group A, B, C & D with 50 Hz and 60 Hz electrical voltage options IECeX and ATEX-approved configurations are available. Please get in touch with us for more information. | General Purpose with 50 Hz and 60 Hz electrical voltage options CSA Class 1 Div 1 Group C&D with 50 Hz and 60Hz electrical voltage options CSA Class 1 Div 2 Group A, B, C & D with 50 Hz and 60 Hz electrical voltage options IECeX and ATEX-approved configurations are available. Please get in touch with us for more information. | General Purpose with 50 Hz and 60 Hz electrical voltage options CSA Class 1 Div 1 Group C&D with 50 Hz and 60Hz electrical voltage options CSA Class 1 Div 2 Group A, B, C & D with 50 Hz and 60 Hz electrical voltage options IECeX and ATEX-approved configurations are available. Please get in touch with us for more information. | General Purpose with 50 Hz and 60 Hz electrical voltage options CSA Class 1 Div 1 Group C&D with 50 Hz and 60Hz electrical voltage options CSA Class 1 Div 2 Group A, B, C & D with 50 Hz and 60 Hz electrical voltage options IECeX and ATEX-approved configurations are available. Please get in touch with us for more information. |
For regular aeroderivative turbine oil maintenance, the desired flow rate is to exchange the fluid reservoir volume 4x per day with sufficient acid removal capacity for a given reservoir volume. Larger equipment may be preferred for recovery projects where higher Acid Numbers are present. The filter format used in the SVR JET 600 and SVR JET 1200 models is more cost-effective for these situations.
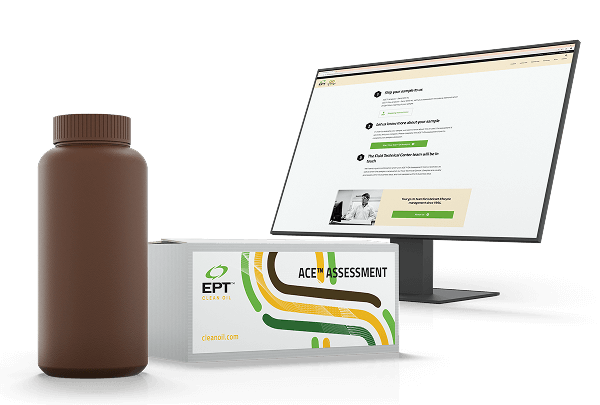
Get a Complete Picture of Your Aeroderivative Turbine Oil
EPT Clean Oil’s Fluid Technical Center is a state-of-the-art lubricant research facility, offering specialized analysis and comprehensive evaluations for your aeroderivative turbine oil.
Our Lube Oil test package, applicable for aeroderivative or jet lubes, includes:
- Viscosity (40°C)
- Water
- ISO Particle Count
- Dissolved Metals
- Fluid Color
- Acid Number
- MPC Varnish Potential
- Antioxidant Levels
Submit an oil sample today, and let’s get a handle on the remaining life of your aeroderivative turbine oil.